Is your mine ready to adopt teleremote technology?
Discover the benefits of this versatile technology and determine the best teleremote solution for your operation
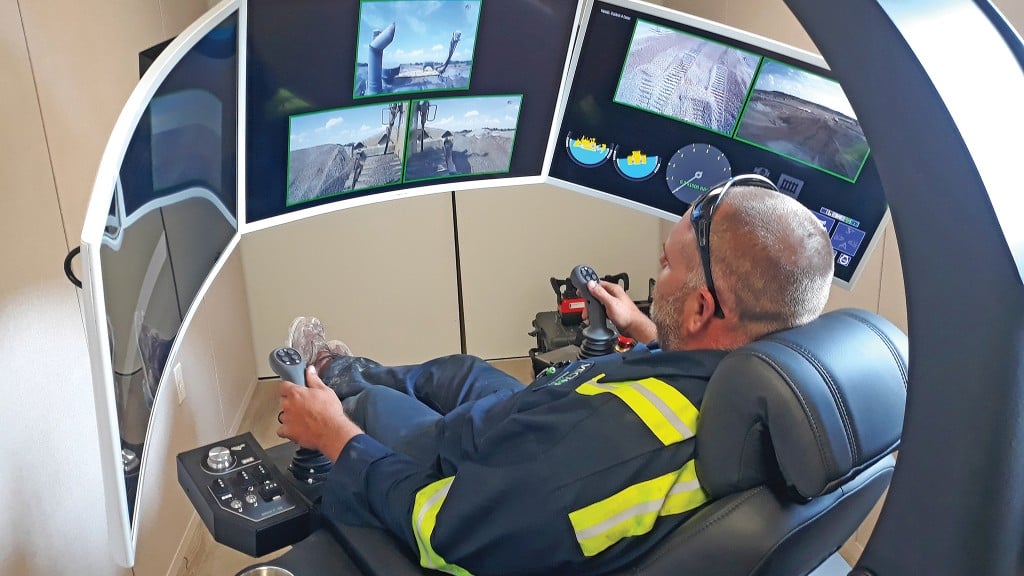
Teleremote technology is changing the mining game in Canada. Introduced about 40 years ago, it continues to innovate to meet the ever-more-sophisticated needs of mining operations. This versatile technology can tackle many different challenges, says Paul Oldenburg, manager, Smart Mining Solutions at SMS Equipment. "It's a broad space in terms of what you can do with the equipment."
Key benefits of teleremote technology
Teleremote technology offers many benefits — to your operations, your team, and your bottom line.
Enhanced safety
Safety is one of the primary benefits of integrating a teleremote solution into your mining operations. With your operators either in a remote location or at a distance from the machine in a line-of-sight scenario, the risk of accidents and injuries is significantly lowered. "Now the risk is just the asset," says Oldenburg. "We're eliminating the human aspect of it."
Operational flexibility
Depending on your objectives, operation, and budget, there are two options: OEM or aftermarket. If you're ready to replace your fleet, an OEM solution is the way to go: The technology is pre-installed and fully integrated with the equipment. If you prefer to work with what you have, an aftermarket solution can be installed in your current equipment. Both OEM and aftermarket teleremote options can leverage automated functionality and be deployed in underground and surface operations.
Talent attraction
The "grey wave" of mass retirement that mining is experiencing, coupled with a general labour shortage, is putting pressure on the industry. Alleviating the need to be on-site in typically challenging locations, teleremote technology widens the net of people you can attract. Rather than a fly-in, fly-out role, your staff can go to an office that's closer to home and is much more comfortable. It's also attracting a younger generation, one that grew up playing video games and is familiar with similar interface experiences.
Increased productivity
Instead of a 1:1 ratio of operator to machine, with a teleremote-enabled operation, one person may control many machines. This means that only four or five operators are usually required compared to the traditionally larger team necessary to cover all your shifts. Without having to travel to and from the mine site, your operators can maximize work time, and the downtime for shift changes or breaks is minimized. As well, the need for on-site infrastructure is reduced, there are fewer safety-related stoppages, and your equipment usage is optimized.
Training efficiencies
Because you are no longer restricted to radio communications with an operator in a cab, it's faster and easier, with training happening in-person, side-by-side. And for individuals who are already adept with joystick controllers and accustomed to 2D spatial awareness, the learning curve can be faster.
Reduced emissions
Under conventional staffing, you might schedule an operator to a machine for many hours. With a person on board, the cab must be climate-controlled for their comfort. This means equipment may be left idling when not in use or while waiting for other equipment. With teleremote technology, your machines run only when needed. So, when equipment isn't in use, it can be shut down, saving on emissions.
Getting started
To determine how teleremote technology can benefit your operations, and what solution makes the most sense, start by answering these questions:
What is your need?
Implementing teleremote technology starts with understanding your mine operation's use case. What is your impetus for adoption? What are your challenges? Objectives? Defining all this up front is critical, says Oldenburg. "Once we understand your challenges and applications, we can tailor the best solution."
OEM or aftermarket?
Once you've articulated your use case, you'll have a better sense of whether an OEM or aftermarket solution is best. When deciding between an OEM and an aftermarket teleremote control solution, several factors should be considered. OEM integration, such as that offered by Komatsu, typically offers seamless integration with the equipment, because it is specifically designed for the model in question. This ensures optimal performance, reliability, and easier support, often with warranties and manufacturer-backed service.
An aftermarket solution can range from a basic line-of-sight setup to a fully autonomous fleet and can be customized to your current equipment — any make or model. Oldenburg notes that RCT, SMS Equipment's partner in teleremote solutions for mining, says they have yet to come across a piece of equipment they couldn't work with. This machine-agnostic solution is more affordable, and specific options can be layered as your operation's needs change.
What's your timeline?
From initial conversations to deployment, the average implementation period for an aftermarket solution is between three and six months. "You can move pretty quickly because it's not an all-encompassing technology that affects your entire fleet," says Oldenburg. "It's very much on an asset-per-asset basis." With OEM, because the tech is already installed in the asset, integration is even faster.
Are your people ready?
Introducing any major technology to your organization often requires some change management. What is your team's experience, and comfort level, with new technology? How will it affect workflows and processes? What training and support will your people need?
What infrastructure is required?
The level of infrastructure required depends on the complexity of the solution. A line-of-sight installment on one loader requires less support than a more robust deployment, which may involve network or digital asset management systems.
Scaling up, out, and beyond
Oldenburg reports that, after the initial deployment, teleremote users are so happy they often find more opportunities for scaling the technology. For example, one mine automated its dozers to track pack. "They layered in an automation where several dozers are performing this task, going back and forth autonomously," Oldenburg explains. "When they're done, someone takes control, moves them to another location and sets them on their way."
It's this kind of agility that Oldenburg believes will drive teleremote innovation in the future. "I see it evolving on the automation side and bringing in advanced features, such as supervised autonomy." He also notes that interoperability — such as integration with an autonomous haulage ecosystem — is another feature being built out.
Teleremote technology can be a key integration to your mine on many fronts. From enhancing safety to increasing productivity to helping meet sustainability targets, your people, operations, and balance sheet all stand to benefit from this game-changing solution.