SBM to showcase electric-hybrid crushing plants at bauma
The REMAX impact crushers and JAWMAX jaw crushers use an electric hybrid drive to cut diesel use by 30 to 50 percent
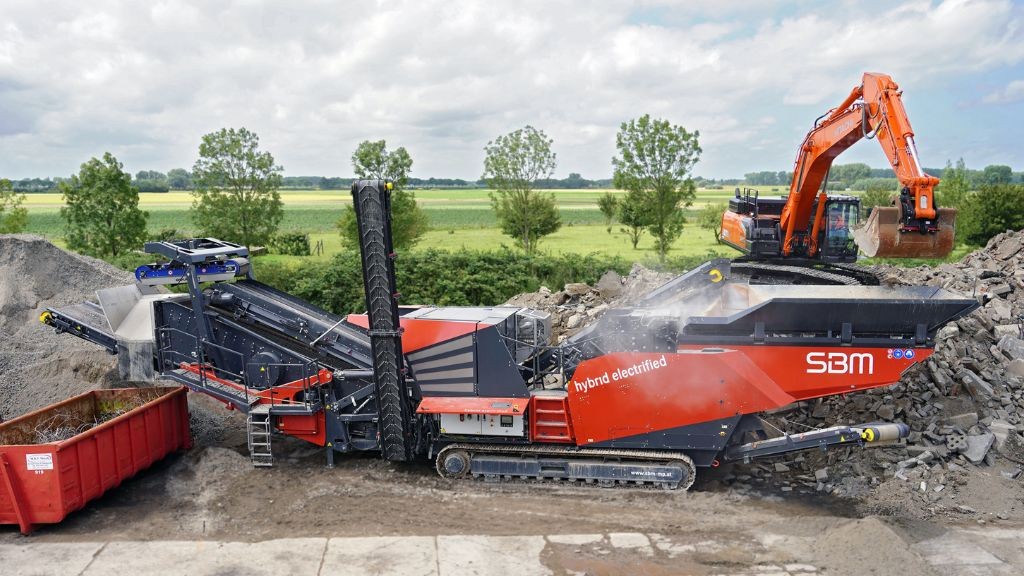
In 1950, Franz Wageneder, the owner of a gravel pit in Austria, laid the foundation for SBM Mineral Processing GmbH with his revolutionary swivel beam mill. "We proudly bear the initials of the revolutionary impact mill technology in our name, and of course, we will be celebrating '75 years SBM' in style at bauma," explains Erwin Schneller, managing director. "In fact, we have paved the way for many new technologies, which in turn have had a significant influence on the developments in both the aggregates sector and the building materials industry."
At this year's bauma trade show in Munich, SBM will focus on diesel-electric crushing plants. For more than 40 years, SBM has been focusing on creating efficient and environmentally friendly electric-hybrid drives for all power classes, including the REMAX impact crushers and JAWMAX jaw crushers. The company is also focused on developing intelligent automation; in two years, SBM will release its first autonomous crusher.
Mobile mineral processing
Shown at the pre-launch event for last year's bauma trade show, the REMAX 600 will continue to dominate the SBM mineral processing exhibition stand this year. The 600 t/h plant has been successfully placed across all major industries, according to SBM.
In addition to the performance of the 1400 impact crusher for natural stones and recycling with a feed size of 1000 mm, the economic sustainability in operations is a major callout: the fully hybrid plant with an EU-5 engine and a 520-kVa on-board generator consumes 30 to 50 percent less diesel in direct comparison to conventional diesel-hydraulic or only partially electrified large-scale plants. The REMAX 600 is an environmentally friendly cost saver with a plug-in option for connection to external power generators or grids.
Despite being fully equipped with an active double-deck primary screen, efficient longitudinal and cross discharge by magnetic separator, and up to three screening stages in the secondary screening unit with oversized grain recirculation, the REMAX 600 weighs less than 90 tons; as a one-piece unit, it can easily be moved from one location to another and is ready for use without needing any additional auxiliary equipment. The intelligent SBM Crush Control system supports the machine operator right from the set-up stage; it then monitors the entire production process and uses a comprehensive sensor system to ensure trouble-free and smooth material flow.
Solutions for compact sites
SBM will also present the JAWMAX 300 with a double-deck secondary screening unit. Pressure crushing remains the technology of choice for many contractors because of lower wear costs and lower fuel consumption. With a weight of less than 40 tons, the powerful 300 t/h jaw crusher, which has an inlet opening of 1000 by 600, now offers a flexible solution for inner-city recycling or for the local processing of smaller raw material stockpiles or stored residual materials.
With the reversible impact crusher SMR 13/7/4 and the vertical shaft impact crusher (VSI) V8, SBM will be presenting two individual machines in Munich that allow stationary plant operators to achieve higher value through the production of chippings or sand from oversized aggregates in the course of new constructions or upgrades.
The five SMR series, with feed sizes of 150 mm/200 mm, can be used as secondary or tertiary crushers with a high proportion of cubic final products for the concrete and asphalt industry. The V8 vertical shaft impact crusher is suited for the production of sands and fine chippings. A patented inlet control ensures low-dust production in the full-load range with high circumferential speeds of the rotor, as well, the design also guarantees a long service life.
Concrete solutions for any site
For over 25 years, SBM has been assisting with the creation of mobile and super mobile concrete mixing plants with its EUROMIX series. With the world premiere of the new SBM EUROMIX 1600 NOVA, the OEM is taking its plant program to the next level and is also presenting its smallest series with a new basic structure for the mixer unit in a pioneering design that thanks to new types of insulation offers even better year round properties and significantly more space for inspection and maintenance works.
Like its previous model, the EUROMIX 1600 NOVA has a hardened concrete output of up to 80 m³/h and is aimed at creating solutions for small to medium-sized construction sites with a daily requirement of up to 800 m³ of hardened concrete or liquid soils for backfilling. As a temporary addition to stationary installations, this plant produces high-quality mixes including special and recycled concretes, but can also be used permanently in the production of prefabricated parts as a space-saving solution.
Like all EUROMIX plants, it has a modular design and can be extended, the mixer and hopper units as well as the cement silos are transported on flat-bed trailers. At the construction site, a mobile crane with 2 to 3 workers is usually sufficient to install the entire plant ready for operation within one day.
The new basic design allows for 100 percent more space and improved accessibility with the fold-out extensions on both sides in the upper area of the weighing and mixer platforms. Safe access staircases and larger maintenance platforms make the mixer and all weighing and dosing equipment for water, cement, and additives easily accessible from all sides. Energy efficiency has also been improved, the enclosed structure made of 40-mm insulation panels and a fully insulated roof area ensures energy savings in normal operation. Due to an optional winter package with additional ground insulation, interior heating, and enclosure of the aggregate transfer area, even operation at low temperatures of +5° C and below is safe and economical.
The centerpiece of the EUROMIX 1600 NOVA is the BHS twin-shaft mixer DKX 1.67 with an output of up to 80 m³ of hardened concrete per hour. A newly developed SBM high-pressure cleaning system reduces the cleaning efforts and operating costs. In addition to the complete dosing technology system, only the aggregates are weighed externally by the discharge conveyor in the hopper unit, the compressor is now also integrated into the NOVA mixer unit. This makes the plant even more compact, increasing the efficiency and operational reliability of the entire plant. The standardized plug connections for the electrical equipment makes set-up quick and safe. The NOVA generation is also fully compatible with any control system.
Presentations at bauma
In Munich, SBM will also be presenting its range of easily movable and container-mobile mixing plants. In addition to the DYNAMIX 2500 presented last year, the VARIOMIX series deployed in constricted inner-city areas and the flexible LINEMIX containerized series, with hardened concrete outputs of up to 190 m³/h, which are used for long-term infrastructure projects in tunneling or power station construction, will be shown. SBM uses high-quality LINEMIX components for stationary horizontal mixing plants - the plant engineers design classic customized tower mixing plants based on the standardized TOWERMIX series.
A pilot project by SBM for the autonomous operation of concrete mixing plants will be presented at the event. Even without a mixing plant supervisor on site, truck mixers should be able to collect ordered deliveries from appropriately equipped plants as usual.
The production process, which is usually fully automated, is remotely monitored from another location or a central control room. Driver access terminals, camera systems, and sensors in the loading area ensure that the order is activated safely and monitor that the concrete produced has the correct quality. Once the delivery vehicle has been cleared, the concrete mixer and loading hopper can even be cleaned automatically.
According to SBM, the system, which can also be upgraded on existing plants, is currently undergoing practical trials and is designed to keep plant operation profitable without the need for expensive skilled workers.