The benefits of preventive fleet maintenance and equipment inspection
United Rentals offers insight on how effective inspection and maintenance plans improve the bottom line
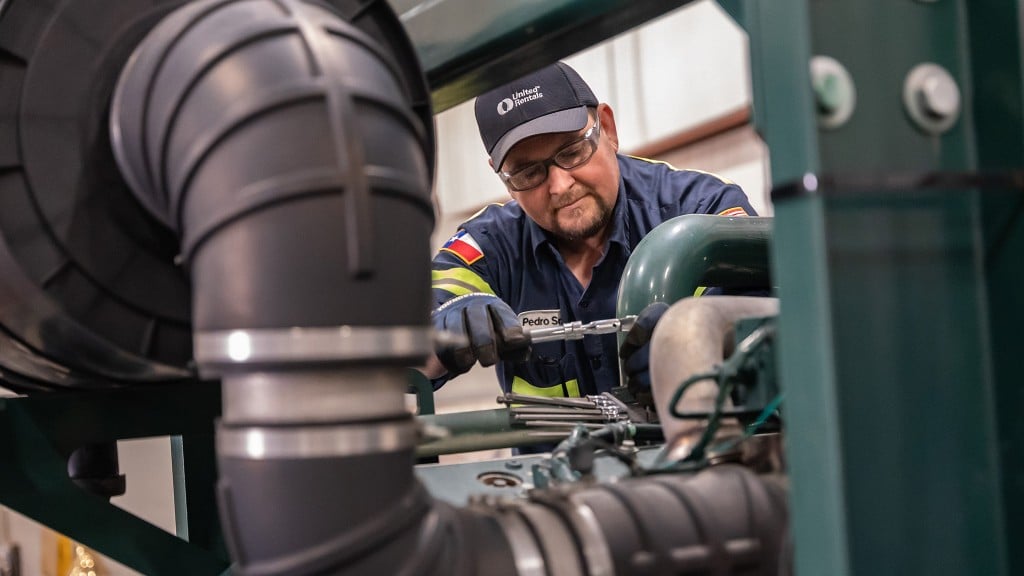
Preventive maintenance and inspection programs can help construction and industrial companies garner maximum value from their equipment fleets. According to United Rentals, regular maintenance and inspections are a critical component of equipment operational efficiency.
Under-maintaining equipment, especially high-use compact to midsize machinery, can happen for a variety of reasons. However, failing to conduct maintenance and required inspections comes at a price that includes higher equipment costs, lost productivity, and increased safety risks.
"For too many companies, preventive maintenance tasks and inspections fall through the cracks of busy work schedules and equipment moving from work site to work site," said Bret Kasubke, director of Customer Equipment Solutions, United Rentals. "A well-executed maintenance and inspection program delivers great value by ensuring equipment is ready to go. It adds structure and visibility to the maintenance of owned equipment so companies can reduce downtime and improve cost control. The program protects equipment investment and can extend machinery life, possibly reducing the risk of catastrophic equipment failure that can lead to work site safety issues."
A look at safety, productivity, and financial benefits
Here are some key safety, productivity, and financial benefits that preventive maintenance programs and regular inspections provide to construction and industrial companies.
Safety benefits. Over time, wear and tear on equipment can lead to potentially dangerous mechanical failures. Worn chains and cables, broken pedals or levers, and malfunctioning safety lights or audio signals can cause work site accidents. Creating and following an equipment maintenance plan can mitigate serious hazards that result from faulty equipment and improve overall work site safety.
Equipment inspections required by ANSI, OSHA, and CSA are equally important. For example, aerial lifts, such as boom and scissor lifts, require inspection by qualified mechanics or technicians every three months or every 150 hours, whichever comes first. Aerial lifts must also be inspected annually - every 13 months - and every time the equipment has been out of service for more than three months.
It is important to note that only a mechanic or technician qualified to work on the specific make and model of the aerial lift can perform the lift inspection. If a company does not have this expertise in-house, it should consider outsourcing equipment inspections to a qualified vendor.
Productivity benefits. Poorly maintained equipment is more likely to break down when it is needed. Companies that follow a preventive maintenance schedule experience less unplanned equipment downtime and better equipment performance, resulting in greater productivity. Inspecting equipment during regular preventative maintenance service can reduce the risk of potentially crippling issues.
Financial benefits. Proper maintenance and inspection of equipment can save a company money in numerous ways, including:
- Reducing downtime: When a single piece of equipment fails, the costs of lost productivity and wasted wages can be considerable. Preventive maintenance and regular inspections help reduce equipment failures.
- Avoiding fines: Failures to perform aerial work platform inspections or inspect other equipment on schedule, such as cranes and derricks, can result in government fines.
- Lowering repair costs: A well-executed preventive maintenance program can lower repair costs more than relying on reactive maintenance - waiting until a machine breaks to fix it. The simplest maintenance tasks can prevent expensive engine breakdowns.
- Reducing overtime: If equipment breaks during a project with a tight schedule, a company may have to pay workers overtime to make the scheduled deadline.
- Extending the useful life of equipment: Well-maintained equipment lasts longer. When regular fleet maintenance is performed, companies can delay the need to purchase new equipment.
Outsourcing can be an attractive option for companies that want to gain the benefits of preventive maintenance and inspections but need more internal capabilities or resources. A third-party provider that offers a dependable one-stop shop with standardized processes and rates takes the maintenance and repair burden off fleet owners. This approach can give companies the peace of mind that comes with knowing equipment will be ready to perform when needed.
"Starting and sticking to a preventive maintenance program isn't simple or easy, especially when equipment moves from job site to job site. Outsourcing these tasks to a single vendor with deep experience in equipment maintenance and a large staff of skilled technicians can relieve the burden of fleet maintenance and let companies focus on what they do best," said Kasubke.
Repair and service in the field and on-site
The United Rentals Customer Equipment Solutions team specializes in equipment repair and service in the field and on-site, so companies can protect their investment, safeguard employees, and meet ANSI, OSHA, and CSA requirements. From on-demand service for unexpected repairs to turnkey fleet management, United Rentals Customer Equipment Solutions has offerings that can be tailored to an organization's unique needs. In addition, United Rentals offers parts and supplies for sale so companies can conduct their own maintenance and repairs.