Digitalization technologies from Machines in Construction, Bosch Rexroth, and Mesh AG nominated for bauma Innovation Award
Three technologies vie to win bauma’s 2022 Digitalisation Innovation Award
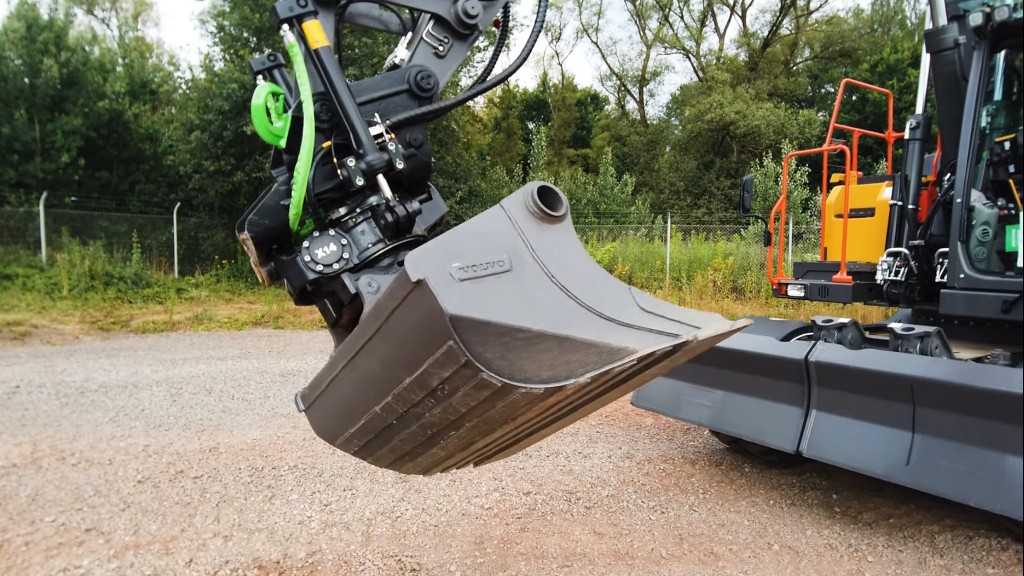
Digitalization has become integral to construction and the bauma 2022 Innovation Award showcases some of the latest technologies that further integrate technology on the job site.
Machines in Construction is nominated for its solution that connects machines and attachments from different OEMs with a standardized data interface, Bosch Rexroth AG is nominated for its haptic collision avoidance system that uses ultrasound to sense pending collisions, and Mesh AG is nominated for its MESH technology robot that creates complex reinforced concrete structures without formwork.
MiC 4.0 standardizes data for cross-OEM communication between attachments and equipment
A cross-machine and manufacturer-independent data interface between construction machines and attachments is required to digitalize construction sites.
With the Machines in Construction (MiC) collaboration project, 11 companies are developing the MiC 4.0 data standard for cross-manufacturer communication between attachments and construction equipment. The aim is not to standardize the existing mechanical, hydraulic, or electrical interfaces between the attachment and the machine. MiC 4.0's aim is to create a universal, uniform, and manufacturer-independent data interface between construction equipment and attachments. Through the cooperation of over 25 users and machine and tool manufacturers, a data interface via the CAN bus internet protocol is being defined under the name MiC 4.0 BUS, which can map use cases for communication between attachments and machines.
The use cases include identifying the tool during coupling so that information, such as serial number, tool type, and manufacturer, are transmitted to the machine and are available to evaluate machine and tool usage. The carrier machine can then be automatically adjusted to the tool. The MiC 4.0 BUS also provides the transmission of control data to optimize operation. By transmitting geometry data, operator assistance systems, such as working area limitations, can automatically work with the correct data.
Standardized data eliminates manual setup of the work tool
By automating the setup of the work tool, the MiC 4.0 BUS reduces the chance of incorrect operation of a work tool, which increases safety on the job site.
Both contractors and manufacturers can benefit from a "plug-and-work" system for complex work tools, which makes adoption of specialized tools more efficient and attractive.
The MiC 4.0 BUS also provides information on tool usage on the job site, including load and operating hours of the attachments.
The MiC 4.0 BUS has already been tested successfully on prototype machines and attachments from different manufacturers in April 2022. At bauma, a demonstration of the MIC 4.0 BUS will give visitors the chance to see the interface in action.
Following bauma, the MiC 4.0 BUS will be published and made available to other manufacturers.
Bosch Rexroth's haptic collision avoidance system
Using ultrasound, this assistance technology warns operators of an imminent collision using joystick vibration. The type and intensity of the haptic feedback provides information regarding the distance to the object. If the machine is operated with two joysticks, the system can even indicate the direction from which the object is approaching. Unlike purely visual or acoustic feedback, the operator's attention is unaffected while working, helping to increase reaction time.
Haptic collision modular assistance systems can help increase the safety and well-being of operators and workers on the job site. The warning reaches the driver's hands even in noisy environments and without need to watch a display.
For increased automation, Bosch Rexroth offers the option of automatic braking via the electro-hydraulically controlled GEMINI power brake valve. If the collision warning is not reacted to quickly, the necessary brake pressure builds up automatically.
The assistance system is made up of hardware and software modules from the BODAS ecosystem. Along with the software, these include the USS ultrasound sensors with an intelligent evaluation unit, Sense+ joysticks, DI4 displays, and RC controllers.
Virtual walls provided added safety
Virtual walls allow situation-specific workspace monitoring so that excavators, wheeled loaders, and other construction equipment can work much more safely and productively. The newly developed software provides the flexibility that the user needs to set up specific safety areas called virtual walls. Parameterization can be carried out via the BODAS touch display or with the help of a teach-in function.
Mesh AG's robot-assisted MESH technology
Mesh AG has developed a robot-assisted technology for the production of complex reinforced concrete structures without formwork. The production process offers new design potential for the construction industry while eliminating the need for costly and resource-intensive special formwork. The new robotic construction method helps make an important contribution to greater efficiency, sustainability, and design freedom in the construction industry.
MESH technology automates the prefabrication process
The MESH technology uses an automated prefabrication process that makes it possible to produce complex or curved reinforcement cages, which were previously manufactured manually. Reinforcing bars are continuously positioned, bent, and welded into a three-dimensional reinforcing grid by a robotic process. The reinforcement cages are positioned on the construction site and connected to each other, and the grid structure created with this method serves as formwork and reinforcement. The concrete can then be pumped into the reinforcement grids and can be surface-treated afterwards.
The MESH technology can be used for customized concrete structures and the production of complex forms for the building industry. The technology can also be used to build conventional concrete structures that can also be structurally optimized for material efficiency.
bauma Innovation Award categories
Additional Innovation Awards will be presented in the following categories: