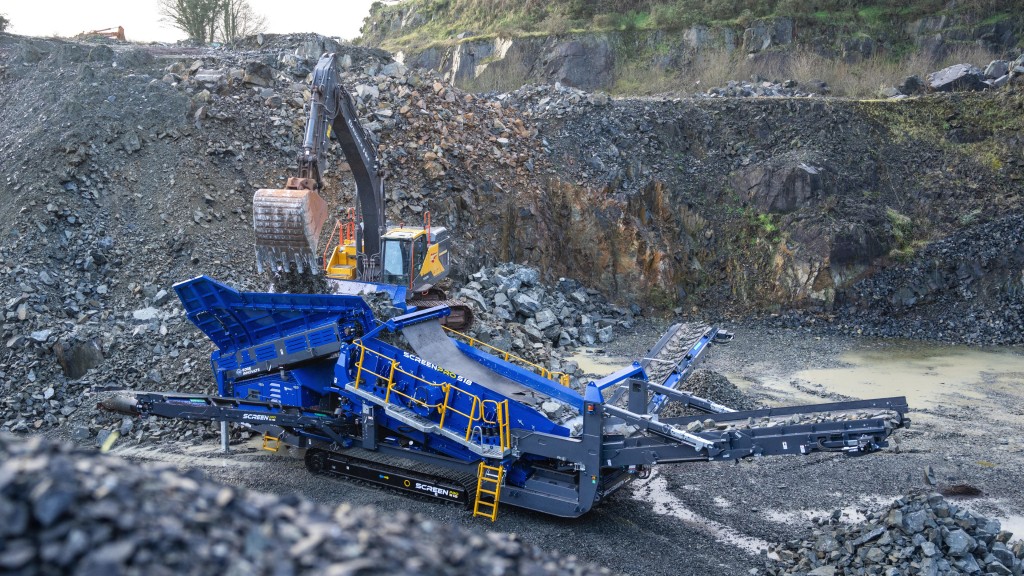
EDGE Innovate has expanded its product offering with the EDGE SCREENPRO S18 heavy-duty tracked scalping screen. EDGE says that the new screen delivers high production rates and precision screening.
The 18- by 6-foot (5.4- by 1.75-metre) two-deck screen features interchangeable flip flow and conventional scalper screens. The screen is designed to process aggregates, construction waste, sand and gravel, soils, and organic materials. With numerous screen media options and configurations available, the EDGE S18 can be utilized as a stand-alone unit or placed before or after a primary crusher.
The EDGE S18 utilizes a low-level feed hopper, two- or three-way split configuration, hydraulic folding discharge conveyors to facilitate the quick transition from operation to transport, and a fully integrated power unit with large service access. A user-friendly control system with sequential start/stop functionality provides exceptional operational performance and unit safety.
The EDGE SCREENPRO S18 utilizes a 1,400-millimetre (55-inch) wide, variable speed feeder with forward/reverse functionality. A large feed opening ensures an ideal flow of material to the scalping screen. EDGE's load management system monitors conveyor load pressures and regulates feeder speed resulting in ideal uptime and screening production by eliminating material overload. Hydraulic folding hopper extensions allow for side loading while a folding hopper rear door provides loading flexibility.
At the heart of the SCREENPRO S18 is an EDGE high-stroke scalping screen with a screening area of up to 18.3 cubic metres (21.7 square yards) and a wide variable working angle to suit an array of applications. The high stroke action results in material separation and a large screening area ensures precision fines separation. To ensure minimal downtime, the screenbox utilizes hydraulic lift-up functionality for a quick and efficient mesh exchange process, supported by full-access walkways on both sides of the screen.
Producers can choose from a wide range of screen media options including woven mesh, punch plate, finger screens, and grizzly decks to achieve a variety of final grain sizes and to process different feed materials.
Adding to the versatility of this new SCREENPRO range is its ability to interchange the scalping screen with EDGE Innovate's flip flow screen. This flexibility combined with numerous screen media options and configurations allows the EDGE SCREENPRO S18 to process a wide range of materials and to tackle screening applications that other conventional screens cannot, such as incinerator slag or wet, damp, and sticky material.
Thanks to an intuitive design, the plant is customizable both in the field and from the factory with side conveyors that can be reversed or discharged on the same side or converted to a two-way split without any additional parts required. The SCREENPRO S18 can be road transported in these setup modes.
The SCREENPRO S18 can also be equipped with both over-band magnets and magnetic head drums for the extraction and recovery of ferrous metals.
The oversize discharge conveyor features a heavy-duty 1600-millimetre (63-inch) chevron belt with a combination of impact bars and rollers that absorb the impact from loading material, prolonging the life of the conveyor belt. The oversize discharge conveyor can be lowered to five degrees to provide access to the lower screen deck and aid in the screen media exchange process.
The EDGE SCREENPRO S18 also offers added remote functionality for improved operator efficiency and safety. All major functions on the S18 including tracking, feed conveyor speed adjustment, sequential start, and hopper jacklegs can be remotely operated from a safe distance of up to 100 metres or in the comfort of the operator's cabin.
The new screen can be powered by either a Caterpillar or Cummins Tier 4 Final / Stage V ACERT engine. An electric hybrid option is also available, offering increased cost savings and environmental benefits. Utilizing a small onboard diesel engine for tracking and setup, operators can then connect to an external electricity supply once the machine is in position.
Company info
30 Farlough Road
Dungannon, Co. Tyrone,
IE, BT71 4DT
Website:
edgeinnovate.com
Phone number:
44 (0) 2887 747244