C&D specialist rolls two machines into one thanks to versatile Keestrack impact crusher
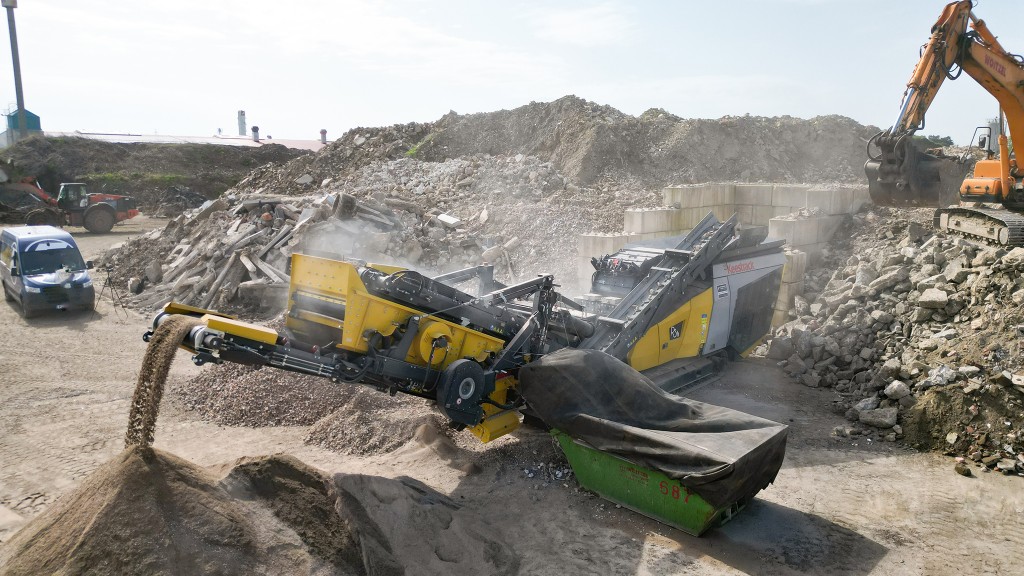
German company Manfred Woitzel GmbH & Co. started in 1956 as a quarry operation and today specializes in groundworks, demolition, recycling, and disposal services. One of the streams that the company handles is construction and demolition waste, which it processes on-site in its holding yard.
Today's third generation of the Woitzel family is always looking for ways to improve efficiency and profitability from all sectors, including C&D waste, and it has turned to Keestrack seeking out new solutions to improve the bottom line.
Previously, Woitzel has used two crushers - one jaw crusher at their holding and C&D recycling site, and an impact crusher that travelled between demolition sites. Woitzel has two Keestrack K4 screens and an S5 stacker; its familiarity with the brand and dealer Oppermann & Fuss drove interest in exploring new crushers.
Woitzel selected a Keestrack R3 impact crusher with double deck after screen and wind sifter. Fuel savings compared to the previous crushers were part of the decision-making process, said Jannik Woitzel.
"The two-deck after screen with return conveyor saves space, is easy to detach, and is easy to transport to demolition sites without a permit," he added. "This way the impactor is used both on the holding and recycling site, as well as the actual demolition site. The fully equipped machine is in fact two machines in one, saving a lot of cost in our operations."
At the holding and recycling site, Woitzel is producing RC-1 certified 0/8 mm and 8/45 mm used as crushing sand, and the bigger fraction is used as a stable base for such uses as road construction with high drainage capacities. The R3 runs up to six hours a day, producing about 160 tons per hour. When the S5 stacker is added to the production process, more savings can be realized thanks to reduced wheel loader use and personnel costs.
The R3 impact crusher has won a number of European design prizes, including the prestigious Red Dot award. It has unique safety features including a safety key system, and is compact for easy transport. It is also available in a full electric plug-in drive version, with capacity of up to 250 t/h.
A vibrating feeder has a prescreen of 1,200 x 920 mm to optimize crushing results and minimize wear. An asymmetric opening facilitates longer material turning into the 770 x 960 mm inlet. A high inertia rotor with a diameter of 1,100 mm and width of 920 mm produces high-quality end products with low wear.
The crusher is equipped in closed circuit with a recirculation conveyor and two-deck precision screen measuring 3,100 x 1,400 mm. It produces a defined aggregate product size. The installed wind sifter eliminates contaminants like plastics, wood, or paper, and an overband magnet separates valuable materials. Total weight of the R3, with all options included, is approximately 33 tonnes.
Remote control operation allows the excavator operator to run the R3 from their machine. An integrated water spray system reduces dust as necessary.
The Keestrack-er UMTS/GPS telematics system provides real-time data and analytics, and the exact location of the machine. All aspects can be checked from a distance and, if necessary, remote software updates can be made. Owners and dealers can take advantage of data from the system for planning maintenance. Diagnostic tests for all components including the feeder, crusher, after screen, and conveyors can be run through Keestrack-er.