Concrete dowel pin drills more accurate and up to 10 times faster
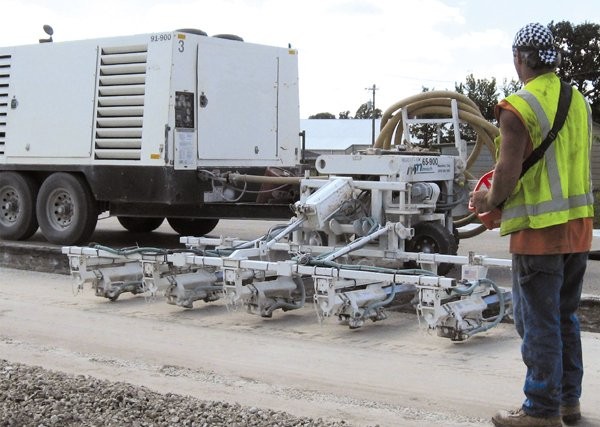
A number of contractors still use hand-held drills to create dowel holes whenever a new slab of concrete must be secured to an existing slab, such as adding another lane to a highway. This method has worked fine for years, so many people feel that if the system isn’t broken, there’s no need to fix it.
Where hand-held drills fall short, however, is their speed and accuracy. Even if a worker has the luxury of a sharp new drill bit, 50 dowel bar holes will still take a very long time to drill, especially if they are specified at a wide diameter.
The struggles of drilling dowel holes with speed and accuracy in concrete slabs didn’t go unnoticed, and in the 1980s, manufacturers began developing specialized dowel pin drills for contractors who faced this type of work often. After more than 20 years of development, the equipment is now offered in multiple configurations and power options.
Smaller drills, such as one- or two-gang units, are only available with pneumatic power, due to cost efficiencies. Larger drills, such as five-gang units, can be found with either hydraulic or pneumatic power. Various configurations are also available to operate from the top of the slab or from the sub-grade, and there are even equipment-mounted drills available. Despite the type of unit, however, all types of dowel pin drills have been proven to drastically increase productivity and safety on the jobsite.
The enhanced productivity of dowel pin drills comes from their faster speeds and heightened accuracy. A single-gang unit can drill a hole up to ten times faster than a hand-held drill, so for every hole created with a hand-held drill, a single-gang dowel pin drill could potentially produce 10 holes. And multi-gang units can drill multiple holes just as quickly. For example, a five-gang drill can drill five holes in the same amount of time that a single-gang unit can finish one.
The previously stated numbers only take drilling time into account, but dowel pin drills can also set up from hole to hole faster than hand-held drills. The operator simply positions the unit on centre for the first hole, and then he can run the length of the slab using the same setting. When finished drilling, each hole will be at a consistent angle and distance according to the top of the slab. In contrast, hand-held drill operators must take time to reposition themselves at the start of each new hole.
Because dowel pin drills use the slab as a reference, they’re extremely accurate. Contractors no longer need to rely on the good eye and steady hands of an experienced hand drill operator to pass inspection. Now, each hole can be easily drilled straight and centered, resulting in high quality work and virtually eliminating the need to ever redrill holes.
From a safety standpoint, hydraulic and pneumatic dowel pin drills are also equipped with several features to help prevent workers from getting hurt on the job. For starters, operators have less chance of being injured since they can work in an upright position, rather than being bent over holding a heavy, vibrating hand-held drill. Additionally, certain configurations of dowel pin drills can increase safety in specific situations. For example, when a patching job takes place near heavy traffic, on-grade models can be used. This keeps both the drill and the operator in the sub-grade and farther away from moving vehicles.
Remote controls
Additionally, some larger drills come with remote controls, which let the operator keep a safe distance from the drill, vehicles and any flying debris. However, exposure to harmful flying debris and concrete dust can be further minimized if the dowel pin drill is equipped with a dust collection system.
The one performance disadvantage of dowel pin drills is their size. Although they’re fairly compact, there are still some areas where they simply won’t fit. However, some manufacturers are working on new models of drills to address this issue and currently offer models that fit inside a 24-inch opening.
The other consideration that keeps contractors from purchasing dowel pin drills is the initial cost. Of course, these units cost more than hand-held drills, but by doing the math and determining return on investment, one can decide if dowel pin drills are right for his operation, rather than simply putting more men on the job.
Doing the math
Let’s take an example of a concrete patching job where 100 dowel holes need to be drilled. The holes must be 10 inches deep and three-quarters-of-an-inch in diameter.
Depending of the quality of the drill and experience of the operator, a hand drill can bore one of these holes in anywhere from 45 seconds to more than two minutes. However, for this example we’ll assume the operator is skilled and averages one minute per hole, which means he can do 100 holes in 100 minutes, or an hour and forty minutes. Figuring in a wage of $25 per hour, the contractor must pay more than $40 in pure drilling time.
Next, consider a single-gang, dowel pin drill, which has been tested to drill a hole with the same specifications in 14 seconds. To complete 100 holes at this rate, it takes only 23.3 minutes and costs under $10 at the same $25-per-hour rate. That’s less than a fourth of the time and cost of doing the work with a hand drill. Multiply this out over several years and thousands of holes, and the result is very significant cost savings. These numbers don’t factor in the time to set up in-between holes, which can also be done faster with dowel pin drills, thanks to their easy repositioning features.
This example only calculates the time for a single-gang drill. For instance, if a four-gang unit is used to drill four holes at once, the drilling time for 100 holes is only 5.8 minutes. Not to mention, the operator needs to reposition the drill fewer times, resulting in additional labour savings.
Furthermore, consider the initial cost and lifespan of the equipment. A good-quality hand-held drill might cost only $1,000, but then again, it may need to be replaced every two years, or more often, depending on how much it’s used. A single-gang pneumatic drill, on the other hand, may be priced in the ballpark of $7,500 and last ten years or more, as long as the operator performs regular maintenance. In fact, some contractors are still using dowel pin drills that they purchased in the 1980s. With this in mind, a contractor could go through $5,000 worth of hand drills in the same period as one $7,500 pneumatic dowel pin drill. That significantly narrows the cost difference one must make up through increased productivity, which should be no problem at all, considering the time savings outlined above.
Obviously, time equals money, but there are benefits beyond the labour savings.
First, dowel pin drills place less stress on the operator, which helps reduce the potential of worker’s comp claims and keeps workers at the top of their game.
Next, dowel pin drills produce higher quality holes than hand drills, so the work can pass inspection much more easily.
Finally, contractors are able to bid more competitively on jobs and are more likely to meet, or beat, deadlines. And by completing more jobs ahead of schedule, the contractors open themselves up to more bonuses.
Considering the extremely quick return on investment, it’s a wonder why many contractors haven’t yet embraced dowel pin drills for patch work. Compared with hand-held units, dowel pin drills can produce better, straighter holes in a much faster time and in a safer manner. But until this equipment becomes the norm on jobsites, you can make it one of the tricks up your sleeve to give you the winning hand on future bids.