Drilling into a Great Lake
CC Underground faced some unusual challenges in boring a pipeline for Hydrostor Inc., the company behind the world’s first underwater compressed air energy storage system
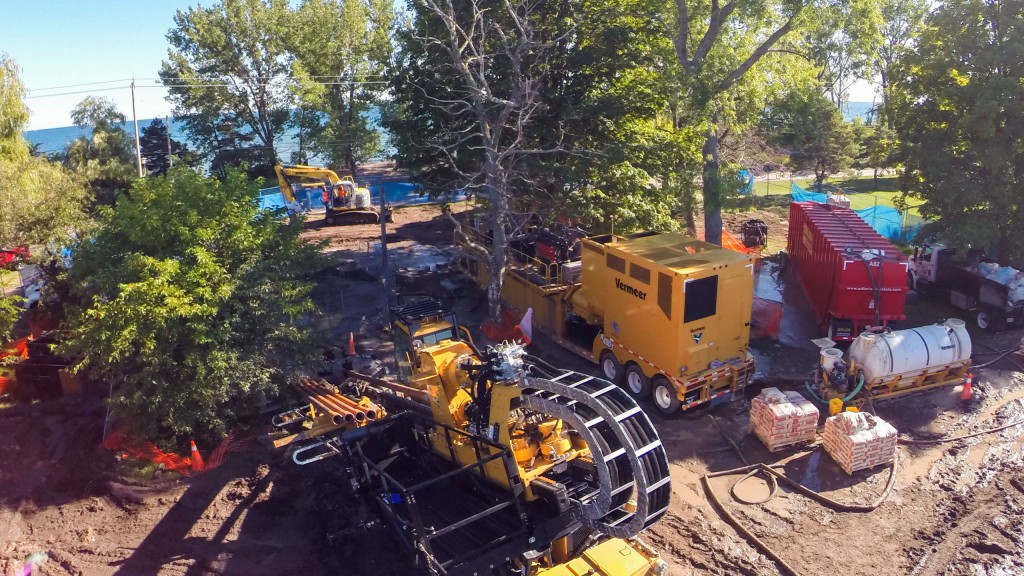
It is not unusual to encounter a body of water on an underground construction project. It is unusual, however, to intentionally drill into a body of water.
But that’s exactly what CC Underground did on a horizontal directional drilling (HDD) job that was part of a recently completed larger project – and it was far from the only unusual thing about the work. Here are a few examples: drilling into a Great Lake, having a dive team locating, attaching a reamer from a barge, and having a drill break down during the pilot bore and buying a larger rig from a different manufacturer to finish the job.
“This job required a lot of outside-the-box thinking,” says Scott Anderson, project manager for CC Underground. “That’s what made the project very interesting right from the beginning – there were all these things that we hadn’t done before, and we had to figure out how to overcome all these unique challenges.”
Even the larger project CC Underground was hired to work on was one-of-a-kind. The company installed a pipeline that was part of what project owner Hydrostor Corp. says is the world’s first underwater compressed air energy storage system.
Hydrostor says its technology works by running electricity through a compressor and converting it into compressed air. The compressed air is sent underwater, via a pipeline, where it is stored in large balloon-like structures. When electricity is needed again, the weight of the water pushes the air to the surface through the pipeline and to an expander, which converts the air back into electricity.
The storage station is approximately 2.5 kilometres offshore from Toronto in Lake Ontario. The pipeline runs between the storage area and a land station on one of the Toronto islands.
Taking a ferry to work
CC Underground was contracted to install the first portion of the 12-inch (30.5-cm) steel pipeline, running from the island to about 1,000 metres into Lake Ontario. The family-owned company, headquartered north of Toronto, installs everything from telecom lines to large pipelines and specializes in trenchless technology. With 30 employees, Anderson acknowledges the company is on the small side in the industry, but he sees it as an advantage.
“One of the things that sets us apart is we’re family owned, and the people who work here are like family because we’ve been here for a long time, so there’s a very close bond and everybody’s got a great deal of pride in their work,” he says.
The Hydrostor project is something the company is rightly proud of. CC Underground’s pipeline kicked off the construction portion of the project in summer 2014.
The primary motivator for using horizontal directional drilling was minimizing the effect on the surrounding environment. There is a lot of animal and plant life near the shore of the island, and HDD could protect them best.
Just getting equipment and crew members to the jobsite was demanding. There was no road access to the island. Instead, it was a two-hour ferry ride one way. Equipment had to be transported one piece at a time when room could be coordinated on a commercial ferry.
The jobsite itself also presented challenges. CC Underground was given a small footprint for setup. The crew’s horizontal directional drill sat about 80 metres from the water, but a public road was 20 metres behind them. While vehicle traffic was light, there were a lot of pedestrians along the road because the island is a popular tourist spot. There were noise restrictions on equipment, and CC Underground had to put up a fence to keep the project as out of view as possible.
Another space constraint was a field of radio towers near the rig. These towers also created signal problems when it came to locating.
New rig bought mid-bore
Mobilization started in mid-June 2014, and the drilling commenced at the end of the month and lasted into August.
Just over halfway into the pilot bore, the company’s 100,000-pound (444.8 kN) HD drill experienced a mechanical issue. The mechanical fix would take longer than the job allowed, and a replacement drill from that same brand was not immediately available. CC Underground, which had been considering purchasing a larger rig, determined Vermeer could meet their needs faster and bought a new Vermeer D220x300 Navigator horizontal directional drill. Also important was that the 242,100-pound (1,076.9 kN) drill fit in the tight footprint on the Hydrostor project. The company also bought a Vermeer R9x12T reclaimer.
“You can appreciate that time is of the essence, especially when you’re working in a body of water like that,” says Christian Meyer, one of the owners of CC Underground. “We didn’t want to wait for everything to be repaired.”
They had the new rig on the island five days after the other drill experienced the mechanical issue. In that time frame, financing, transportation, product support and training were completed. The equipment also had to clear customs because Vermeer sent them up from Ohio.
Coordinating this was the Vermeer Canada dealership. Additionally, several Vermeer Canada employees were at the jobsite for training and to make sure everything went smoothly.
“Everybody worked very hard to make this happen,” Meyer says. “No one said, ‘We’ll deal with it tomorrow.’ It was, ‘We’ll deal with it at 8 or 9 at night,’ because they realized what kind of timeline we were dealing with.”
Locating in a dive suit
Soil samples showed the bore path started in a soft silt before transitioning to more consolidated soil and finally hard sand as they drilled deeper. CC Underground used a 25.4-cm mill tooth style bit manufactured by Vermeer to cut through the hard sand.
Hydrostor required a minimum cover of at least 9.1 metres to keep the airfilled pipe, which in water would have a tendency to float, in place and to account for potential future changes to the lakebed caused by nature. To give their client even further protection, CC Underground went as low as 45.7 metres (150 feet) deep.
Locating was an adventure unto itself. The crew would have preferred to use a wireline system to track the drill head under water, but the nearby radio towers created interference. A walkover locator was used on approximately the first 350 metres of the pilot bore. How does one do a walkover in a lake? In CC Under ground’s case, they hired a commercial dive team.
“They did a walkover locate under water just like you would do on land except he’s walking on the lakebed with a dive suit on,” Anderson says.
Interference was still an issue, so a system of lines was set up running from the locator to a boat. From there the information was transmitted to the rig.
This brings up another challenge of drilling into a large body of water: the unpredictability of the weather and the condition of the water. There were days it was sunny but waves were 3 metres (9.8 feet) high, making it difficult for the locating team. Or the water would be extremely murky. And even in the summer and with wetsuits on, the water down deep in Lake Ontario is cold, preventing divers from working long stretches.
“We had to pick our days wisely,” Meyer says. The interference became less of an issue farther from shore, and the crew finished the pilot bore with a wireline. While waiting for the Vermeer rig to arrive, CC Underground took the opportunity to build a grid by placing a series of large cement blocks along the bore path and having divers run a wire from corner to corner. The blocks were necessary because the current was so strong.
“We had a lot of discussion and creative thinking on how to make things work,” Anderson says.
Tugboats then pullback
The exit point for the pilot bore was in about 13 metres (42.7 feet) of water. The day they were going to break through, the 1,000-metre (3,281 foot) string of steel pipe was brought out from a docking station on mainland Toronto. It took from 7 a.m. to mid-afternoon for a couple of tugboats to get it in position. There were permits specifically for this portion of the job, and law enforcement and marine contractors were involved to help ensure safety on public waters.
Once the pipe was at the receiving area, a crane on a barge was used to help keep it in position. A couple small lines were run into the pipe so water could be pumped into it to keep it at neutral buoyancy, meaning it would not sink or rise. This let crews suspend the pipe exactly where it needed to be to line up with the drill string at a favourable angle.
Meanwhile, the drill stem was lifted onto the barge so a reamer could be attached. CC Underground used a 20-inch (50.8 cm) stacked plate reamer. Once everything was in place, pullback took 30 hours.
“The Vermeer 220x300 did exactly the job it was supposed to do,” Anderson says. “It helped us finish the project.”
Drilling additives kept minimal
Drilling fluid management was another critical component of the project. Drilling in a body of water, the crew had to be careful of inadvertent returns, and they kept additives to a minimum. They also installed a series of weeper subs during the pilot bore to keep the hole lubricated.
CC Underground co-owner Matthias Meyer says they bought the Vermeer R9x12T reclaimer because of the number of desanding cones it has, which was essential given the silt and sand they were drilling through. Also, its tank capacity of 32,403 litres (8,560 gallons) provided the volume of drilling fluid they needed, particularly on the pullback.
CC Underground wrapped up its work in August 2014. Hydrostor’s underwater energy storage system was activated in November 2015. Anderson says with all the unique aspects of this job, what he’s most proud of is how his co-workers performed.
“You’re out on an island, the days are long, the ferry rides back and forth are tedious, to say the least,” he says. “All of our staff stuck through the challenges on a project that was new for everybody.”