Kal Tire showcases mining tire management solutions that improve sustainability at MINExpo 2021
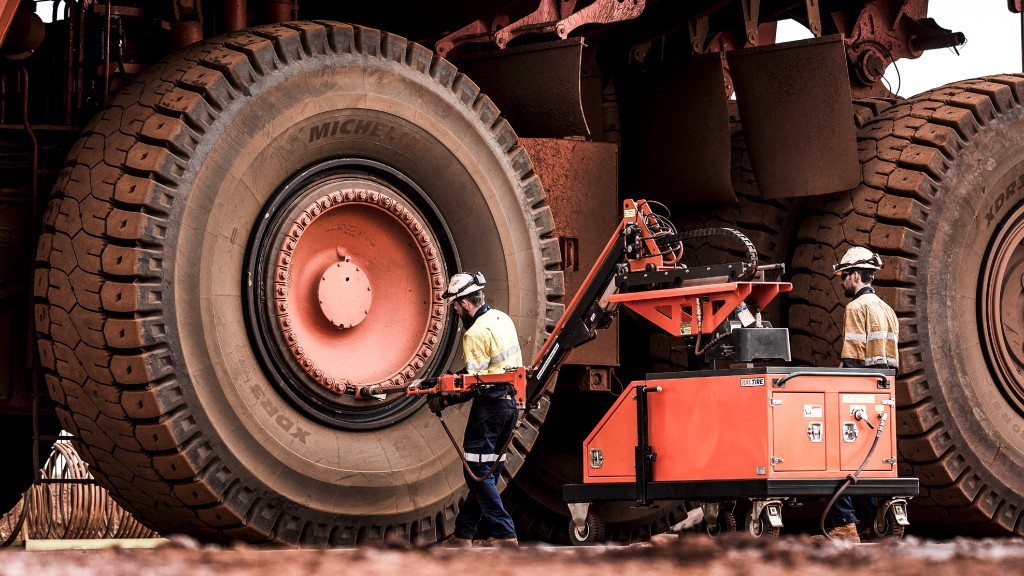
For Kal Tire's Mining Tire Group, it has been a year of firsts and looking to the future of what it means to provide mining tire management solutions that improve sustainability and tire performance as well as safety and productivity. At MINExpo 2021, the company showcases several unique new offerings, including its thermal conversion OTR tire recycling facility, two first-of-the-kind tools that will change how technicians work safely around the wheel, and a program that provides customers with actual accredited data on the emissions savings of retreading, Ultra Tread and Ultra Repair.
"We're in a time when mines are acting on new and forward-thinking commitments to the environment, people and communities touched by mining operations," says Dan Allan, senior vice president, Kal Tire's Mining Tire Group. "The emphasis on ESG issues is exciting in many ways because we're showcasing several big and bold solutions that align with this future-minded focus. We're developing offerings that don't exist so we can protect people from risk and bring mining operations even greater safety, productivity and sustainability."
One of the biggest projects Kal Tire will celebrate this year is reaching full production of its new OTR tire recycling facility in northern Chile. The thermal conversion process uses heat and friction to induce a reaction that converts tires into their base elements: Each day, one of two reactors will have the capacity to convert five 63" tires weighing nearly 20,000 kg into 6,500 litres of alternative fuel, 4,000 kg of steel and 8,000 kg of carbon black as well as enough synthetic gas to fuel the plant itself for seven hours.
Kal Tire is also helping customers to act on and demonstrate environmental stewardship through its Maple Program, which provides actual data on oil and carbon emissions saved when they retread tires compared to buying new. The foundation of the Maple Program is Kal Tire's custom-built carbon calculator that was developed after analyzing more than 125,000 production records spanning 20 years, and is validated by SCS Global Services, an international leader in third-party environmental certification.
New in 2021 is the Maple Program's addition of Ultra Repair: mines that use Kal Tire's exclusive process for repairing large injuries to tires that would otherwise be scrapped can now quantify and report on the environmental benefits of using Ultra Repair versus buying new tires.
Since opening its Innovation Centre in western Canada, Kal Tire has developed several tools now in use that help protect technicians from risk and improve efficiency and productivity, including the Gravity Assist System, Ram Mount Tool, Air Valve Protector and others. At MINExpo, Kal Tire is showcasing two tools to improve safe work around the wheel: Wheel Inspection and Magnet Clamp.
The Wheel Inspection allows mines to inspect wheels on-site as the mobile unit scans and indicates cracks along weld lines or ring grooves that could compromise wheel integrity and safety. As earthmoving equipment is subjected to ever-increasing loads and speeds, and wheels risk fractures in sensitive areas, wheels play an integral role in mine safety. The Wheel Inspection also saves mines from sending wheels great distances for testing.
The Magnet Clamp allows tire technicians to safely perform the last, and most dangerous, step of removing an OTR tire and wheel assembly as a remote-controlled clamp secures and then releases the last two wheel bolts. Typically, for this final step, technicians must stand underneath a tire manipulator forklift bearing the weight of the assembly.
"We believe every team member should be able to return home safely at the end of the day, and that's why we've invested in the research and development of these tire management tools. They prove how thinking about new ways of working and having tools designed for the job can make such a difference for technicians' safety, and also create efficiencies and help trucks stay in production," says Allan.
TOMS—the company's proprietary Tire Operations Management System, now in use on 130+ mine sites— could also be described as a productivity tool as it enables planned maintenance and turns tire inspections into actions. With TOMS, issues can be caught early to help prevent unplanned tire work and meet tire performance goals. Teams can also use both real-time performance data and company-wide tire management data to identify more ways to improve uptime.