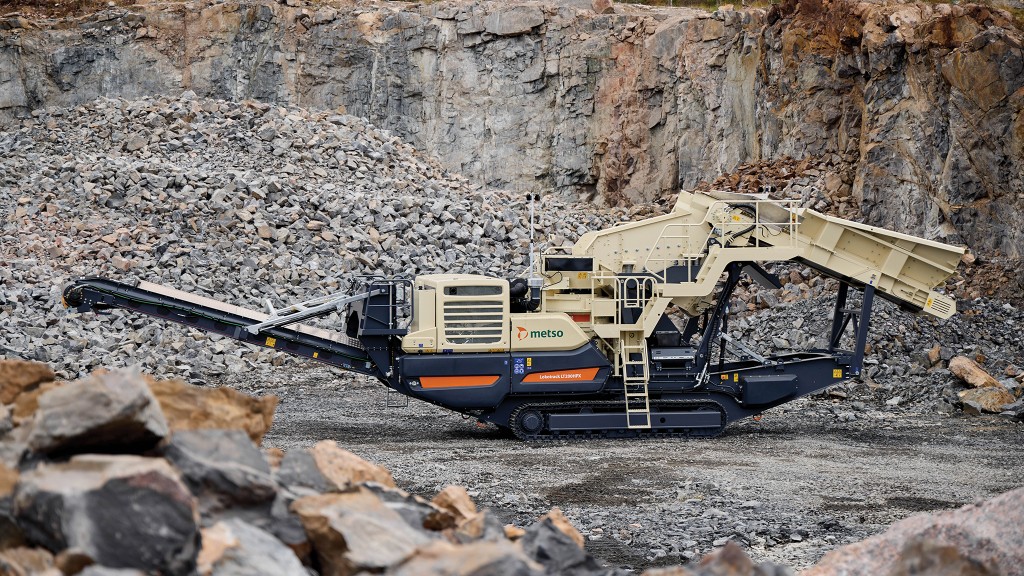
Compact mobile crushers easier to use and move
Metso Outotec has introduced a pair of new models to its Lokotrack crushing and screening range. The two mobile cone crushers are compact and efficient, with up to 30 percent more capacity as well as more flexibility compared to earlier models. Both cones are easily combined with Lokotrack jaw crushers and mobile screens to produce an efficient package in the quarry. The LT200HPX has a two-deck pre-screen for higher capacity, along with a heavy-duty chassis and wide conveyors for high throughput and a direct v-belt crusher drive for high fuel efficiency.
For more crushing power, the LT220GP can be selected and equipped with a pre-screen or belt feeder. It can also be combined with Lokotrack jaw crushers and mobile screens for a more efficient and highly productive spread.
Kleemann has designed a pair of machines to work together in a crushing spread, matching efficiencies and ensuring optimized, quality throughput. The Mobicat MC 110(i) EVO2 jaw crusher and Mobicone MCO 90(i) EVO2 cone crusher are frequently used together as the first and second stages in a crushing line, and it was natural to pair them ideally for this purpose. Output from the jaw crusher is ideal for perfect utilization of the cone crusher in the second stage; both machines are adjustable to ensure ideal throughput.
On the screening end, Powerscreen's Titan range of secondary scalping screens offer cost-effective solutions in a range of applications, including recycling. The compact Titan 1300 is designed to fit on small trailers for easy transport, and combines an extra-large-capacity twin-drive feeder at the rear of the machine with an 1100mm feeder belt with hydraulically folding extensions to allow for side loading. An aggressive screenbox offers a variable angle for various applications, and has lift-up functionality for quick and efficient screen media changes. The largest belt feeder in the Powerscreen line, at 1,500mm (60 inches), is designed for optimum power usage and is available with Hybrid Dual Power using standard diesel or connection to an external electric supply. A steep hopper enables ease of emptying without bridging, a benefit for recycling operators.
Less water and more efficiency for Terex wash plants
A sand quarry set up near Sydney, Australia, is making use of a Terex Washing Systems plant to produce high-quality sand while recycling most of the water used in the washing process. The custom designed plant can produce up to 300 tonnes of sand per hour. It starts with a H30 (50-tonne) feeder, where stone and rock larger than 100 mm are separated out and sand is evenly distributed on the main conveyor. A deck rinser screen designed specifically to handle the tonnage needed rinses material as the vibrating screener shakes it down during size classification.
Sand, silt, and clay are washed to the screener's split catchbox, then the material is fed into FM 200C sand plants, one for coarse sand and one for fine. For this operation, these were upgraded to separators rather than hydrocyclones to help with higher volumes of fines. Material then moves to dewatering screens, after which only 10 to 15 percent of water is left. Sand meeting spec goes to a radial stacking conveyor. Meanwhile, the water is captured and pumped into a rake thickener tank. A flocculant dossing unit helps bind waste particles together for quicker settling. The result is a system that reuses about 90 percent of water.
Terex Washing Systems is also improving efficiency in other ways, including offering hybrid options for its enhanced M1700 mobile washing screen. The M Range of mobile washing screens can produce up to five products - three aggregates and two sands - for aggregates, recycling, industrial sand, and mining applications.
Wash plant cuts water use in recycling application
Sodextra S.A. is targeting recovery of up to 70 percent of incoming inert CD&E waste in its newest wet processing plant, a custom design developed by CDE. At the same time, it's reducing the amount of water being used in the washing process, an added benefit to the company's goals. Sodextra recovers about a million tonnes of material yearly from construction and demolition waste and hopes to improve that thanks to the new CDE wash plant aiding in recovery of inert soil.
Based on the analysis of the soil from around the region, CDE was called on to answer the challenge presented by the processing of the very heterogeneous and heavily clay-bound material.
CDE process engineers tested the reclamation potential of Sodextra's incoming waste stream, and a unique design was developed to improve recovery. The plant uses a variety of CDE modular technologies along with integrated patented technologies for things like density separation that can maximize the quality and value of feedstock. It also incorporates CDE's AquaCycle, which provides an alternative to extraction and pumping of water by improving efficiency. Up to 90 percent of process water is recycled in the process, with just small amounts of top-up water needed.
The Sodextra solution also includes a filter press, which recycles even more water - up to about 96 percent. At the same time, Sodextra is extracting new products to increase its recovery from waste to 70 percent.
Big crusher calls for big generator power
Big crushing jobs require big power, and for Swedish operator ABBEMA and its largest machine that need called for a big engine to generate plenty of electricity.
ABBEMA recently purchased a massive Metso Lokotrack LT330D mobile cone crusher, one of eight that the construction and crushing company own, and the largest by far, combining a three-deck screener with the secondary crusher. The design is unique, in that the unit can receive stone directly from a primary crusher and reprocess into smaller sizes as needed, producing three different fractions of material simultaneously. At the heart is the Nordberg GP330 cone crusher; electrically driven, the ideal for ABBEMA is to power the crusher from a mains connection, but when the machines move anywhere up to 500 km from their base that's not always possible.
So, owner Benth Winqvist selected a Volvo Penta D16 as the crusher's integrated generator power package. The compact, low-weight 16.1-litre diesel genset features dual-stage turbochargers and heavy-duty steel pistons to ensure excellent power density, providing primary power equivalent to 596 kWm (mechanical kilowatts).
With the D16 operating it, the LT330D can crush up to 220 tons of small aggregates for concrete and roadbuilding each hour, or 350 tons of large fractions. In addition, low noise makes life easier for operators.
Company info
800 Farewell St.
Oshawa, ON
CA, L1H 6N5
Website:
powerscreencanada.com
Phone number:
877-797-7276
6030 Dana Way
Antioch, TN
US, 37013
Website:
wirtgen-group.com/america/en-us/products/kleemann
Phone number:
(615) 501-0600
200 Coalislad Road
Dungannon,
IE, BT71 4DR
Website:
terex.com/washing-systems/en/index.htm