In-motion weighing helps scrap handlers improve loading at Calgary Metal Recycling
Swedish-built wireless grapple scale provides better way to load rail cars
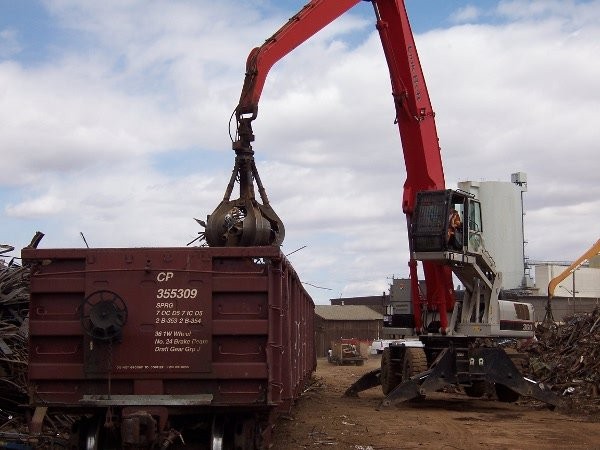
Calgary Metal Recycling Inc. has more than 85 years experience in processing scrap metals. Still, an efficient way to fill open-top gondolas (rail cars) accurately had been a persistent challenge. In 2012, the company went looking for a better way to get the job done.
“Without having a rail scale, it’s been kind of tough,” says Steve Goodzeck, Calgary Metal Recycling. “We have a bucket-scale loader, but most of the material is not easy to handle with a loader. Before, when we were loading the HMS (heavy melting scrap) the loader couldn’t just go into a pile. One machine would load the bucket, the loader would pull the weight and dump it into a train car, then another machine would have to level the train car and spread the material around.”
“Now, we’ve eliminated two-thirds of that job,” he says.
The improved loading at Calgary Metal Recycling came in the form of a new wireless grapple scale manufactured in Sweden by Intermercato and marketed in North America by RMT Equipment.
The Intermercato XW scale utilizes a strain gauge system that allows in-motion weighing, without requiring the machine to pause in its loading cycle to record the load’s weight.
“It has sped up our shipping, there’s no doubt about it,” Goodzeck says. “We’re shipping out cars faster and the weights are coming back accurately. It’s wonderful. We know what we’re shipping and we’re maximizing the rail car’s capacity. That means we are also maximizing the profitability of the load. It’s probably letting us fill two-and-a-half times the number of cars in a day, and we’re getting the right weights in them.”
Like most recycling businesses that ship by rail, Calgary Metal Recycling often faced penalties and added costs caused by inaccurate loading.
“We don’t want to be under-loaded, because then we’re paying more per ton,” explains Goodzeck. “But if we are overloaded, they pull the car into a siding down the line and you have to send an operator and a machine to go and take material off. And you’re paying demurrage charges on that car while it’s waiting.”
“With this grapple scale, we haven’t had a problem with overloaded cars. We’re shipping the weights we want to get into the car. It depends on the material, of course: some material has less density, but some can easily go over, especially shred and heavy HMS. And when you do, it’s costly.”
In 2012, after searching the internet for a grapple scale that could really do the job, Goodzeck learned about the Intermercato scale from a local specialist in productivity equipment, Mountainview Systems.
“The fellows from Mountainview were quite accommodating in helping us get it set up,” Goodzeck reports. “We calibrated the scale once; then they were out again when we were a little bit off in the very beginning. Since then, there’s been no problem. We double-check periodically with check blocks we use on our truck scale.”
Goodzeck says he’s especially pleased that, while the grapple scale is much less costly than the rail scale, it is also very robust.
“I like the fact that it’s all enclosed in a nice tight case. We’ve done things that we wouldn’t recommend doing with any kind of sensitive equipment but it’s stood up.”
The XW scale is installed by simply replacing the yoke of the grapple with the scale itself, which then serves as the coupler. At Calgary Metals, the scale is fitted to a Liebherr Type-75 grapple, operated by a 99,000-pound Link-Belt X2 with a 55-foot Young boom and stick. The company says operators are able to lift, load and spread all sorts of material normally. When they’re not loading rail cars, they can turn to other tasks in the yard such as sweeping with a magnet or off-loading for customers.
“We have three operators using the grapple scale. It required minimal training and we have had good success,” says Goodzeck. “They’re just using the machine as a regular grapple in the yard. There are no signs of any complaints from the scale and we beat on it pretty hard. We also don’t have any wire to contend with or any transmitter problems or anything like that.”
Recently, the scale’s easy installation proved to be an extra benefit when a problem with the X2 handler took it out of service for repairs. The Calgary Metal Recycling crew simply moved the scale and grapple to another Liebherr material handler in the yard.
“It was just six bolts on top and six bolts on the bottom to bolt into the Liebherr grapple, then two wires to connect in the cab. We were able to swap it out in a couple of hours and continue to load rail cars,” says Goodzeck.
“Our goal here is to move as much material as possible, as fast as possible,” he continues. “The fewer times you have to handle it, the better. This grapple scale from RMT has worked wonders for us in solving that problem. We’re doing it faster with less equipment, and we have had no overload problems since we started using it a year ago. One machine can go into the prepared pile, pick it up, weigh it, lay it into the train car, and spread it around. I would say that this piece of equipment has more than paid for itself in the time we’ve had it.”