Procore project tools give builders a boost
Toronto tower project benefits from robust project management software options
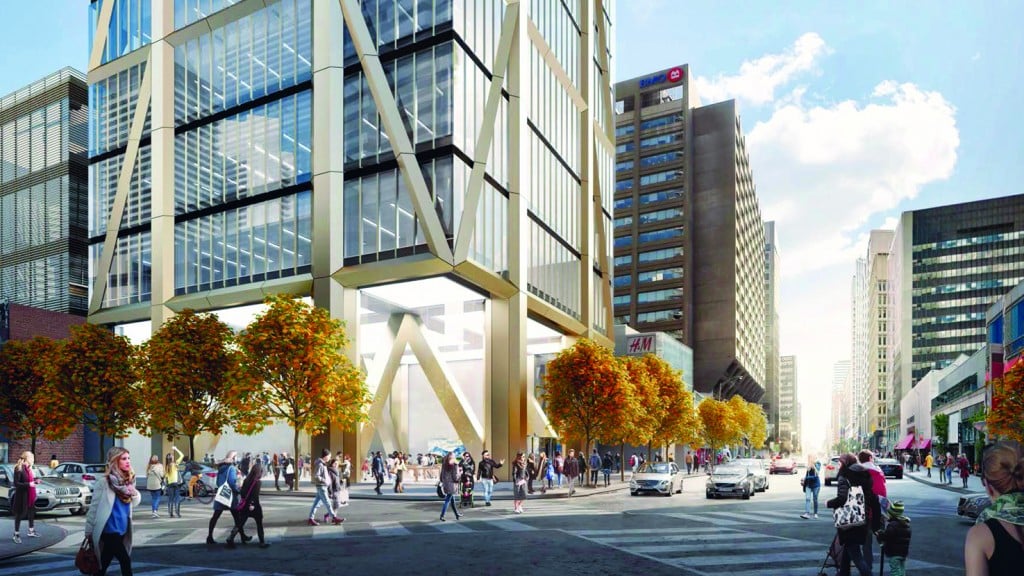
Towering high above Toronto's tallest buildings at 306.3 metres, a new skyscraper will soon join the skyline. Located at the intersection of Yonge and Bloor Street, The One is set to be the tallest building in Canada. With a distinctive design featuring dramatic diagonal steel pieces framed by mega-columns on each side, the unique design is as visually stunning as it is complex. Both the developer and construction manager agreed they needed project management software that was comprehensive enough to manage one of the largest projects the city – and country – has ever seen.
As partners on the project, Clark Construction Management and Mizrahi Developments knew even before the project began that they wanted a top tier project management solution. In the few months before using Procore, teams were using Excel and saving documents on their server. However, this not only led to confusion, but did not allow for full collaboration.
"It was difficult because there wasn't open communication between everyone involved. All the as-builts were in a separate system, and they couldn't easily be communicated to the office guys, and we'd have to dig around for photos," Connor Early, Clark's project coordinator, explained.
Clark and Mizrahi began construction near the end of 2017, and with a completion date set for 2023, they agreed they needed a system that was robust, reliable, and would allow both teams (and any third-party subcontractors) to seamlessly collaborate over the entire duration. They had successfully used Procore on a previous joint project, so shortly after starting construction they decided to partner with Procore on The One as well. They implemented multiple products including Project Management, Quality & Safety, and Construction Financials.
"Clark and Mizrahi discussed what the best project management software would be. Both decided to go with Procore because it had the most comprehensive usage from financials to quality and safety to project management. It was a whole package deal – everything was interconnected and everything made sense. You could connect your RFIs directly to your drawing, your trades could look at it right then and there and give an instant response, and everything was tied into the budget. That was huge," said Early.
Intuitive and user-friendly
The best part was that the platform was intuitive and user-friendly, so team members quickly learned how to use the software.
"We wanted to get as many tools as possible because our onsite guys really adopted it quickly. They started using the daily logs within a day, and that was really important to us," Early recalls.
Early explains that by switching to Procore very early on in the project, their team saved hours, and he notes that not having Procore would have severely hindered progress of The One. "It's such a huge project that any little change could get lost. But with Procore, we have everything tracked so we can easily revisit things a couple of weeks or a year later to make sure nothing gets missed."
In addition to enhanced documentation, Procore also helped streamline processes by automating workflows. So much, in fact, that Clark was able to eliminate two positions on the project (document control and assistant document control), thereby reducing staffing costs and improving the project ROI.
"With Procore, you don't have to distribute documents to anyone because everyone gets notifications when things are uploaded. Submittals and drawings are a lot simpler too. It's such a beast of a project that we have four project managers, and each one can do their own submittal and not have to go through a single point of contact. So Procore has definitely eliminated the need for more bodies in our office."
Tools save work time daily
Early goes on to say that this submittal process, which was once a 20-minute process, is now just five minutes. Similarly, Procore's Meetings Tool reduced meeting minutes from an hour-and-a-half task to just 30 minutes. Daily logs, too, went from an hour to just 10 minutes.
"Superintendents can do daily logs on the fly. They can be out on the field and can type it all in as it's happening – even if they're offline. They don't need to go back to the office and work for an hour at the end of the day. That way, they can actually focus on doing the more important parts of the job, and they can be more present while the construction is happening."
Procore's Reports Tool also saved Clark's team hours when writing monthly reports to investors, and the Daily Log Tool similarly proved especially useful.
"Our general superintendent's jaw hit the floor when he first saw that the weather was automatically put into Daily Logs. He didn't have to go check the weather on his computer and grab a screenshot and put it into his homemade sheet. He said, ‘I'm going to have so much time on my hands – I'm not going to know what to do.' Of course, he hasn't run out of things to do yet, but it was a big time saver."
Early says that with so many collaborators on the project, Procore's ability to boost communication has been critical, a benefit which he largely attributes to Procore's unlimited user license model.
"Having unlimited users is one of those things that you don't realize how good it is until you have it. The scale of this job requires hundreds of guys onsite, all accessing Procore, and we don't worry about how many people are using it at one time."
Easier work tracking
He says that Procore has also helped provide greater visibility both onsite and off.
"The owner can easily and quickly get an all-encompassing view of where their money is going. That same visibility happens onsite too; if our super tells someone to do something, everyone can see that on their observations. Everyone is aware of what needs to be done, and there's accountability. A lot less falls through the cracks because everything is documented and has deadlines attached to it."
Early concedes that for a project of such magnitude, employing the most comprehensive toolset and the most advanced team have both been critical in ensuring success. "The scale of it is just huge. All the trades and all the people who are a part of it are bringing their best guys to make the project as spectacular as the developers want it to be."
Along with the best guys, as Clark and Mizrahi discovered, it also takes strong project management software to successfully reach the top of the Canadian skies.
Company info
04-128 1 University Avenue
Toronto, ON
CA, M5J 2P1
Website:
procore.com
Phone number:
(866) 477-6267