How to maximize cone crusher performance
Maximum crusher performance results in greater uptime, increased production and reduced maintenance costs
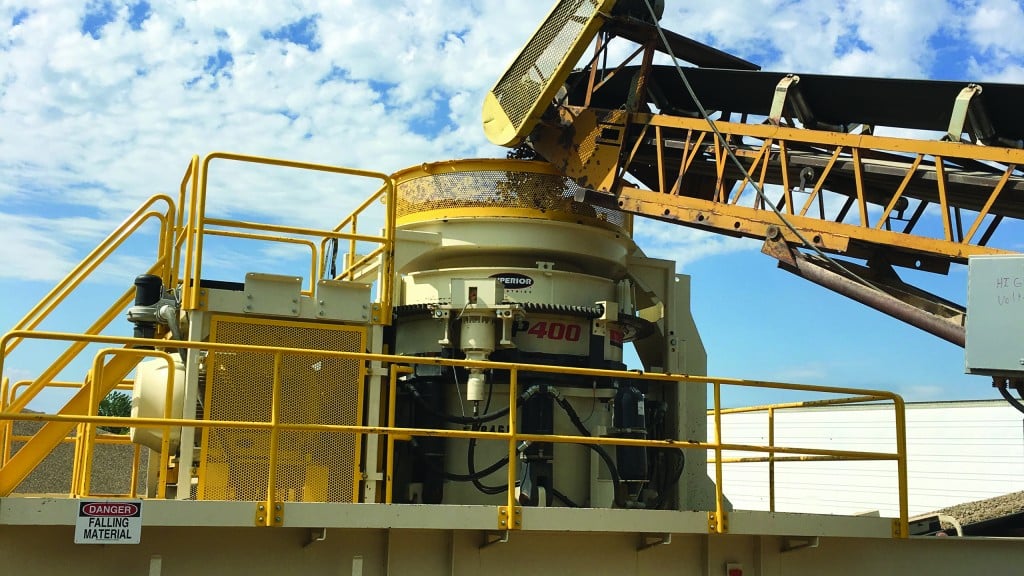
Every producer wants peak crushing performance but not every producer knows how to achieve it. Getting there may require just a few tweaks or a total rebuild, while remaining at peak levels requires proactive maintenance practices, combined with expert consultation and continuing education, according to Mike Schultz.
As crushing product manager for Superior Industries, Schultz brings more than two decades of crushing industry experience to their team of product, parts and service professionals.
"Maximum cone crushing performance requires a complete understanding of the application parameters, the design limitations of the crushing machine and the processing circuitry needed to support that machine," he emphasizes.
A cone crusher uses compression to effectively crush abrasive material, as well as a wide variety of stone from medium to very hard compressive strength. It is a versatile machine that can be used in all phases of material reduction, from the rock face to product finishing but more often than not its duties are targeted to secondary, tertiary and quaternary aggregate and mining applications.
Schultz explains that from a bottom-line standpoint, to maximize performance and cut wear costs means you need to get every stone through a crusher that you safely can, while preventing any crusher damage, and still meet or exceed production goals.
What is the difference between a jaw crusher and a cone crusher?
The two most popular pieces of aggregate equipment in the market include cone crushers and jaw crushers. While cone crushers and jaw crushers both perform a similar job of breaking rocks, their approach and applications are quite different.
A jaw crusher also uses compressive force and the materials are allowed into a gap at the top of the equipment between two jaws. One of the jaws is fixed while the other reciprocates by moving back and forth relative to the stationary one. The gap between the two jaws is known as the crushing chamber. The moving jaw exerts a compressive force against the stone in the chamber causing it to fracture and reduce. The rock remains in the jaws until it is small enough to move down the chamber to the opening at the bottom.
Jaw crushers can work on a range of stone from the softer ones, like limestone, to harder basalt or granite. Feed material is reduced by squeezing it between a moving piece of steel and a stationary piece of steel, with the discharge size controlled by the gap setting, or the space between those two pieces of steel. The tighter the setting, the smaller the output size and the lower the throughput capacity.
Jaw crushers are mainly used in primary crushing stages and are rarely used for secondary crushing. As a compression crusher, this type of machine generally produces the coarsest material because it breaks the rock along its natural lines of weakness. Jaw crushers are an excellent primary stage solution to prepare rock for subsequent processing stages, such as washing, classifying or secondary crushing.
A cone crusher is similar to a gyratory crusher because it operates using a mantle that rotates within a bowl, but it has less steepness in the crushing chamber. It has a short spindle which is supported by a curved universal bearing located beneath the cone. They use compression force to break the rock between the gyrating spindle and the enclosing bowl liner. The rock becomes wedged and squeezed as it enters the top of this rock crushing equipment. The cone crusher breaks large pieces of ore once into smaller particles that fall to a lower position where they are broken again. The pieces are continually crushed until they are small enough to move through the narrow opening at the bottom of the crusher.
Solutions and strategies to maximize cone crusher performance
Whether specifying a new machine or fine-tuning an existing crushing circuit, all key parameters must be defined upfront, Schultz says, and that means defining the work that you want that cone crusher to do.
To do this, operations must provide data on proper feed gradation, desired output gradation, tonnage requirements and, most importantly, the material type. In addition, knowing the precise composition, compressive strength (maximum force that material can withstand before breaking) and chemical properties of the stone is a huge factor in determining how much work a crusher needs to do.
"Many operations try to do too much with one machine, pushing it beyond its design limitations, causing excessive component stress and wear and the potential of serious damage," Schultz says.
Cone crushers are designed for certain reduction ratio limitations
In most cases, cone crushers provide reduction ratios (the ratio of the feed size to the crusher vs. the size of the crusher discharge) of 4-to-1 up to 6-to-1. "The reduction ratio design limitations and the rated capacity (tons per hour) of the cone crusher are the most important factors to consider when designing a crushing circuit - and determining how much that crusher can safely do," Schultz says.
Crushing chamber and liner configurations matter
Once complete application data is in hand, it's important for operations to work closely with their supplier to select the right cone crusher. Key considerations will be crushing speed, crushing chamber design, liner configurations and crusher settings.
"Whether it's minimizing fines or maximizing fines, or trying to create the highest yield of a particular product, there are crushing chamber and liner configurations designed specifically to meet the desired product yield," says Schultz.
Designing the right circuitry to maximize crusher efficiency
For performance efficiencies, proper circuitry should be designed around the crusher cone, says Schultz. Importantly, the circuit should be engineered to provide the crusher cone with choke-fed material, or enough material to keep the crusher full. Having too little feed can cause the crusher to side load, which stresses components. Also, having too many fines in the feed leads to premature wear issues.
Having adequate screening capacity downstream of the crushing circuit is another key factor. In a closed-circuit setup, material that is not properly sized is recirculated back to the crusher for further reduction.
"It's very common to see operations that have a bottleneck at the screening circuit. They do not have enough screening capacity, so properly crushed material is sent back to the cone. These unnecessary recirculating loads simply eat up more space and horsepower in the crusher while increasing wear," says Schultz.
Make use of automation to help extend the life of the cone crusher
"To significantly affect cone performance, automation doesn't need to be over-the-top and super complicated, but rather quite simple and very easy to control," Schultz emphasizes.
One of the biggest things that automation delivers is protecting the crusher from damage by acting as a warning system that alerts operators to conditions such as bowl float, excessive amperage or temperatures, and lubrication or low-flow oil issues.
As an example, he points out that Superior's Patriot Cone series features a three-sensor "bowl float" or "ring bounce" monitoring system that alerts the operator if conditions are over exceeding the design limitations of the cone. The top and the bottom of the cone are held together by hydraulic cylinders.
When the crushing action on the cone exceeds the pressure that is holding those two pieces together, it causes bowl float or ring bounce, which is any movement at all (even slight) between the top and the bottom of the cone crusher, Schultz explains. Undetected bowl float will eventually lead to component failures. "When operating a cone, preventing bowl float is arguably the single most important thing you should ensure."
Most cone crushers are designed to open up due to tramp metal or an uncrushable situation. However, no cone crushers are designed to operate under normal conditions with ring bounce.
"There should be zero ring bounce or bowl float under normal operating conditions," says Schultz. "Without an automation package, it can be difficult to detect ring bounce at times. You can literally be standing on the machine, and you cannot detect even the slightest ring bounce - so having that automated warning system is an enormous advantage."
Know the true limiting factors and the best closed-side setting for the job
One of the major misconceptions Schultz encounters in the field is the way operators view the closed-side setting (the material discharge opening from maximum to minimum) of the cone. He says that operators often try to maintain a specified closed-side setting, assuming that will yield the desired product output no matter what. Often, they close the setting down to the smallest point possible and then let the crusher beat itself up. Schultz suggests a better approach to setting up a cone for maximum performance.
First, consider the true limiting factors of any cone crusher are attached power and crushing force. After determining the proper speed and liner configuration, it is possible to dial in the proper settings of the crusher based on maximizing the amp draw to a desired set-point, while making sure that the machine does not incur ring bounce at that point.
He also encourages operations to tie an automated warning system into the designed amperage utilization of the crusher. With Superior's automation package, "if the motor and the machine are being overworked, the system will either take steps to reduce the amp draw, or will send an alarm to the operator," he explains.
Automation features maximize the life of wear components
Patriot Cone's auto-wear compensation, included in the automation package, is an example. As liners begin to wear, the cone crusher is designed to automatically compensate for that wear in order to maintain the same settings in the machine. With liner wear, the space between the two compression components expands. At the same time, the auto wear compensation system automatically closes the crusher down to maintain proper settings throughout the life of the wear components.
What are the different types of cone crushers?
Gyratory crushers
While there are many similarities between gyratory crushers and cone crushers, such as both using a cone-shaped crushing surface, the main difference lies in the speed at which the mantle travels while crushing materials. Gyratory crushers are generally used for primary crushing, whereas cone crushers are used for secondary or tertiary crushing.
Single-cylinder hydraulic cone crusher
Single-cylinder hydraulic cone crushers are used for the fine crushing of materials such as ore, limestone, sandstone and granite. Benefits of this type of cone crusher include low operating costs, less consumption of wear parts, and produce a uniform particle size.
Multi-cylinder hydraulic cone crusher
Multi-cylinder hydraulic cone crushers are most suitable for secondary and tertiary crushing due to the fact that they can handle larger crushing forces that are suitable for materials such as ore, construction sand and stone processing. With a high capacity and a strong crushing force, they are generally used for crushing medium and hard materials.
Symons cone crusher
Symons cone crushers are mainly used in fine crushing and reduction. A Symons cone crusher can be used for secondary, tertiary or quaternary crushing as they feature a flatter chamber and have a rotational speed that is nearly double that of a primary gyratory crusher.