How RodRadar is set to revolutionize excavation safety
Live Dig Radar shows excavator operators utility location and depth in real time
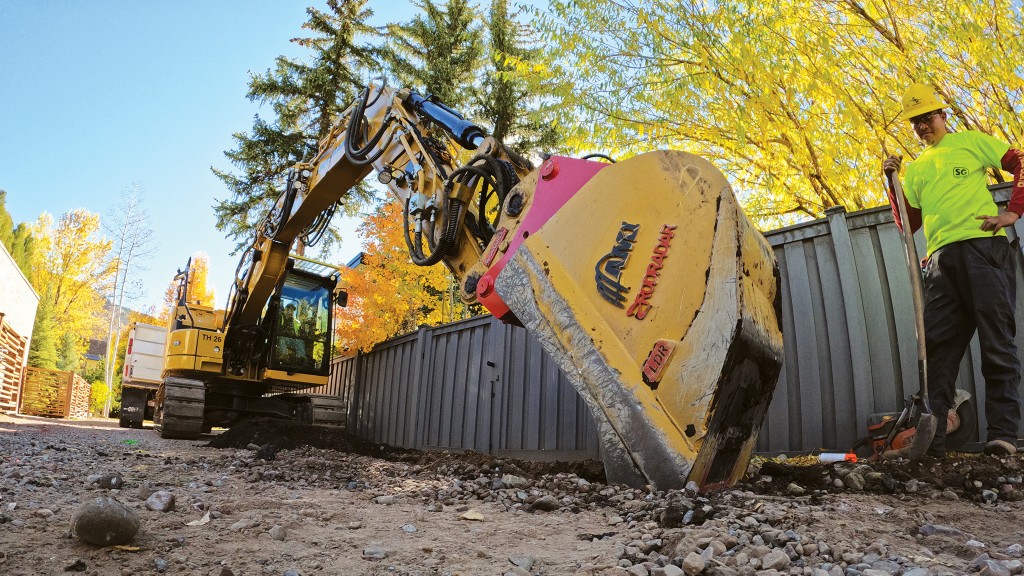
The dangers of utility strikes are well known, yet even when taking the most proactive measures, they can still happen – and result in potentially dangerous, even fatal, consequences for operators as well as project delays, immense liabilities, and disruption of services. The Common Ground Alliance estimates that damage during excavation to underground utility infrastructure costs the global construction industry billions of dollars annually.
RodRadar, an Israeli construction technology company, has developed and put to market a unique bucket and integrated ground penetrating radar (GPR) technology platform that automatically detects underground utility infrastructure in real time, on location, and without the need for expert analysis. The operator can view all information from inside the excavator cab. The Live Dig Radar (LDR) system is the first GPR system integrated directly into an excavator bucket, allowing an operator to scan below ground quickly and easily for utilities.
I spoke with Moshe Dalman, CEO and co-founder of RodRadar, and Yuval Barnea, the company's VP of sales and marketing, in March at CONEXPO about the LDR technology, its development, applications, and future of what has been described as the "Holy Grail" of earthmoving.
Making utility strikes a thing of the past
"RodRadar's mission is to make the $100 billion annual cost of utility strikes around the world a thing of the past," says Dalman. "Our approach is completely different from anything else you see in the industry. We're enabling the operator to see into the ground and have a tool that enables them to avoid utilities."
While GPR, of various forms, has been used on construction sites since the early 1980s, the data and imaging it produces typically requires an expert's interpretation. RodRadar's LDR system uses advanced algorithms to classify radar echo and determine utility location and depth. Capable of detecting any man-made material, including plastic (PVC) and metal, to locate gas, electric, water, fibre-optic, or telephone lines in any soil type.
In its initial development the RodRadar team had to reinvent GPR "to detect very shallow targets [utilities] in any ground condition, as well as to remove the interpretation from the radar. We wanted to give the operator the information and act on it immediately. Our algorithm is targeted to give a very simple response: is there or isn't there a target [utility pipe] and where is it?" explains Dalman.
The primary goal of RodRadar is to provide immediate and actual information that is acted on at the job site in real time. Current systems for surveying have limitations. "In ground conditions which are very challenging [the operator] might not see all the utilities, even when a job site has been scanned and surveyed conventionally, and is accurate, at the end of the day there are always utilities that can be missed. There is always information that is incomplete. Even when the locations are known, the operator can still hit them; we are the last line of defence," says Barnea.
"Contractors are very innovative. Once you give somebody a good tool, they understand very quickly how to use it," adds Dalman.
Aspen, Colorado-based contractor Shay Stutsman of Stutsman & Gerbaz Inc Earthmoving – one of RodRadar's first North American clients – understands that there is a constant knowledge gap in terms of where underground utilities are located. Stutsman has his LDR system on an excavator equipped with a grade control system; when an unmarked utility is discovered, they register the GPS coordinates and know where the utility is located. Stutsman recounted that when they got the Live Dig Radar unit, "A guy from the Aspen municipality saw what they were doing with it and said: ‘I am not going to hire anyone else unless he has the Live Dig Radar.'" Stutsman understands the impact of technology. With LDR you can finally see into the ground, and this completely changes excavation.
How to operate Live Dig Radar
To use the system, the operator positions the bucket at the starting point of where they plan to dig. The bucket is positioned in front of the dig location and moves toward the excavator over the area to be scanned. With the push of a button on the touchscreen, the LDR scans the earth for buried utilities as the operator slides the bucket along the ground. The in-cab LDR Visualize Monitor then displays a utility's distance and depth of utilities in the area where excavation is required. Alerts are sounded when utilities are detected, and a message on a red background of the monitor signals across the screen announcing, "Utility Detected." The system uses advanced algorithms to classify radar echoes and identify the utility.
As with any other GPR system, LDR's digging/visualizing depth is affected by soil conditions. Dalman explains, "In perfect conditions, like dry sand, it'll detect up to a metre, a metre and a half. In wet clay, it'll detect up to 40 to 50 centimeters. One of the things about this system is that it's not a mapping tool, it's not a surveying tool – it's a job aid. It's a tool to avoid hitting utilities. Like with any other tool . . . you have to adapt the way you operate it to the conditions of your job."
In applications that require more depth in excavation, operators are able to dig in layers, scan, and then dig again.
RodRadar partners with AMI
RodRadar was able to make the electronics and antenna in the bucket very rugged and sustainable. "We have collaborated with high-end bucket manufacturer AMI, known for its high-quality attachments, to build the perfect envelope that can both operate and protect the sensor. AMI is a perfect example of a company that understands they're not just selling steel but they can sell technology," says Dalman
RodRadar and AMI have developed three bucket sizes outfitted with LDR that have bolt-on cutting edges:
Type I is for excavators weighing 3,000 to 10,000 pounds and comes in widths of 18 or 24 inches.
Type II is for excavators weighing 10,000 to 24,000 pounds and comes in widths of 18 or 24 inches.
Type III is for excavators weighing 24,000 to 45,000 pounds and comes in a 24-inch width.
Where RodRadar goes next
Dalman sees opportunities to integrate its technology with OEM machine control systems that are on the market, similar to how the ADAS (Advanced Driver Assistance Systems) is used in the automotive industry, to improve the ways in which the operator is working but that no one sees on the ground. "We are in a unique position where we can integrate with everybody and everybody has a collective interest to integrate with this technology," says Dalman.
Dalman adds that the other significant future opportunity for RodRadar is to use the information found in the data collected by the Live Dig Radar system and to add more capabilities.
"For example, what type of utility is being located, what's the direction of the utility, even given an exact location. Just imagine the city of Montreal: somebody does something, exposes something, the city wants to know, what did they find? If it's an electricity line, the electricity company wants to know that their line is over there because the information they have is not up to date. We will be able to do a lot on the data side to leverage all that information."
Data capturing and management is a big part of RodRadar's future strategy, as Dalman explains: "We want to give value to the operators, to the contractors, to the municipalities, and everybody in the value chain who could use the data collected by the system."
This is a modal window.
Stutsman & Gerbaz Inc. is a contractor based out of Aspen, Colorado, that started operations in 1960. The company started out with a Caterpillar 993 track loader and an International tandem truck. As the company grew, they added more machines to their fleet in order to work on more advanced projects. That desire to work on tough projects continues today with Shay Stutsman, the president of Stutsman-Gerbaz Earthmoving, who saw an opportunity to utilize RodRadar's Live Dig Radar system on a City of Aspen project faced with the difficulties of digging near buried utilities.
"It changes excavation. This changes earthmoving," says Shay Stutsman in the above video. "Nobody can see in the ground – up until now. Now we can see in the ground. So really, there's no excuse for us to have to worry about if there's something undetectable."
Watch the video above to see RodRadar's technology in action and hear more from Shay Stutsman about the abilities Live Dig Radar can bring to a job site.