Swapping rotors on grinder makes it more versatile
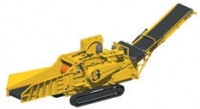
What makes the Magnum Force 6400-T particularly unique is its ability to accept three different rotors – forged, solid steel, and chipper – and its ability to swap rotors in just a day’s time. You can go from making high quality mulch from trees and stumps, to chipping stemwood into chips in custom sizes ranging from 2 to 30 mm, to grinding highly contaminated C&D or railroad ties with the tie plates attached, just by swapping rotors and screens. “We’ve found that several of our customers have their grinding needs change depending on the time of year, or the client base that they have in their area. For six months, they may need to process construction and demolition debris, but then they may get a customer that needs to have a 100 acre tract of land cleared, or a customer that needs to make a chip for fuel,” notes Mark Taitz, director of business development for Continental Biomass Industries (CBI). “While it may be cost prohibitive to have two or three separate grinders, keeping a spare rotor in stock for opportunities as they become available is not only economical, but it allows our customers to be competitive in the marketplace no matter what the job requirement.” In travel mode, the 6400-T is only 12.44 metres (40 feet 9 inches) long, 2.99 m (9 feet 9 inches) wide, and 3.82 m (12 feet 5 inches) high, and weighs about 80,000 pounds.
The 6400 series is available in either track or portable configurations. It features a clamshell opening on the hog box that affords complete and easy access to the rotor and screens, a unique wrap-around grate frame with 172 degrees of screen area, a choice of C-18 or 3412E CAT engines with ratings from 700 to 1,000 hp, CBI’s Replace-A-Face hammers on the four-inch-thick forged drum rotor, and a new mor-tice and tennon fit for affixing strikers to the lobes of the solid steel rotor, reducing movement and thus reducing wear substantially on the leading edge of the striker.
The unit also features an upgraded version of CBI’s IntelliGrind operating system that improves feed speeds and production by advancing and optimizing the staging of material being fed into the hog chamber.
The 6400 series is available in either track or portable configurations. It features a clamshell opening on the hog box that affords complete and easy access to the rotor and screens, a unique wrap-around grate frame with 172 degrees of screen area, a choice of C-18 or 3412E CAT engines with ratings from 700 to 1,000 hp, CBI’s Replace-A-Face hammers on the four-inch-thick forged drum rotor, and a new mor-tice and tennon fit for affixing strikers to the lobes of the solid steel rotor, reducing movement and thus reducing wear substantially on the leading edge of the striker.
The unit also features an upgraded version of CBI’s IntelliGrind operating system that improves feed speeds and production by advancing and optimizing the staging of material being fed into the hog chamber.