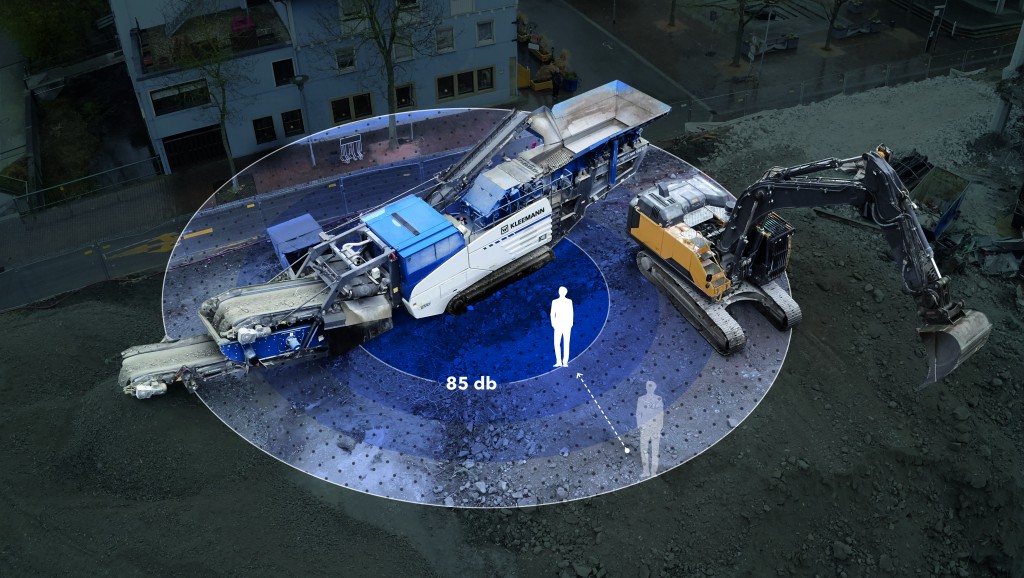
Modern crushing plants have become more and more complex as their requirements rise. At the same time, the technology must be safe and as simple as possible to operate – and without lengthy instruction and familiarization periods. This is the challenge which faced Kleemann. At bauma 2019 Kleemann showcased innovative solutions for the safe and simple operation of crushing and screening plants.
Simple and comfortable operation
The control system is the interface between operator and machine. The entire PRO line and the MR 130 Z EVO2 impact crusher can be comfortably operated via the intuitive SPECTIVE control concept. The 12-inch touch panel simplifies work as all functions are visible at a glance and clear symbols point the way. The user interface is not affected by dust, is splashproof and can be easily read in difficult lighting conditions. A simple menu guidance guarantees that only the information which is currently required is displayed on each page. This concept makes it possible to use the crushing plant properly in a simple manner and fully utilize its functions.
Low-noise work close to the machine
The new option package for noise reduction ensures comfortable and safe work close to the impact crusher. Noise protection flaps mounted on the side at the same height as the engine deflect sound upwards. These flaps are folded in for transporting the plant and therefore have no impact on the transport width. The bottom of the unit is also sealed off from noise. The volume perceived by the user is reduced by six decibels. A reduction of three decibels has the effect of halving the amount of noise perceived by the human ear. This makes possible low-noise work in a significantly smaller area around the machine.
Excellent accessibility and safety during maintenance work
The design of the machines offers good access from all sides. Designed on the basis of the material flow, all components of the plant are easily accessible for the user. For example, it is possible to refuel the MCO 11 PRO cone crusher comfortably from the ground and the prescreen surfaces for the MR 110 and 130 Z EVO2 impact crushers can be easily changed via an extra platform. Other service work on the machine can also be completed quickly and comfortably thanks to the good accessibility.
The award-winning "Lock & Turn" system provides the highest level of safety during rotor ledge change at the mobile impact crusher and when releasing bridging. Here special keys are used that only permit work in certain areas of the crusher. There the operator can open service flaps or move and exchange components. If the user wants to work on another area, the keys must be removed, which automatically blocks the area worked on previously. Apart from the key system, a rotating device also allows the rotor of the crusher to be turned and blocked manually in any position from the outside using a gear. The exchange of rotor ledges and the elimination of bridging can be carried out even more safely.
Company info
6030 Dana Way
Antioch, TN
US, 37013
Website:
wirtgen-group.com/america/en-us/products/kleemann
Phone number:
(615) 501-0600