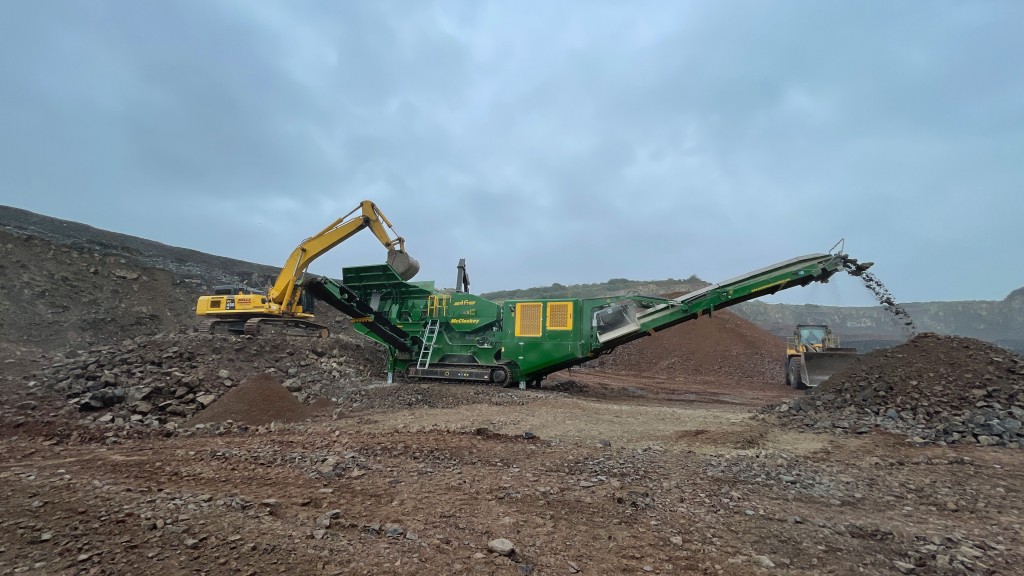
McCloskey International will unveil the new J6 as the latest entry into McCloskey's jaw crusher line. Exclusive to the North American market, the J6 builds on the features of the existing product range, with features aimed at boosting productivity and offering enhanced durability across applications.
The J6 delivers high production due to its jaw chamber design and enhanced material flow. The large chamber has proven to be particularly effective in hard rock applications, with an optional factory-fit rock hammer available to maximize resources on site. The large 48" x 34" (1204mm x 864mm) jaw opening accommodates large feed sizes, also contributing to higher production in material processing.
The material path is enhanced with a 47.4" x 7' to 8.8" (1204mm x 2360mm) double-deck grizzly prescreen under the hopper that, along with the variable speed pan feeder, allows for better sizing of material with a variety of media options.
McCloskey engineers have designed the J6 to meet the requirements of today's projects and operations. Portability has not been compromised on the J6. Mobility on-site and between sites continues to be a feature with remote control tracks to easily move and position the crusher and maximize the efficiency of any project site. Also contributing to efficiency, particularly in remote locations, is the high volume fuel tank, sufficient to run the J6 for approximately 20 hours.
The J6 delivers ideal stockpiling, with wide main and side conveyors for enhanced material flow. The angle-adjustable 55" (1400mm) wide main conveyor has a 16'-9.8" (5.13m) high stockpile. With a quick release and ground-level access, the belt is easy to maintain and service. While a side conveyor remains an option for many jaw crushers in its class, the J6's integral folding conveyor is standard and has a 32" (800mm) adjustable speed belt fueling a stockpile height of 3.99m.
Technology has been a key factor in the development of the J6, with a 12" DSE control panel for performance and reliability, providing a push-button control of the jaw, track, and feeder functions. The crusher is fitted with a telematics modem for the new 365SiteConnex program, a connectivity solution for monitoring of McCloskey products.
The J6 is equipped with a number of features to ensure the workplace and the operator are safe and secure. Engine safety shutdown systems, start-up alarms, full safety guarding, external maintenance access, and tagout capability on the isolator, all contribute to the safe operation and maintenance of the equipment. Ground level access also promotes safety, and allows for quick service and maintenance, reducing the downtime for the operation.
"The J6 is an exciting addition to our jaw crushing product range, as we continue to develop products that meet the unique requirements of fleets in diverse conditions around the world," said Toni Laaksonen, senior vice president at McCloskey International. "We design and evolve our equipment to enhance the operations, efficiency, and productivity of customers, ensuring success in the field and in their results. The J6 is a perfect example of leveraging the best features from our existing jaw crushers, and adding functions and features based on how our customers use the equipment every day. "
The J6 jaw crusher will be shown to the North American market at World of Asphalt/AGG1.