Co-developed by Kohler and Liebherr, new Kohler G-Drive diesel engines feature modular design for optimal serviceability
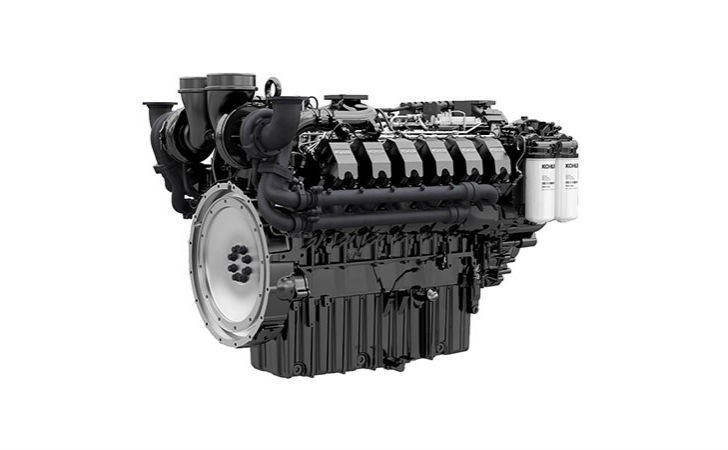
An entirely new line of G-Drive engines was developed to exclusively power the recently launched KD Series of KOHLER and KOHLER-SDMO diesel industrial generators. The compact and powerful new engines, co-developed by Kohler and Liebherr, deliver highly efficient and dependable performance and feature a modular design for optimal serviceability.
“A global team of engineers came together and worked tirelessly to design and develop these new large diesel engines, which will only be available on the just-launched line of KOHLER and KOHLER-SDMO industrial generators,” said Tom Cromwell, group president-power for Kohler. “We’re pleased to be integrating a premium new engine into these generators that combines a compact footprint with unrivaled power density.”
In total, there are six engines within the new line, which deliver between 709 and 3,608 kWm Standby Power at 50 Hz and between 891 and 4,250 kWm Standby Power at 60 Hz. The new line is divided into two series – the 135 series and the 175 series – both containing three engines. The 135 series includes the KD27V12, a 12-cylinder model with 135 mm bore and 27 litres displacement; the KD36V16, a 16-cylinder model with 135 mm bore and 36 litres displacement; and the KD45V20, a 20-cylinder model with 135 mm bore and 45 litres displacement. The 175 series also includes three engines: the KD62V12, a 12-cylinder engine with 175 mm bore and 62.4 litres displacement; the KD83V16, a 16-cylinder model with 175 mm bore and 82.72 litres displacement; and the KD103V20, a 20-cyliner model with 175 mm bore and 103.40 litres displacement.
Both the 135 and 175 series of engines incorporate a modular design with common components, allowing for efficient servicing, reduced spare parts inventory, and more streamlined technician training. Other key features include:
- An innovative fuel system by Liebherr with common rail injection, which reaches pressures up to 2,200 bar to deliver better atomization of fuel and improved fuel consumption;
- This precisely-metered fuel injection system also minimizes engine particulates, reduces emissions, and helps the new engines to meet global emission regulations in all markets;
- An advanced Engine Control Unit (ECU), which is supported by KODIA diagnostic software for intuitive monitoring;
- A unique turbocharger system, which optimizes airflow to the cylinders for maximum power, optimal combustion, and reduced fuel consumption;
- A low-noise combustion system with optimized pressure, which works in combination with a rigid engine block, crankcase and sub-frame to significantly reduce noise and vibration.
“These feature-rich engines were purposefully designed to deliver unequaled performance and ultimate reliability in the field,” Cromwell continued. “Together with Liebherr, we carefully test each component and engine under rigorous operating conditions and utilize an advanced quality management system to monitor every step of the development process. These procedures were put into place to ensure the highest level of engine quality and dependability.”
Company info
1015 Sutton Drive
Burlington, ON
CA, L7L 5Z8
Website:
liebherr.com/en/can/about-liebherr/liebherr-worldwide/canada/liebherr-in-canada.html