Remote monitoring smooths out auto lube system management
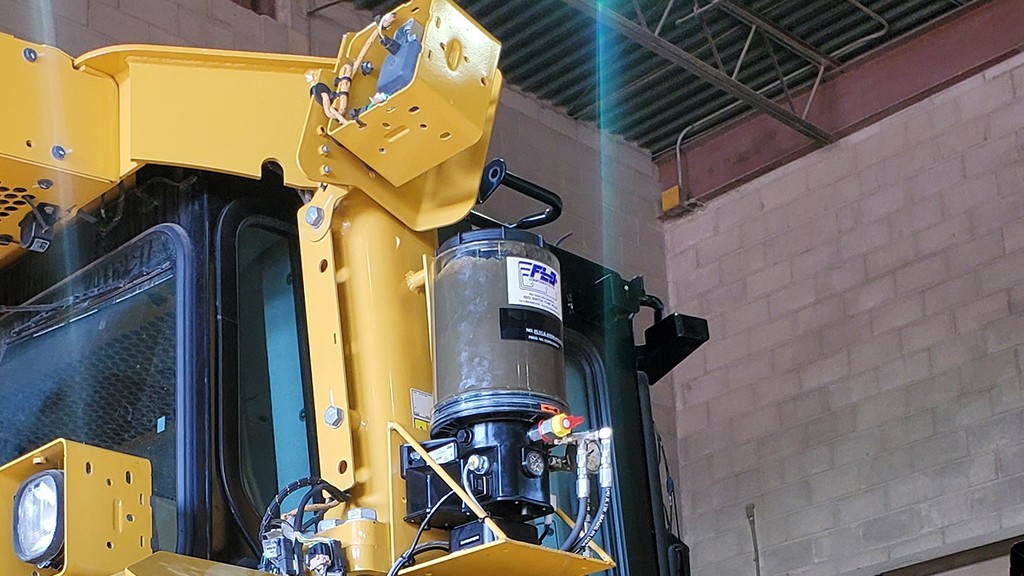
Automatic lubrication systems (ALS) have helped take a tedious daily task out of the routine for operators and mechanics working with heavy equipment. The ability to have an automated system provide grease to the necessary locations on machinery helps save time and keeps maintenance up to date more effectively.
At the same time, the desire to collect more data about equipment maintenance and operation has driven growth in telematics use. More demand for detail that can aid in planning preventive maintenance programs is driving the development of remote monitoring opportunities - including one tied to auto lube systems.
FLO Components, a manufacturer of automated lubrication systems, has introduced FLOlink, an independent remote monitoring telematics program designed specifically to give customers a snapshot of their ALS across their fleet. FLO Vice-President Mike Deckert said that the company started developing telematics for its systems after seeing equipment manufacturers adding more and more new technology to their machines.
"We started including the lube system alerts for low level and lube failure in the machine telematics, but when you started looking at the reports that come up, there are pages and pages of information," Deckert said. "Talking with our customers, we heard ‘You know what? I just want to know what's happening with my lube system.'"
That launched a drive to develop a product that would monitor the lubrication system for when it's low on material, as well as any failures and several other conditions, he noted.
Regular service important for auto lube systems
Auto lube systems feature a reservoir plumbed to a machine's grease points, paired with a timer and controller, which distribute grease on a regular schedule. The system is a huge shift from days when a mechanic or machine operator might crawl over and under a piece of equipment with a grease gun, manually delivering grease to those key points.
However, automated systems can't work on their own - they still need to be serviced and refilled to ensure they are able to keep up with the needed lubrication work. That's where FLOlink comes in.
"There are two things that we're looking for. One is the reservoir level - what we call low level - and the other is lube failure: if the lube system is working or not," Deckert described. "If it's not working, if there's a failure, a blocked line or something, then we want to know about it."
FLOlink works with any model of FLO's automatic lubrication systems. A modem is connected to the system that connects to sensors and tracks the current status of the system. When certain situations - like a low level indication or need for service - are detected, the system can send alerts to key personnel via email. For example, if a system reports it is low on lubricant, an email is sent and a fleet manager can then send their service personnel to top up the reservoir immediately - before there's a potential for damage to the machine.
Fleet managers and owners also get an additional benefit: FLOlink allows easy visibility of lubrication system health across not just single machines, but across the fleet, Deckert noted. That way they can determine whether each particular incident requires a lube truck or a mechanic and allows them to better track their lubrication needs across the fleet.
Tracking provides useful maintenance scheduling tool
Lubrication and maintenance is an important part of equipment maintenance, but it can sometimes slip through the cracks - FLOlink provides a beneficial tool that helps to improve the maintenance schedule and processes for fleets of all sizes, no matter what their maintenance program might be. That's a key message Deckert says FLO is always offering to equipment owners.
"Some of our fleets have an amazing maintenance program, and typically those are the ones that are always looking to upgrade or to collect this data," he noted. "It's the other ones where they say ‘Well, when my machine starts to squeak, that's when I know I have a problem' - those ones, it's constant training to let them know they're spending a lot of money when they don't really need to."
FLOlink aids in maintenance training and planning by providing contractors with a tool that puts lubrication of equipment at top of mind for both managers and operators, Deckert said.