Kal Tire transforms tire inspection with TOMS
The new Tire Operations Management System harnesses data for powerful insights
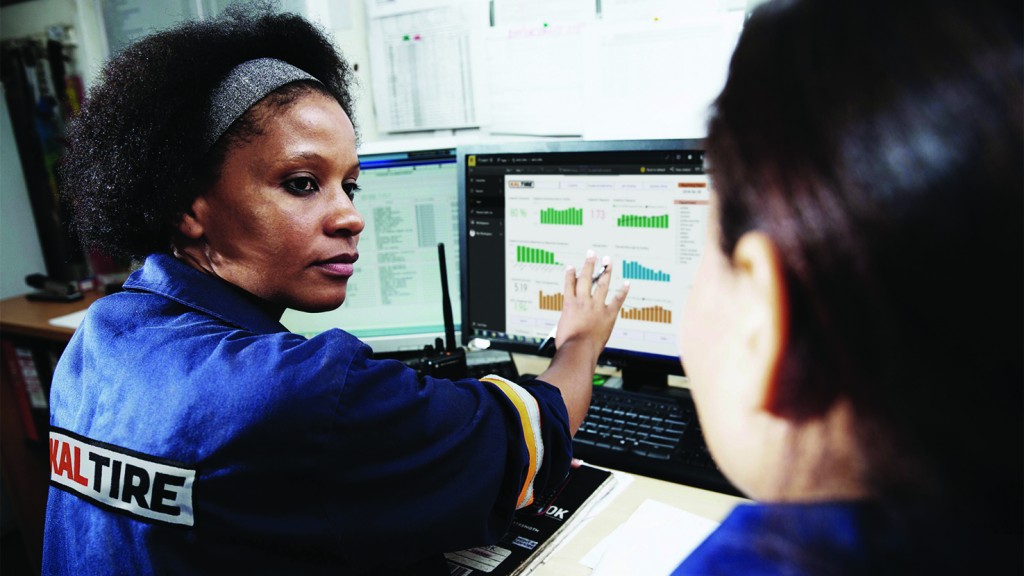
A mining truck is only as good as the tires it rides on, and inspecting and maintaining those tires is a big job with significant implications for both productivity and safety. With its new Tire Operations Management System (TOMS), Kal Tire is demonstrating that tire management can benefit from more effective fleet inspections and improved planning and communication of required tire work. With TOMS, the company is making the tire inspection and reporting process clearer and more efficient today, while common language data capture and centralized data management will lead to predictive tire maintenance, AI recognition of damage and more effective training for inspectors in the future.
Historically a significant challenge for tire inspections has been the lack of a consistent, clear method for capturing and communicating damage issues. Mark Goode, Director of Business Insights for Kal Tire, said that the software and paper-based data collection methods traditionally used have been effective at gathering information for use in historical tire performance reporting, but haven't been as efficient at capturing or communicating tire work that needs to be planned. "Tire work that needed to happen immediately was handled pretty effectively by the tire technician simply calling Dispatch on the radio," Goode said. "But tire work that needed to be planned and that could take place at the same time as the equipment was down for other work was often missed as it wasn't captured effectively, nor communicated. This led to a lot of tire work being unplanned and incurring unnecessary downtime."
How TOMS is changing tire inspection
"The concept came from the fundamental recognition that Kal Tire, as a tire service provider, works primarily for the maintenance team on site and, as such, that we needed to use a similar maintenance planning tool as our customers," said Goode. "In short, we needed to think and be able to talk the same maintenance language."
TOMS is a work-order-based solution built on an enterprise asset management system (EAM). A core concept of the system is to plan work and report on the successful completion of inspection tasks and generated tire work. A powerful feature of TOMS is that all information flows into one database.
While the basic process of doing an inspection as defined by Kal Tire's Safe Work Procedure doesn't significantly change, using TOMS, inspections are planned for each piece of equipment at agreed upon intervals. The inspector uses a pre-determined task list based on variables that are agreed upon with the customer up front in a Maintenance Activities Plan (MAP). The MAP is regularly reviewed and evaluated to ensure that it continues to accurately reflect the operation's needs.
"We use the core functionality of the system to produce a planning report for our customers that can be automated or run for a determined forward-looking period. This planning report includes all the tire or wheel work required for the period ranked by priority and organized by truck. This work typically covers upcoming rotations, rim NDTs and all identified work found as part of the fleet inspections," said Goode.
Another vital feature of TOMS is its use of one common language. This means that inspection findings, actions and priorities, for example, all have unique codes removing any ambiguity from written notes. Consistency has long been a problem in gathering data from written inspection reports.
With its central database, Kal Tire acts as a gatekeeper to ensure consistency in coding and data capture remains intact.
"Consistency of data capture is important for reporting purposes and also data analysis, but inspectors can always add their own notes [to the report]. If I'm inspecting a truck today, and you had done it last week, I can see your codes, your findings and recommended actions and also any notes you might have left me as well as any photographs you might have taken."
The first phase of TOMS was paper-based, the inspector using a common booklet of codes that includes all inspection, removal and scrap descriptions. Kal Tire is now rolling out a mobile version that captures data via a smartphone or tablet, which allows for real time or close to real time data capture as well as clear communication of updates to the inspectors. "One key change for us with the move to mobile is the ability to capture images and bring them into the system," said Goode.
"What that means, from a process point of view, is when the inspectors are doing the inspection, and they're capturing their findings, their actions and their priority codes and photos of any damage, that information is reviewed by the manager of the site before it goes into the system. We are giving the manager far more information than he had before; he can now physically see the damage."
The manager's ability to see this damage leads to more value added conversations with inspectors and the customer about when tire work needs to be planned.
Harnessing data for customer productivity
Goode said that customers want concrete recommendations of things that they can do differently to improve tire performance and productivity.
"We can trend and benchmark operational damage findings over time, along with track how long it takes for work to be completed. We plan to analyze the inspection data collected in conjunction with removal and scrap tire data in order to improve our ability to determine and predict when tire work needs to happen," he said.
"Given that a fundamental goal of tire management is to help ensure that our customer's mining fleet is as productive as possible, it's critical more focus is put on understanding how often and for how long trucks are actually out of service due to tires. Our customers typically know this for their own operations of course. We see tremendous opportunity to help our customers reduce that downtime through better analytics and benchmarking across operations. Improved tire performance is a key driver for sure, but improved planning and management of tire work can be just as important. And in many ways, these depend ultimately on the quality of the tire inspections taken and the communication process from them. That, with TOMS, is what we are looking to address."
Kal Tire is already working on research projects to provide feedback for customers. For example, the company has just started a project with researchers in Canada to determine the impact that rotations have on overall tire life and when it's the right time to rotate. Goode hopes that this research will determine whether there is a direct correlation between when a site rotates tires and the impact on tire life.
The future of TOMS
It's still early days for TOMS, which is currently in use at approximately 60 mining sites in 12 countries. "We're only now starting to analyze the data and see what we can learn from it," said Goode.
For example, as Kal Tire collects more photos of tire damage through the TOMS system, it will be able to train AI to recognize damage using the common codes in the database. Goode expects that in a few years the AI will be able to recognize tire damage accurately and be able to support inspectors in their jobs. Goode also anticipates that this ability will be a good training tool for new team members and that it will help drive more consistency and in turn provide better information for continued analysis.
"Three years ago we were using at least half a dozen different tire management software systems across our operations. Each of those systems had independent databases and each of those databases had different ways that tires were called. To get access to those databases and to map them together and try to say ‘Can we benchmark tire performance here?' We just couldn't do that three years ago."
Pushing all of the data to one database is a game-changer.
"Over time the system will increasingly change from one that is a collection tool, which probably is 70 percent [of TOMS] today, to one that actually is driving recommendations and standard procedures," Goode said.
Putting that intelligence to use is something that Goode said Kal Tire is hoping to see over the next five years. "That's the ultimate value. We can make every single one of our people as intelligent as all of us together."