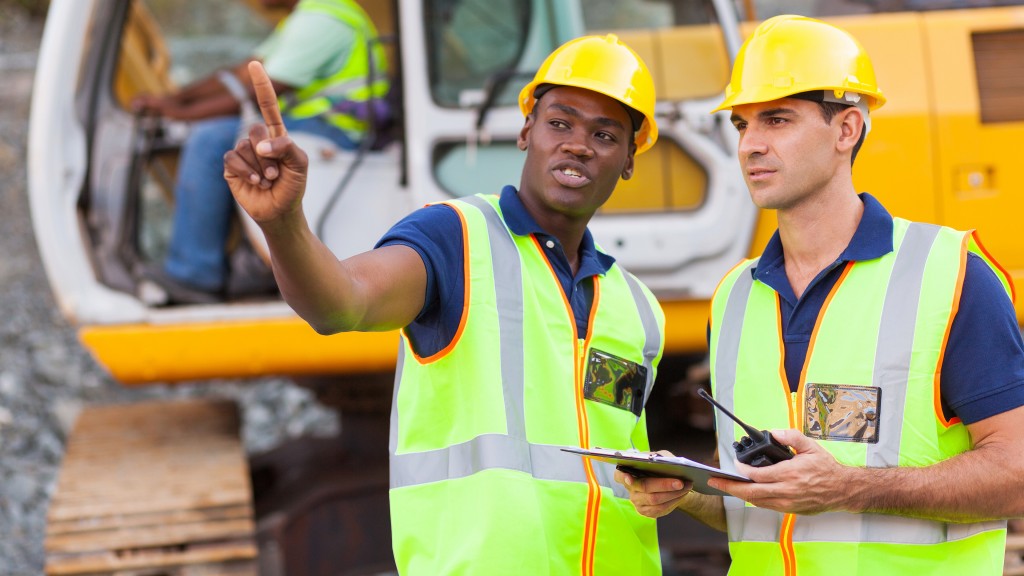
It's no secret to anyone working in equipment manufacturing that the ever-growing technician shortage is a problem poised to get a lot worse before it gets better.
According to a 2020 AED Foundation industry research report, our industry may need to fill as many as 73,500 heavy equipment technician positions by 2025. In addition, the report stated equipment manufacturing possesses a job opening rate three times higher than the national average. Among survey respondents, 95 percent agreed with the assertion there was a skills gap in the industry, while 89 percent reported a shortage of workers within the walls of their respective companies.
Now, I don't want to suggest the widespread technician shortage can be quickly addressed, let alone easily solved. However, equipment manufacturers can (and should) embrace and adopt a number of short-term and long-term strategies to set themselves up for sustained success as it relates to workforce development.
Focus on retention
So many pieces of the technician workforce puzzle can only be lightly influenced. However, one area companies can focus efforts to drive positive change as it relates to retention is workplace culture. Start by asking the following two questions:
- Are exit interviews being conducted? – Technicians leaving an organization within the first six months could indicate an onboarding problem, while technicians leaving between 2.5 and 3.5 years could indicate a lack of development opportunities. With exit interviews, it's worthwhile to have both a manager and human resources representative conduct interviews separately, as each position is likely to elicit different responses from departing employees.
- Are staying interviews being conducted? – Talking with staff in key positions about their individual experiences can shed light on missed opportunities or future red flags. Engaging in staying interviews can be particularly helpful in the first 12 months to understand what it's like to be onboarded and how new employees experience the existing culture within the organization. Start by creating a culture check-in by surveying all employees. What changes can be made based off all the information learned? And remember, to those companies who aren't currently acting on employee feedback being received, asking for additional input can (and likely will) negatively impact culture moving forward.
Fill the talent pipeline
There's really no overstating the importance of finding ways to fill an organizational talent pipeline. And while it takes time to secure a return on investments of time, effort, and resources to do so, it's worth it to take proactive steps to ensure desired results.
Simply contacting the nearest local technical college once or twice a year isn't going to be enough to attract and acquire talent. Regularly engage with educational institutions. Be part of review committees. Get in front of students in classrooms. Donate equipment. More than anything else, do what it takes to be top of mind when these schools begin looking to place their best students. It will pay dividends over time.
In addition, it's important to connect with high schools feeding into technical college programs. One effective way to do so is to introduce the high schools to a free, available, high school technician curriculum offered through Curriculum for Ag Science Education. It's not just an ag technician curriculum, but rather a program which introduces the technician career to a wide audience and enhances industry perception to parents, teachers, and students. As a bonus, there is a built-in industry connection opportunity through the collection of used parts and by offering several class visits.
Organizations must be willing to shed light on the significant industry demand for qualified workers and worthwhile career opportunities because chances are they aren't aware of the extent of the existing technician shortage. Technician program partnerships, apprenticeships, job shadowing, or any other work-and-learn program are the most effective way to connect with new workers. And, ultimately, partnering with education is critical for retention, as technicians require ongoing training and development.
Diversify and optimize recruitment strategies
Want to really move the needle when it comes to acquiring talent? Do the following:
- Actively recruit women and minorities.
- Change the way job postings are written and where they are being posted.
- Check language in job postings via a gender decoder website to determine if it's overly masculine.
- Target locations and events where someone with the skills, interests, and hobbies of workers the organization wants to replicate might be out and see if the openings can be posted.
- Learn more by reading Equipment World's 27 Ways to Attract and Retain Equipment Technician Talent and Chris Czarnik's Winning the War for Talent.
Collaborate with others
Because the technician shortage is one of our industry's biggest issues, AEM's Workforce Development Committee has created a technician taskforce. We'll be sharing examples of survey questions, stay interview questions and other practices being used by industry members to help move the needle in this space.
AEM is also partnering with, and supporting the work of, the AED Foundation. If you're not aware of the AED Foundation's work to accredit 100 colleges and recognize 150 high schools in heavy equipment technology programs, you can learn more about its Vision 2025 by visiting the AED Foundation website.
When it comes to understanding the work being done to support the industry's needs in this space, there are many associations that are trying to collaborate rather than duplicate efforts. Just as there's no one thing that a company can do to help ease the technician shortage, there's no one associate that can solve the challenge on their own.