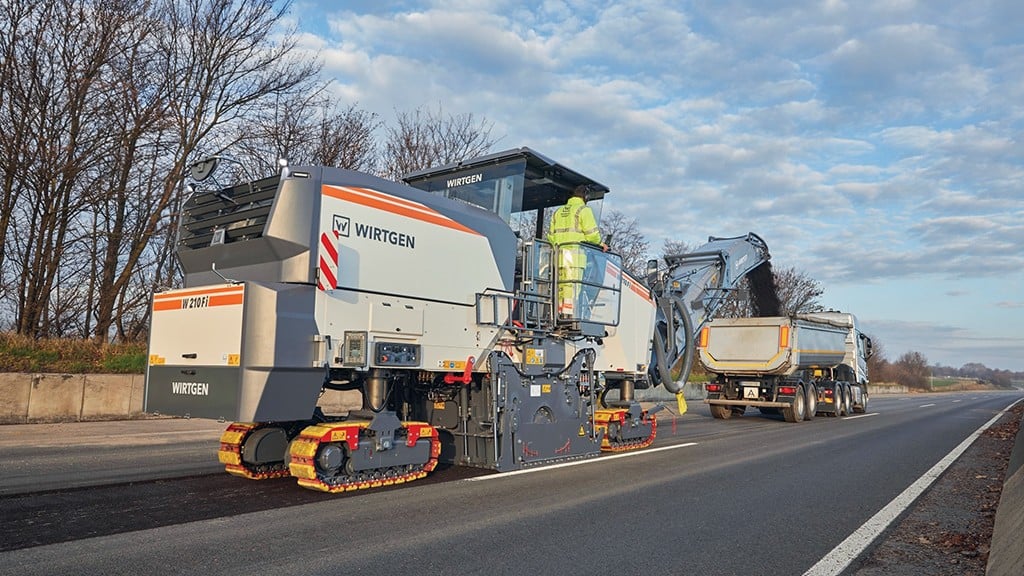
Asphalt milling has become an integral way in which roadway owners can extend the lives of their infrastructure. Stripping worn surfaces and replacing with freshly laid asphalt keeps motorists moving on smooth roads, and saves money in the long run.
For contractors, learning how to best use a milling machine is key to successful completion of paving jobs. Tom Chastain, milling product manager with Wirtgen America, offers a collection of tips and techniques that can bring more to milling machines and ensure good quality surfaces for paving.
How do milling machines help with good paving?
Milling machines, Chastain said, are intended to provide the preparation for paving crews to place their best work - the better the milling operation, the better the final results.
"Our job as a milling crew is to give the paving crew a clean canvas to paint a masterpiece on," he described. "If we mill properly, it gives the paving crew a greater likelihood of paving it correctly."
Communication a good starting point
A key starting point for good milling machine operations involves good communication. Milling teams need to know the job, the challenges, things to watch for and other aspects of the job - but they aren't the only ones who need to know what's happening.
"Obviously, we have 100 percent of the information at the office, and that trickles down to the supervisor or foreman, and then down to the milling crew. But it doesn't stop there - we have to talk to the dump truck driver, for example, and inform them how we're going to approach the job so we can do it in a safe and efficient manner," Chastain said.
Production the key for asphalt milling machine choice
Milling crews keep three words in mind when they're going to work, according to Chastain: production, production and production.
"Production is how milling crews are typically geared. The worst thing you can say to a milling crew is ‘we have asphalt on the way' - you've just lit a very quick fuse," he said. "That really sends things into overdrive."
To be sure that production is maximized, crews need to have the right milling machine for the job. Chastain said that for smaller jobs, like curb reveals, joint replacement or cutting around manholes, small machines are best suited. Larger patch work may call for a compact or mid-sized machine, while full replacement work means it's time to bring in the big boys. Understanding the job size and requirements makes it easier to match milling machines to the work needed.
Maintaining cutting teeth key to good operation
Milling machines are designed to do one thing: tear up the surface they run across. In the process, they also take a beating themselves, so it's very important to be sure that maintenance is done constantly and correctly.
"If you're in a mill and fill situation and haven't done the maintenance on your machine and it breaks down, then everything else goes down as well - it's a domino effect," Chastain said. "What we've done with the newer machines is made it much simpler to do that maintenance, to get to the fuel filters and air filters, as well as access everything else important.
Keep cutter drum and teeth optimum
Key to the milling machine's operation is the cutter drum and the teeth on it. "As a manufacturer, we could put two jet engines on a milling machine, but if the cutter drum is not in optimum working order it doesn't matter - it's not going to produce the quality or quantity we need," Chastain described.
It's important to review the status of the milling teeth and holders, which are wear parts and need to be replaced.
"Every time the cutting tool hits asphalt, it generates upward of 1,800 degrees F - that's hot! When you take that along with the abrasiveness of the material and heat and that's where you get carbide wear - it starts to break down that carbide tip," Chastain advised.
When teeth start to wear, operators may notice white streaks on the surface behind the machine, an indication that they need to be replaced. If that's ignored too long then the tool can be ground away and the holder starts to engage the surface material. Without a cutting edge, it bludgeons the asphalt and leaves scuff marks on the surface. Chastain described this as trying to cut a surface with an ice cream tasting spoon. At that point, both bit and holder need to be replaced - if not, the worn holder will leave the tooth at a different angle of attack compared to the rest of the tools on the drum.
Keep old teeth handy for emergency replacement
One tip Chastain suggested is that if machines are switching from job to job and the milling head has a full new set of teeth installed, keep the old teeth on hand if they aren't worn too far down. That way if a tooth breaks on the new job, one of the used teeth can be installed, matching up better with the rest than a brand-new one that will cut deeper than the rest.
It's also important to check over the water spray system and ensure spray nozzles are in good condition, keep the drum coolant level at manufacturers' specs, and be sure to have spare teeth and holders - saving someone an emergency run back to the shop if there's a problem on site. Maintain the kicker panels, which aid in removing pavement material coming from the cutting teeth and eject it onto the conveyor belt, as well.
Control systems aid with efficiency on milling machines
There has been quite a lot of growth in the use of grade control systems on milling machines, whether they are ultrasonics, smart cylinders, laser or other approaches. Understanding how they work is a key to achieving good surfaces.
"Ask the question: are we copying the road or profiling it? When you copy the road, what you see is what you get - if you are referencing off the side plate sensors, yoyos or whatever, when you go over a bump it's going to just copy the road," Chastain noted. "Behind the paver it looks great, but when you compact it you're just right back to where you started."
Higher speeds may not smooth correctly
If the road is being copied at a higher rate of speed, some bumps may not be removed, and in fact more might wind up being added. Profiling can be a better approach, taking any bumps on the road and averaging them out through the use of grade control sensors.
Using a 3D scan of the road is also helpful, in that it allows crews on mills to see the true profile of their target levels and how to deal with some problem spots in pavement.
Slow down for smoother cuts
The best milled surfaces are developed from slower speeds, Chastain noted, but production in feet per minute should be balanced based on the end result and the size of pavement material desired from any particular cut.
"The slower the machine's forward motion is, the more hits those teeth are going to make, and the smaller the material," he advised. "Milling faster doesn't change the line spacing, it changes the quality of the pattern being left behind. When there's a bigger swipe being taken, the pattern is more coarse."
Even for production-minded milling crews with high-horsepower machines, higher speeds are not the best. "At those kinds of speeds you're just excavating material, not milling - you may have to add a crushing and screening aspect to the whole process," he said.
Slower starts mill pavement more evenly
Be sure to start slower, as well - when the machine engages in the cut and begins to move, give the tracks some time to get in and the hydraulics enough time to react. Starting out too quickly can cause the machine's cutting head to drop too hard and potentially leave a brand-new dip in the road.
All in all, Chastain said, the keys to good milling come down to a few key points.
"If we maintain our machine, we have bettered our chance to achieve quality. If we slow our feet per minute down, we have bettered our chance to achieve quality. If we communicate with our team regarding the job, we have bettered our chances to achieve quality," he said. "If we do all of these things while putting safety first, we will achieve quality."
Company info
6030 Dana Way
Antioch, TN
US, 37013
Website:
wirtgen-group.com/en-us
Phone number:
615-501-0600