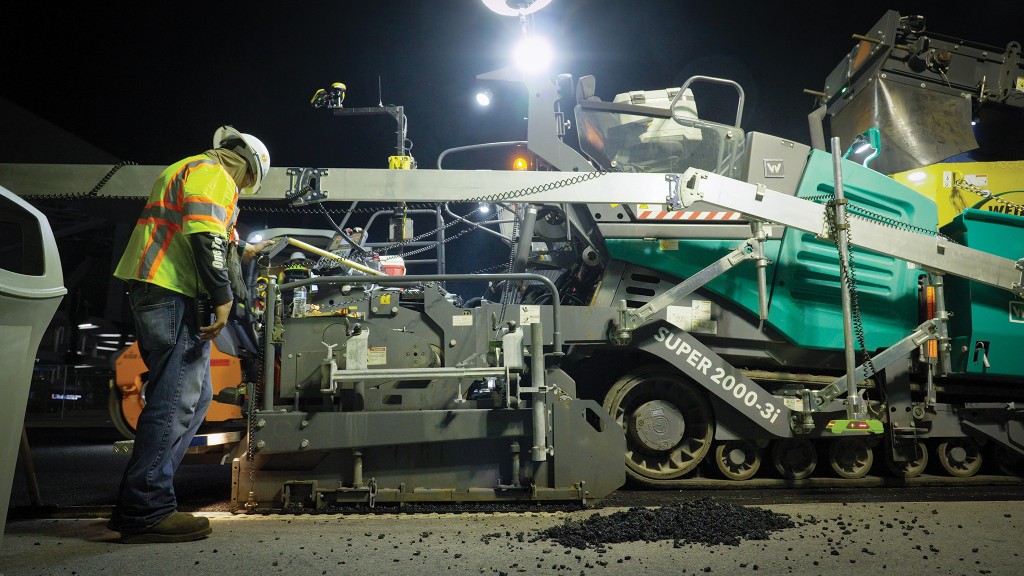
When paving, the last point of contact between the paver and the final product is the screed. To do the job properly, the screed needs to place mix at the right thickness, on the right slope, and with the right surface texture.
Most screeds on the market for smaller commercial projects, like parking lots, road repairs, and driveways, are similar in design and function. You have several decisions to make when choosing a new screed to ensure that the final product meets the needed specifications.
Front or rear mount depends on the job requirements
Mount style is a key choice when selecting a new screed. There is no right or wrong answer to whether a screed should be front- or rear-mounted because it all comes down to the needs of the job, says Brodie Hutchins, vice president, dealer development with Wirtgen America.
On a front-mount screed, the extensions are placed ahead of the main screed, which allows for easier hydraulic retraction and reduces the likelihood of material being caught in moving parts.
"A front-mounted screed has a much smaller pile height so that if you're coming up on a mailbox or a fire hydrant or some other obstacle, it's much easier to pull it in because the volume of material in front of the extension is lower," says Hutchins. "If you back up to do a driveway, you hit the button and the mix goes all the way out, then at the end, you pull it in, you won't have that big pile on each side from the rear-mounted extensions."
Rear mounts are often better for larger contracts such as roads and parking lots, where the extensions are not being moved as frequently and there are fewer obstacles to avoid. There is a smooth, natural flow of material from the paver to the screed, allowing for easy placement. Rear-mount units are also a larger structure, providing more weight and compaction.
In addition, rear mounts almost always feature the same depth of plate on both the main screed and extensions, making it easier to ensure a consistent texture across the mat. Hutchins explains that front-mounted extensions are not as deep as the rear-mounted extensions or the main screed, requiring additional angle adjustments.
Whether front or rear mount, almost every screed on the market today is variable width. Fixed-width screeds, used most frequently in large highway and road jobs, represent only a small percentage of machines in use. The trend for pavers has been toward versatility, and variable-width screeds play into that demand, Hutchins notes.
Vibration or compaction options for commercial screeds
Asphalt screeds take material coming through the paver's augers from the hopper, spread it out, and smooth it down using heated screed plates and the machine's weight. They also add slope and contour where needed and prepare the mat for compaction by rollers following the paver.
Vibration is the most common way to smooth down the asphalt mix, though some commercial pavers are available with compaction tools as well. Smaller units are generally fitted with vibratory systems that use an eccentric on the main screed and extensions. This shakes the plates enough to help spread the material and leave a smoother surface behind the paver.
You can also consider screeds equipped with tampers if you need a little more compaction from the paver.
"We sell several models with a tamper screed – it has a tamper bar in front of the screed plate that compacts the material and then smooths it, versus just smoothing it and getting on to it with the roller to do all the compaction," Hutchins says.
The tamper strikes the surface of the asphalt, pushing the material down, then the screed passes over the material with its usual vibration to leave the needed texture and allow easier final compaction.
Technology options and automation expand on screeds
As technology matures in the roadbuilding sector, more new features are becoming available for screeds. Advanced 3D control systems and a range of automation tools to help you do your jobs more smoothly.
Screeds have moved away from old-style controls like toggles and switches to new, easy-to-read operator panels that are popular with new users. Touchscreens make it easier to program grade and slope and are central to automating many parts of modern screeds.
"There is more exploration into the use of true three-dimensional set-ups where contractors can equip the machine to not only steer but also set the depth you're paving and the slope," Hutchins says. "From a practical standpoint, we're trying to automate more of the functions on these machines to prevent operators from making so many adjustments on the fly."
Telematics is growing in use on pavers and screeds. Hutchins said there is a demand for data among paving contractors, and today's machines feature communication between the plant, trucks, paver, and rollers to track all aspects of a project.
"It's really a dialed-in process where contractors know the exact tonnage in a day, how many trucks they need, how far the trucks are from the paver, and other factors so they can theoretically calculate how fast they should be paving all day long," Hutchins explains.
Know your crew for successful screed selection
While you may be able to track all the hardware variables when it comes to selecting the right screed for your work, there is one final factor to keep in mind: the crew.
Paving equipment requires a good team to operate, and successful paving requires the crew to know the equipment well. It is important to know what type of screed your team prefers for the best results, Hutchins says.
"Crews have very strong opinions on what tools they want to use for the job. If a crew is used to working with rear-mounted screeds – don't give them a front-mounted screed," he advises. "They want what they're used to. It's like they're artists – they're painting a picture, and they want to do it their way."
Company info
6030 Dana Way
Antioch, TN
US, 37013
Website:
wirtgen-group.com/en-us
Phone number:
615-501-0600