Boliden, Epiroc, and ABB install underground mining battery-electric trolley truck system
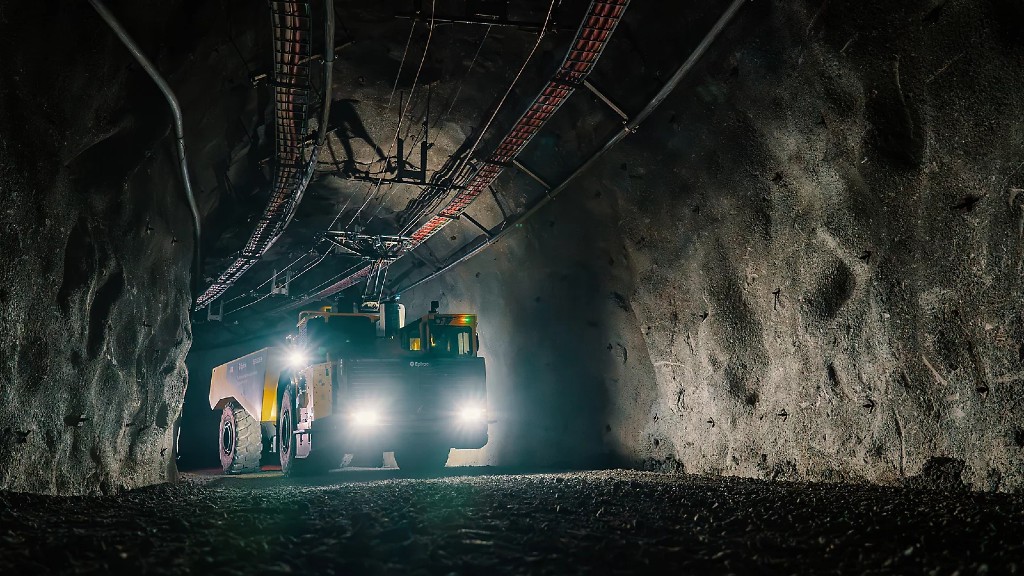
Boliden, Epiroc, and ABB have successfully deployed a fully battery-electric trolley truck system on an 800-metre-long underground mine test track with a 13 percent incline in Sweden.
"Over the past three years, we have worked in close collaboration with the ABB and Epiroc teams to bring the electric mine of the future one step closer," said Peter Bergman, general manager of Boliden Area at Boliden. "The most important thing for us is of course that the technology works in our own operations, but we also see added value that we together with our partners can drive technology development so that the system can be used in other mines. We are proud to have taken this concept to a live installment."
The collaboration in Boliden's Kristineberg mine in northern Sweden marks a critical moment for the mining industry as it continues to face rising pressures to balance increased outputs of critical minerals and metals with lower carbon emissions and energy usage. Demand for minerals critical to society's clean-energy transformation is predicted to increase between 1.5 to seven times by 2030, according to the IEA, making electrification a priority.
Boliden intends to implement a full-scale, autonomous electric-trolley system in the Rävliden mine, a satellite orebody and extension of the Kristineberg mine, and has placed an order for four Minetruck MT42 SG trolley trucks from Epiroc. The total distance will be 5 kilometres at a depth of 750 metres. Once achieved, Rävliden will have significantly less carbon emissions compared to a mine using conventional technology.
In tandem with reducing carbon emissions, the electrification of mining also promises improved health and safety for the industry's workforce. By deploying this system, the collaboration partners aim to prove that the underground working environment can be significantly improved, with fewer emissions, noise, and vibration throughout while reducing the total cost per ton.
Each partner has provided experience in this development process. Epiroc has added dynamic charging to its battery-electric Minetruck MT42 SG and battery system, and the trolley system is equipped with ABB's DC converter, HES880 inverter, and AMXE motors to enhance the power. The mine truck features a trolley pantograph connected to an overhead catenary line, a concept suitable for long-haul ramps.
The electric trolley line gives additional assistance to the battery-electric mine truck on demanding stretches up-ramp while fully loaded, enabling further reach and battery regeneration during drift. ABB created the infrastructure from the grid to the wheel, including the electric trolley system design and the rectifier substation for the test track.
"Together, in close partnerships, we can accelerate the transformation and reach a steep curve in mining technology innovation as we have done in Kristineberg," said Wayne Symes, president of Epiroc's Underground division. "In a short space of time, we have implemented and delivered technology to not only reduce CO2 emissions, but substantially extend travel distance for battery-electric driven vehicles on heavy ramp haulage, reduce operating costs, and improve the health and safety of mining environments."
Company info
1025 Tristar Drive
Mississauga, ON
CA, L5T 1W5
Website:
epiroc.com/en
Phone number:
289 562 0100
8585 route Transcanadienne
Saint-Laurent
Montréal, QC
CA, H4S 1Z6
Website:
abb.ca/instrumentation