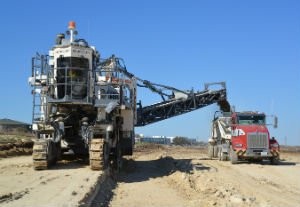
Surface mining offers a far more economically efficient and environmentally friendly solution to quarrying and removal of ore, as it’s capable of cutting, crushing and loading rock in one single working pass. That’s why Wirtgen’s line of precedent-setting surface miners are proving that drilling and blasting in mining, earthwork and rock operations are no longer “state of the art.”
Wirtgen America markets the world's most advanced line of surface miners. The 4200 SM selectively mines coal and iron ore, as well as soft to medium-hard rock. The 2500 SM offers flexibility and performance when mining without blasting, and the 2200 SM is versatile in soft and medium-hard rock. The new 2500 SM Vario is designed for hard mining.
At Conexpo-Con/Agg 2014, a detailed model of the enormous 4200 SM was shown.
This innovative technology cuts expenses for machines and personnel and saves a considerable amount of time when compared to conventional methods. At the same time, it produces even, stable surfaces and embankments, and permits the selective mining of individual rock layers, cutting of haul roads and refinement of drainage.
And that’s not all: Surface mining is a low-dust, low-noise method that causes no damaging vibrations and therefore permits effective mining of useful minerals close to residential areas or roads.
Surface mining also provides an alternative for road right-of-way construction in urban areas or on environmentally sensitive projects where blasting is not allowed.
From the surface miner, the mined and crushed material is so small that it can be processed profitably, requiring minimum subsequent treatment. Mining bauxite, phosphate, kimberlite or salt has become increasingly profitable with the surface miner, which can even mine hard limestone or granite with unconfined compressive strengths of up to 260 MPa without blasting.
The operating method of surface miners resembles that of asphalt cold milling machines. A special cutting drum cuts and crushes the material. Robust conveyor systems then load the material on dumpers or discharge it to the side of the miner. Alternatively, the material can also be deposited as a windrow between the miner’s crawler tracks.
A highly precise automatic levelling system maintains the cutting depth. This highly accurate method enables useful minerals, coal or limestone to be mined selectively and with high purity.
The mechanically driven cutting drum works against the direction of travel. Extremely strong cutting tools on the drum mine the material by removing and crushing it. The tools are arranged on the drum in the shape of a helix. Ejectors on the cutting drum assist in transferring the small-sized material to the conveyor system.
The primary conveyor picks up the material in the drum housing and transports it towards the rear of the machine, where it is then accepted by the slewing and height-adjustable discharge conveyor. The discharge conveyor either loads the material onto trucks or dumpers, or discharges it to the side of the machine. The discharge height can be adapted to the height of the transport vehicles.
Mining the material in precisely the required thickness is crucial for the selective mining of rock layers. That is the job of the machine’s automatic levelling system: It maintains the specified cutting depth.
Two control loops – one for each machine side – continually match the actual cutting depth with the pre-selected target values. This is achieved by optical or mechanical sensors scanning a reference surface. Changes in the reference plane level are compensated by means of proportional control. The automatic system responds quickly and without overshooting.
Slope sensors additionally can be used for leveling when the cut surface needs to have a particular cross slope.
Company info
6030 Dana Way
Antioch, TN
US, 37013
Website:
wirtgen-group.com/en-us
Phone number:
615-501-0600