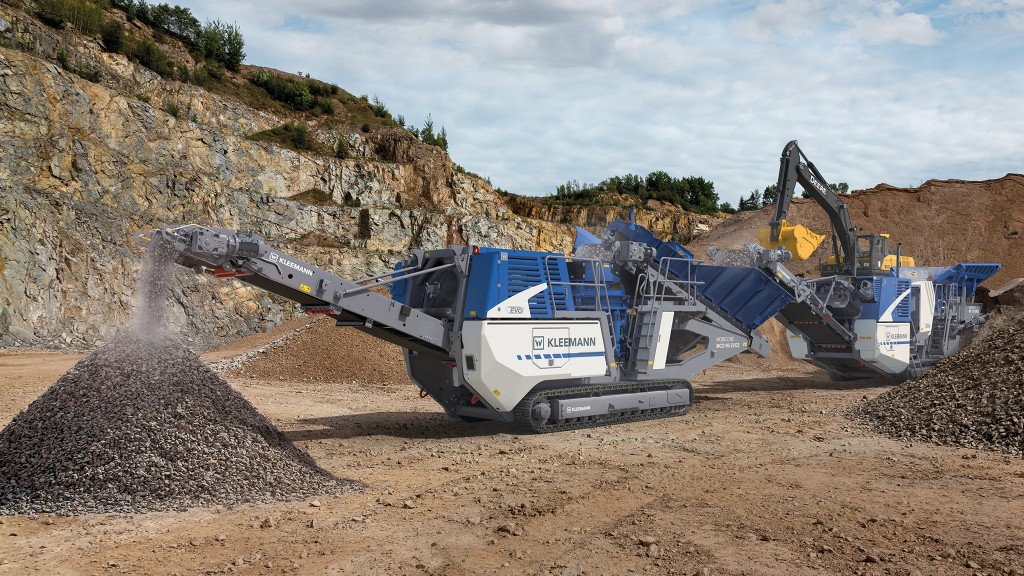
Kleemann made electric drive and advanced operating technologies central to recent new equipment releases, providing aggregates operations with added opportunities to improve their efficiency as well as shrinking their environmental footprint.
A selection of new crushers – including the first in a line of compact mobile machines with an electric power option – have been released recently, along with updates to operating systems and other technology improvements.
Electric drive and new compact crusher lines
Kleemann has increased the ability of owners to select their drive style on many new crushers, with electric, hybrid, and diesel all available.
A highlight of the new releases is the MOBIREX MR 100i NEO/NEOe mobile impact crusher, which Kleemann says is the first model in a new compact machine line. Using Kleemann's E-DRIVE concept, the MR 100i NEOe is available with all-electric operation, making it free of CO2 emissions.
E-DRIVE requires a power supply on the site, but when plugged in it has no local carbon footprint. If the machine is operating outside a location with appropriate power infrastructure, a low-consumption diesel engine can take over. The MR 100i NEO is equipped with the diesel-direct drive system as standard.
A four-ledged rotor with large impact range and versatile rotor ledge options produce high product quality. The MR 100i NEO and NEOe have an optional single-deck secondary screening unit.
Electric power is also available on the MOBIREX MR 130i PRO mobile impact crusher. Suited for primary or secondary crushing, the machine features efficient prescreening, an electric 335-hp drive, and an output of up to 661 tph. It only uses hydraulic oil for set-up functions, which reduces environmental risk and maintenance costs. When running on a diesel generator, a power- and load-dependent fan reduces noise and fuel consumption.
Two plants introduced at CONEXPO 2023 expanded Kleemann's EVO2 line of plants, one fitted with a jaw crusher and one with a cone. The MOBICAT MC 110i EVO2 jaw crusher and MCO 90i EVO2 cone crusher both feature Kleemann's D-Drive diesel-direct electric drive. An easily accessible gearbox is robust and resistant to dust, and an output-dependent fan drive reduces noise. Secondary drives, such as for prescreen, vibrating chutes, and conveyor belts, are driven electrically.
An innovative overload system protects both crushers, and the Continuous Feed System (CFS) optimizes crusher feed flows.
Kleemann also added a new screen to its line at CONEXPO. The MOBISCREEN MSS 802i EVO mobile screen is designed for challenging applications with flexible conversion options to optimize material flow. A range of screen surfaces and easy selection of screen parameters make it possible to adapt the plant for any particular feed material, depending on the required final product.
The MSS 802i EVO is fitted with the H-Drive system, which uses hydraulic pumps to run screens, belts, and the drive system. Power consumption using this system is lower, and an available start-stop system recognizes when gaps in the feed material are present and responds by slowing engine speed, along with the speed of the hydraulic drives. The screen can be run electrically if there is a power connection available.
Optimized flow through wireless links
Connecting multiple Kleemann plants in a train is easier thanks to the Continuous Feed System and wireless line coupling.
A wireless version of Kleemann's safety coupling system allows for fine-tuning of material flow from one end of the train to the other. CFS tracks the way that material is flowing through linked crushers and screens, monitoring the fill level of crushing chambers and adjusting feed flow as needed. This ensures that material moves at an efficient and productive rate.
The link is easier to establish, compared to complex cable routings, and also improves safety – if an emergency stop button is pressed on one machine, all the units in the train respond. This system reduces the likelihood of overloads and potential damage.
Intuitive controls and easier plant operation
Updates to control technology are making Kleemann crushing plants easier to operate, especially through the SPECTIVE system.
SPECTIVE provides control of machines through intuitive touch panels that feature clear instructions and pictographs which make it easier for users to set their machines quickly and precisely, ensuring safer and more efficient operation.
In addition, SPECTIVE can be operated through the new CONNECT feature, which extends control systems to smartphones. Users can view relevant process information including speed, consumption, productivity, and fill levels, along with important reports and fault codes. This allows operators to continue working in the wheel loader or excavator while viewing important data from the plant.
The mobile app also offers access to the Smart Job Configurator, which aids operators in finding correct machine settings. The user enters data for the planned application into SPECTIVE CONNECT, which then automatically calculates the ideal settings. These can then be transferred to the machine via the SPECTIVE touch panel. The Configurator helps select the correct crushing tools and tracks service requirements, simplifying actions for the operator.
Company info
6030 Dana Way
Antioch, TN
US, 37013
Website:
wirtgen-group.com/america/en-us/products/kleemann
Phone number:
(615) 501-0600