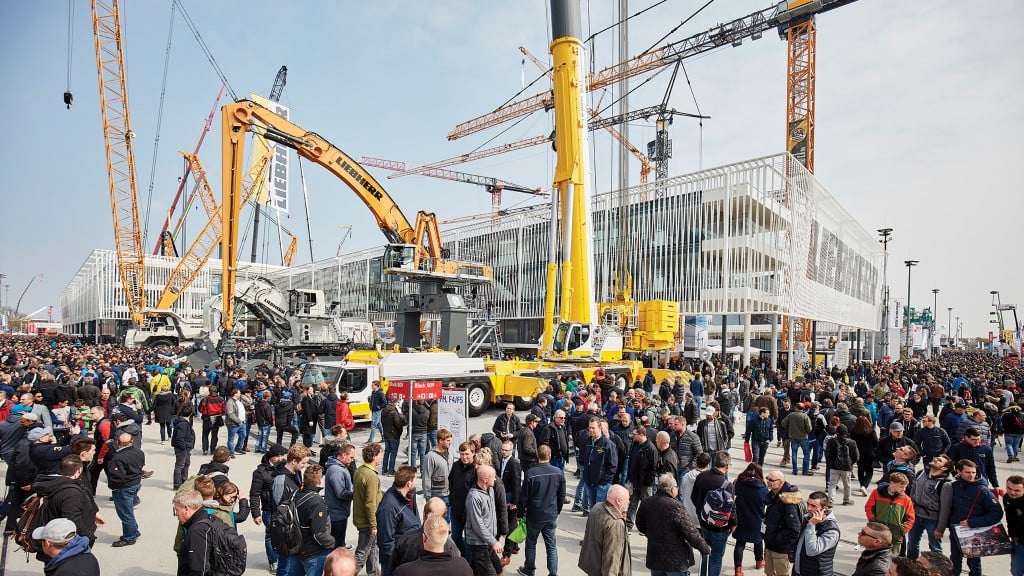
After an extended delay due to the pandemic, bauma is back this October to deliver new equipment introductions, technology innovations, live demonstrations, and all the spectacle and unparalleled scale that one of the world's largest trade fairs has to offer. bauma is an opportunity for the world to come together for a truly global experience in Munich, and in this preview we take a peek at the latest equipment introductions and technologies that manufacturers have teased ahead of the show, along with a special look at the slate of electric machines that will be on display.
International trade show is opportunity to address industry's biggest challenges and celebrate advancements
Autonomy, the connected job site, and electrification are all themes that bauma organizers have highlighted ahead of the show, and every three years bauma is an opportunity to benchmark the progress of the latest technology for the construction industry. Autonomy and connected job site technology are two of the hottest areas of development, but both face barriers to wide-scale use and maximized potential. A significant challenge to be managed is data and communication standardization – how can a mixed, multi-manufacturer fleet communicate?
A working group that was established at bauma 2019 is tackling that problem with the development of an open-source solution and will present its progress toward creating data standardization in the innovation hall – and will also provide a practical demonstration of its work.
The advancement of electric equipment is another great example of new technology development that can be measured against the bauma cycle. At bauma 2019, electric equipment was still in its infancy – a few high-profile machines were announced, but there was hardly an electric-powered machine around every corner. This year, electric machines will be present across the show covering a diverse range of categories including earthmoving, compaction, cranes, crushing, and more. Reduction of greenhouse gas emissions, particularly in urban areas, and reduction in noise levels are highlighted by all of the manufacturers introducing electrically powered machines at bauma 2022, and several manufacturers are displaying full lineups of electric equipment – rather than a single electric option within a lineup of conventionally powered machines. Let's take a look at some of the electric machines announced ahead of the show.
Bauma 2022 electric equipment introductions
Mecalac
Mecalac will display what it calls the industry's first full range of medium-size electric earthmoving equipment for urban job sites. This lineup includes the 11-ton e12 excavator, the 1,000-litre es1000 swing loader, and the 6-ton ed6 dumper, as well as the 300kWh on-site high-power battery charging solution M-Power. This lineup will enable an operation to carry out all earthmoving tasks (digging, loading, and transporting) on an urban job site with emission-free machines. A prototype version of Mecalac's e12 excavator was demonstrated at past European trade shows.
According to Mecalac, the primary challenge in developing medium-sized electric machines is the optimization of power management. To overcome this challenge, Mecalac had to design the hydraulic distribution system, as well as the energy management of auxiliary systems (such as heating and air conditioning), to drastically reduce energy consumption without compromising performance. These machines have also been designed with consideration for the habits of operators who are used to machines with combustion engines and not the instantaneous power that an electric machine delivers when the throttle is pressed – habits that otherwise may not be compatible with optimizing battery performance on electric machines.
Wacker Neuson
Wacker Neuson's zero-emission portfolio includes battery-powered rammers and plates, an internal vibrator system for concrete consolidation, and electric dumpers, wheel loaders, and excavators. At bauma 2022, Wacker Neuson will display the third-generation of its E-wheel loader WL20e with a lithium-ion rechargeable battery. The wheel loader will feature a completely closed cab for the first time. A brand-new addition to Wacker Neuson's battery-electric lineup is the first battery-powered, reversible vibratory plate with direct drive system. The switch in the travel direction is done via hydraulic adjustment, as in conventional models. The vibratory plate APU3050e features an operating width of 50 cm and a centrifugal force of 30 kilonewtons. Wacker Neuson highlights its maneuverability and says it is ideal for use in narrow trenches.
Hitachi
Hitachi Construction Machinery (Europe) NV will introduce a five-tonne battery-powered excavator for the European market.
The new ZX55U-6EB is designed for maneuverability in confined spaces and features a short tail swing. It also provides a high level of performance equal to its diesel-powered counterpart, according to Hitachi. Applications include urban construction sites, residential building, and waste material handling projects.
End users can choose between a battery-powered operation, using 39kWh lithium-ion batteries, and a wired operation, which allows the machine to work while charging.
Hitachi says that end-users can expect reduced maintenance costs and downtime compared to diesel-powered excavators. The status of the electric drive system, including battery level and motor load factor, can be monitored remotely. Reduced external sound levels (91dB) allow for greater flexibility for working times and options. The rear camera can be used to monitor the secure connection of the cable during wired operation.
Firstgreen Industries
Firstgreen Industries, formerly known as Kovoco, will display its all-electric Elise900 skid-steer loader and its compact MiniZ400 tracked loader. Firstgreen says that both of these machines excel at delivering the load capacity, hinge-pin height, stability, and ground clearance needed on job sites. It produces zero emissions, runs silently, and offers low operating costs to owners.
Liebherr
Liebherr, in launching six new zero-emission unplugged machines including piling rigs, drilling rigs, and crawler cranes, is building upon its previous unplugged introductions, which includes two crawler cranes and a drilling rig. The battery on each of these machines is charged using a conventional job site electric supply and operation can continue as normal while charging.
The new piling rigs are the LRH 100.1 unplugged and LRH 200 unplugged; the LRH 200 is an all-new model that closes the gap between the LRH 100 and LRH 600 in Liebherr's series of piling rigs. A 200-kWh battery pack ensures that the unplugged models can operate in battery mode for 4 to 5 hours in average pile driving applications. A 400 kWh option is available for 8 to 10 hours of operation.
When equipped with Liebherr's H 6 hydraulic hammer, the LRH 200 and the LRH 200 unplugged can lift piles up to 24.5 m long weighing 16 tonnes. With a working radius of up to 8.7 m, the machine does not have to be constantly moved.
The LB 25 unplugged and LB 30 unplugged drilling rigs are identical in weight, transportation needs, and application capability to their conventional counterparts. Thanks to the optional extension of the drilling axis, the machines can be deployed for drilling diameters of up to 3.4 m. The optional rear support and the new design of the modular rear counterweight ensure higher stability and longer service life. Both machines are available in a Low Head version with a total height of 14.1 m, or as Ultra Low Head with only 7.7 m. The battery is designed for a working time of four hours in Kelly operation. Whether in battery or plugged-in operation, the drilling performance remains unchanged.
The LR 1130.1 unplugged and LR 1160.1 unplugged crawler cranes have the same performance capability and are operated the same as their conventional counterparts.
The battery is designed for an average lifting operation of eight hours. These cranes can recharge in 2.5 to 4.5 hours, and performance can be increased by 20 to 60 percent using optional additional batteries. In idling mode, the sound level of three unplugged cranes is equivalent to that of a normal conversation on the job site – only 60 dB.
Dynapac
Dynapac plans to start full serial production of electric rollers by the end of 2022 with the introduction of the CC900 e and CC1000 e. Dynapac says that both rollers will deliver increased cost savings, feature fewer moving parts, and require less maintenance. The CC900 e and CC1000 e also deliver the same static linear load, amplitude, gradeability, and travel speed as the diesel-powered models they are based upon.
Based on a typical 1.6-ton roller's work day, which would normally consist of repair work with hand-laying from a spreader or sometimes following a small-sized paver on sidewalks/ bicycle lanes. This comes out to a compaction of about 70–80 tons of asphalt per day at a layer thickness of 40–50 mm – roughly 700 square metres. Based on this work load, Dynapac says that the battery on these new rollers will last for a full day of work. In 90 percent of its test cases, about 20–30 percent of the battery charge was left after the work day was over.
With a fast charger, 400-volt/3-phase system, it takes 1.3 hours to reach 80 percent of charging level. The 230-volt/1-phase charger needs six hours to reach 80 percent of its charging capacity.
Keestrack
Keestrack will be showing its ZERO-drive equipment, which the company debuted at its Norwegian demo days. Unlike the company's hybrid equipment, the ZERO machines do not have a combustion engine, only electric motors, which Keestrack says deliver high efficiency with low energy requirements and require very little maintenance. The ZERO-drive equipment lineup includes: the R3e, K4e, K5e, K6e, K7e, S5e, B5e, and the new Tracked Apron feeder A6 which will also be at bauma.
The Keestrack tracked Apron feeder A6 functions as a buffer with its 15-cubic-metre hopper and makes sure the following machine, usually a stacker, is evenly fed. The A6 can be connected to other e-machines and is easy to position with two drive speeds and the hopper can turn 90 degrees, so it is possible to use the hopper in line to the tracks or in 90-degree position.
Keestrack will also display the B5e ZERO jaw crusher. Without an on-board combustion engine, the B5e will be driven only by electric motors.
Hamm
Hamm has been working toward fully electric machines for several years now, a process which has included the company's Power Hybrid roller from the HD+ series. Now, with eight electrified tandem rollers, Hamm is entering its first fully electric machines into the market. According to Hamm, when operating the electric tandem rollers operators will see no difference from the diesel-powered models, and compaction power is identical.
A maintenance-free lithium-ion battery with a capacity of around 23 kWh supplies power via a 48 V on-board power supply. The energy released from the drive engines and vibration motors when braking is also recovered. Hamm says that these rollers can work the entire day without recharging. To charge the battery, plugs for 230 V and 400 V mains power are included on-board.
The electric drive also drastically reduces noise emissions, making electric tandem rollers ideal for areas where compaction needs to be completed with as little noise as possible.
Kleemann
Kleemann will introduce its MOBIREX MR 130(i) PRO impact crusher. The plant is used as a primary and secondary crusher. This all-electric-drive plant, with the option for external power supply (resulting in CO2-free operation), requires low energy consumption per ton of final product. The optional large double-deck secondary screening unit permits the production of two classified final grain sizes. The MR 130(i) PRO covers a wide range of applications in natural stone and recycling. With its heavy rotor and powerful electric 250 kW drive, the crushing unit guarantees a very high and stable throughput, says Kleemann. A continuous crusher load is guaranteed by the Continuous Feed System (CFS).
Bobcat
Bobcat will show its T7X all-electric compact track loader concept at bauma 2022. First introduced at CONEXPO 2020, Bobcat says it is seeking feedback from customers around the world to better understand different application opportunities. The 62-kWh lithium-ion battery pack delivers four hours of continuous use, and operators are able to manually tune the performance of the T7X for specific jobs, including the ability to vary its drive speed while at full torque. The other feature that stands out is what isn't needed to operate the T7X – it requires virtually no fluids, as the hydraulic work group has been replaced with an electrical drive system consisting of electric cylinders and electric drive motors. The only fluid that this CTL needs is coolant.
Equipment introductions and innovations at bauma 2022
In addition to the range of electric machines, manufacturers have previewed a number of additional innovations and introductions ahead of bauma 2022. The following is a preview that scrapes the surface of the new equipment that visitors will be introduced to at the show:
Hyundai
Hyundai Construction Equipment will display its HW155H concept wheeled excavator powered by a hydrogen fuel cell, which the company says is more compatible with larger construction machinery than the lithium-ion batteries currently being employed in smaller electric mini excavator models. This 14-tonne machine delivers eight hours of operation with a 20-minute refuelling time and is based on hydrogen commercial vehicle technology – and the only emission is water.
Hyundai Construction Equipment (HCE) began development of this driveline in 2020 in cooperation with Hyundai Motors and with Hyundai Mobis. The three companies committed to develop a hydrogen fuel cell to power forklifts and medium/large excavators over the coming years.
Unlike a conventional wheeled excavator, where a diesel engine drives a hydraulic pump to power the machine, the hydrogen excavator has a fuel cell mounted in the rear of the upperstructure which creates electrical energy. This is used to power the hydraulic pump to drive the machine as normal.
Hyundai will also focus on advanced technologies for the construction industry at bauma. Features of its exhibit will include a range of existing smart solutions integrated with Hyundai's vision for the future; Hyundai Connect, a total solution for effective equipment management; and future eco-friendly energy solutions, including electric machines and the hydrogen fuel cell development.
Bobcat
Currently being tested in the U.S., Bobcat's Quad Track concept allows the wheels of selected Bobcat skid-steer loaders to be easily replaced with four individual track pods, effectively converting them into tracked loaders. Bobcat quad tracks will enable skid-steer loaders to easily adapt to different environments that require increased flotation, reduced ground pressure, and better traction on wet ground. Bobcat says this concept provides a smoother ride compared to two-track compact track loaders. The challenge in putting Quad Tracks on a skid-steer loader is ensuring that they can withstand side-to-side as well as forward and backward movement.
The transition to Quad Tracks is completed by removing the wheels, adding an oscillation bar to limit total oscillation, and attaching track pods to the existing axles. The machine can easily be converted back to wheels.
BOMAG
BOMAG will display a range of equipment for compaction at bauma, along with its connected technology. A key highlight is BOMAG's new generation of its Smart Line (SL) single-drum rollers, with smooth or padfoot drums, which will be displayed for the first time at bauma. The single-drum rollers feature an interface to BOMAG's BOMAP app. The company says that this smart helper for tablets and smartphones increases efficiency with real-time maps for Surface Covering Dynamic Compaction Control (SCDCC) and simplifies transparent, digital job site documentation. BOMAG says that its new Smart Line single-drum rollers are characterized by their large amplitudes, optimum weight distribution, and high linear load. These result in ideal depth effect and reliably high surface coverage when compacting sand, gravel, crushed rock, and poorly cohesive soils.
Komatsu
Komatsu will show a range of equipment including a mining excavator and yet-to-be-revealed electric equipment. Komatsu says that these electric introductions are part of its engagement with reducing carbon emissions. Komatsu will also focus on smart construction solutions. The Komtrax Next Generation and Komtrax Data Analytics booths will explain how Komatsu's wireless monitoring system can simplify decision-making for all those who work to deploy equipment effectively or to improve fuel efficiency, to maximize productivity or to plan maintenance. In addition, Komatsu says that its Virtual Stand will transport visitors to a near future, providing a look at upcoming innovations for its wheel loaders.
Wirtgen Group
The Wirtgen Group will display the latest innovations from its Wirtgen, Kleemann, Vögele, and Hamm lines. Wirtgen Group will also offer a Technology Zone exhibit devoted to smart production systems. Witrgen says that digitization and connected system solutions are important drivers in the development of the overall road construction process chain, and will show application-specific core technologies as well as digital solutions and technologies that are already available.
In addition to Hamm's line of electric rollers and Kleemann's electric-drive crushing plant, other machine innovations on display will include the Mill Assist machine control system, which Wirtgen says assures sustainable and efficient machine operation in its new generation of compact milling machines. Wirtgen will also display its KMA 240i cold recycling mixing plant, which the company says makes it possible to produce high-quality mixes from recycled construction materials, but also cement-treated base layers.
Vögele will show its new Dash 5 generation of road pavers. Also on display will be the SUPER 1900-5(i) and SUPER 2100-5(i) Highway Class pavers and the latest generation of the AB 500 and AB 600 extending screeds.
Liebherr
Liebherr will display a range of machines across its entire construction portfolio at bauma, including cranes, excavators, energy storage solutions, and more.
Highlights include its Generation 8 wheel loaders – both compact and medium-size models. Liebherr says that these new wheel loaders deliver a significant performance boost compared to their predecessor models. In the compact range, Liebherr will show the L 504 Compact and L 508 Compact. The new L 504 Compact is the smallest wheel loader offered by Liebherr. The L 546 model will represent the medium-sized wheel loader series at the Liebherr stand. Visitors will be able to see intelligent assist systems, such as the upgraded, high-performance Skyview camera system, and active person recognition.
Liebherr recently re-entered the ADT market, and its Red Dot Design award-winning TA 230 Litronic articulated dump truck will be displayed for the first time at a trade show. Liebherr says that this powerful, robust, and efficient machine was developed for tough off-road applications and is ideal for earthmoving, quarries, and mining.
Liebherr is also presenting a hydrogen direct injection system (H2-DI) for heavy-duty internal combustion engines at bauma. With this technology, the Liebherr Group aims to achieve a maximum power density to match the power of a conventional combustion engine. Liebherr says that hydrogen-based drives are one important part of its work on alternative drive concepts for on- and off-highway applications.
Takeuchi
Takeuchi will display three new compact excavators at bauma: the TB335R, TB350R, and wheeled TB395W.
The TB335R is a compact, short-tail-swing excavator with minimal overhang behind the operator's seat, making it ideal for working in tight or confined spaces. Takeuchi says that it also provides outstanding stability rarely found in a short tail swing machine, along with smooth, intuitive controls that help operators tackle tough jobs with ease. The TB335R has an operating weight of 3,760 kg (8,290 pounds). The new TB350R is a larger version of the TB335R with an operating weight of 5,085 kg (11,210 pounds).
The new TB395W wheeled excavator weighs 10,150 kgs. (22,375 pounds) with an 85 kW/113.9 hp engine. Takeuchi says that its 4,095 mm (13.4-foot) digging depth and 8,530 mm (28-foot) cutting height make it particularly useful on construction sites. It also offers a maximum bucket breakout force of 58.9 kN (13,240 pounds), a maximum arm digging force of 39.7 kN (8,925 pounds), and a traction force of 57.8 kN (12,995 pounds).
Bell
Bell will display its autonomous ADT platform. The company says that autonomous ADT development consists of three elements: remote operation, external sensors that become the eyes and ears of the machine, and sophisticated site control software that manages the operation based on communication with the other two elements. The company has partnered with third parties on its autonomous development, and Bell anticipates that providing autonomous-ready ADTs will be a core part of its business in the future.
Bell says that it also wants to provide a vehicle that can be fitted and controlled with a guidance system from any number of manufacturers with easy integration, as autonomous applications are industry-specific and require surveying and guidance by an industry expert. The company says that it wants end-users to be able to choose a guidance solution that they are most comfortable with and that can be fitted to all the machines in the work cycle, adding that keeping the guidance system independent of the OEM gives customers the flexibility to run a mixed fleet.
In its autonomous ADTs Bell provides a standard cab with no extra hardware taking up space to create an environment where manual, remote, or autonomous operation is interchangeable.
In most cases an autonomous operation will need the site to be set up differently; there may be special traffic control measures, berms, or even different roads needed. Bell currently has an autonomous-ready solution available for customers who are interested in doing proof-of-concept work in their application.
Manitowoc
Manitowoc will display its new Grove GMK6400-1 all-terrain crane. Like its predecessor GMK6400, the new GMK6400-1 has a maximum capacity of 400 tonnes and a main boom of 60 m. New features include an improved hydraulic system with faster flow to provide quicker operating speeds and even smoother movement. Also added to the new 400-tonne machine is the Crane Control System (CCS) and MAXbase variable outrigger positioning system.
SBM
SBM Mineral Processing will display the new track-mobile impact crusher REMAX 600. With a feed capacity of 600 tph, a 1400-impact crusher for material feed sizes up to 900 mm, and a maximum total weight of 75 tons, depending on the equipment, the plant can produce up to five fractions in one cycle. Triple wind sifting and the efficient optional overbelt magnetic separator with longitudinal discharge ensure the high purity of final products, even in recycling applications, according to SBM.
SBM calls the REMAX 600 a technology platform for fully automatic production monitoring and control that it is currently developing in co-operation with researchers of the Montanuniversität Leoben, Styria. Based upon an innovative sensor system and video technology, powerful communication, and IT networks, as well as technological innovations such as automatic gap adjustment, SBM says that "artificial intelligence" has found its way into mobile processing and that this "autonomous crusher" will help end-users and operators make decisions and will permanently support efficient operation, assure optimum product quality, and save energy and costs during crushing.
Company info
Parc des Glaisins 2 av. du Pré de Challes
Annecy-le-Vieux,
FR, F-74940
Website:
mecalac.com/en
131 Savannah Oaks Drive, Building B
Brantford, ON
CA, N3V 1E8
Website:
wackerneuson.com/ca
1015 Sutton Drive
Burlington, ON
CA, L7L 5Z8
Website:
liebherr.com/en/can/about-liebherr/liebherr-worldwide/canada/liebherr-in-canada.html
6030 Dana Way
Antioch, TN
US, 37013
Website:
wirtgen-group.com/america/en-us/products/kleemann
Phone number:
(615) 501-0600
6100 Atlantic Blvd.
Norcross, GA
US, 30071
Website:
na.hd-hyundaice.com
Phone number:
877-509-2254
6030 Dana Way
Antioch, TN
US, 37013
Website:
wirtgen-group.com/en-us
Phone number:
615-501-0600