Preventive maintenance versus predictive maintenance – why they matter
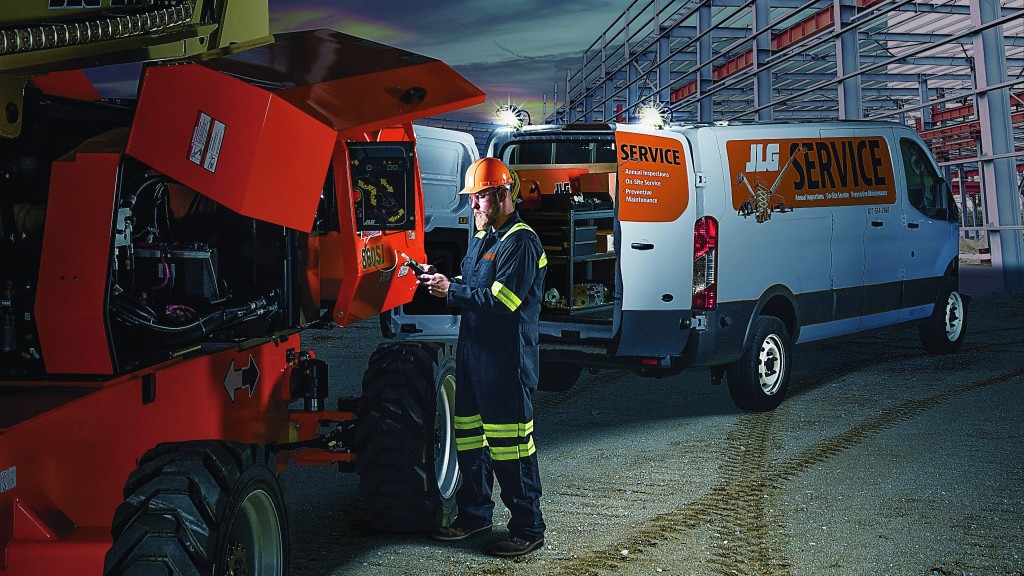
Equipment downtime will not only set you behind schedule, but it can result in lost revenue. Equipment needs to be in top working order and on the job site to make the most of your investment. A vital part of achieving that goal is incorporating a regular maintenance routine into your business practices.
Completing maintenance on the equipment not only will help prevent unexpected downtime, but it also makes the equipment more efficient, leading to improved output and production quality. Well-maintained equipment will have a longer lifespan overall, as will its different components.
What is preventive maintenance?
To ensure your fleet is up and running efficiently, you will need to take care of the machines. One way to do that is with preventive maintenance. This proactive approach to equipment maintenance falls between reactive and predictive maintenance and can help prevent unexpected breakdowns.
Simply, preventive maintenance is regular, routine maintenance based on proven best practices and identified intervals that give you the best chance of catching an issue before it starts. The main focus of this type of maintenance is to prevent equipment issues and downtime.
Preventive maintenance can occur at different intervals set within your business, like a daily list of items to check and then a more intensive list semi-annually and annually. These checklists, which are included in your machine's Operation & Safety Manuals, should include an inspection, repair/replacement, calibration, and cleaning of the equipment and its different components – and when each should be completed (daily, weekly, monthly, etc.).
The machine will be down during these checks, so performing the maintenance before and/or after the workday is ideal for equipment currently in use on jobs. Preventive maintenance should be performed whether or not there are identifiable issues.
What is predictive maintenance?
As technology continues to evolve, so should your maintenance practices. Equipment can now alert you when there's a potential issue before any downtime occurs. Having the ability to flag issues before ever looking at the machine can be a game changer – and you can do that with predictive maintenance.
As the name suggests, this type of advanced maintenance predicts equipment issues while the machine is on the job site and sends notifications for your team to address as needed, allowing you to prevent costly downtime.
Predictive maintenance uses real-time data from equipment with condition-monitoring technologies to indicate potential issues before they occur. This proactive, data-driven approach assesses the machine's performance while it's operating, which reduces the downtime needed for unplanned replacements or repairs.
This type of maintenance requires machines and technologies with interconnected measurements and data collection systems – along with team members who can analyze the data received from the machine. It's important to establish baselines for the equipment before you start using predictive maintenance so you can identify issues when the machine operates outside of those parameters.
Predictive versus preventive maintenance
The best maintenance plans include a mixture of both predictive and preventive practices. While both maintenance strategies focus on being proactive to reduce unexpected downtime and equipment failure, there are some distinct differences between the two. Unlike preventive maintenance, predictive maintenance:
- Can be performed while the machine is in operation
- Occurs as-needed based on data, instead of following a schedule
- Has targeted downtime if an issue is detected
- Focuses on real-time equipment data – not solely on an inspection
Instead of an operator or technician signaling that there's a red flag with the equipment, the data being sent will show when there's a potential issue. The goal of predictive maintenance is to remotely identify issues before they turn into larger ones.
Keep equipment on the job site
Both preventive and predictive maintenance position you for success because it gives you the best chance of catching issues before they start and potentially lead to bigger problems.
Retaining comprehensive records of when and what tasks have been completed on each piece of equipment puts all of the information in one place for you and your team to track and review. Over time, you can use that information to see if you need to adjust your preventive maintenance checklist or schedule.
To ensure your machines are receiving the proper preventive maintenance, check with your dealer and follow manufacturer recommendations.
Jennifer Stiansen is the director of marketing at JLG.