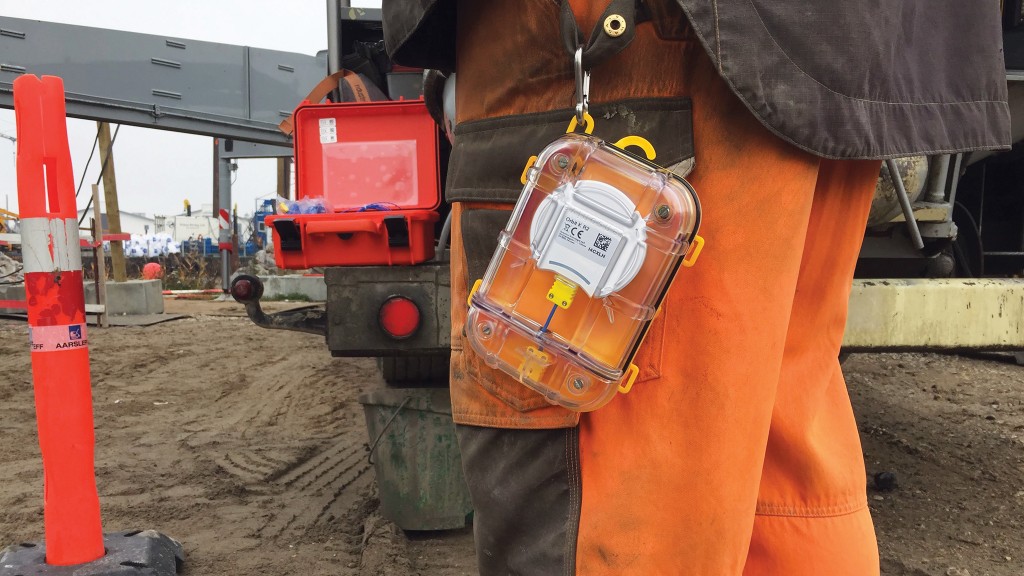
Concrete is finicky - anyone who works in the industry can tell you that. It might seem simple - combine aggregate, cement and water in proper quantities and pour - but for large construction projects the variations that are needed for different uses need to be tracked precisely. Material needs to be mixed just right and monitored from the plant to the jobsite, poured in the right conditions, and then monitored for hardness and curing as it dries before further work can be done. There are plenty of steps where something can go wrong and require significant expense, as well as time, to fix.
Like the rest of the construction industry, technology is starting to play a greater part in improving efficiency for concrete contractors. On the plant side of the equation, monitoring and tracking of concrete mix, condition and delivery is the key focus, while monitoring after the pour has taken several different approaches.
Ready-mix plants have been taking advantage of various technologies for longer than the contracting side of the industry, with computers handling tasks like dispatching and purchase orders in the office, related Jeff Hunter, vice president with Command Alkon.
"Technology started in the industry through mandates of government . . . as things have progressed, producers have come to realize that there are efficiency gains that technology can provide," Hunter said.
A retired Command Alkon vice president, Jim Wagner, started developing dispatching processes using technology, kicking off a push for more opportunity to add efficiency. Automated batching plants came along next, adding precision and reducing standard deviations in concrete loads, and that was followed by GPS tracking of trucks to help improve scheduling.
Tracking concrete from plant to pour
Today, much of Command Alkon's work is going into understanding what is happening with the concrete itself - which can be a challenge for a product that is handled by so many people between leaving the plant and being used on the jobsite.
"You have an expensive plant and production process where you had a good control of what was produced, and then you put it into a truck. You have 50 trucks, and you would have 50 drivers making adjustments to the concrete. Then you had however many customers out there, again, making adjustments," Wagner said. "There's not any other product that I can think of where the finished product, from the time it's produced at a batch plant, through the time that it's placed and hardened, has so many different people with their hands in it."
For Command Alkon, the route to tracking concrete quality through that trip from plant to pour takes advantage of sensors installed onto delivery trucks. The company's COMMANDassurance system is designed to ensure that stakeholders know how the concrete is being handled in that time frame.
"It uses exception-based reporting and notifications to notify quality control people, dispatch managers and plant operators on how the concrete is performing in terms of slump and temperature, how it's being manipulated in terms of revolutions and mixing, and accounting for the water that can be added to make sure the water-cement ratio is maintained within specifications," Wagner explained.
Key to the COMMANDassurance system is direct measurement; a probe is installed in the access hatch of the mixer drum to ensure that it's in direct contact with the concrete. The system is solar powered and connects via Bluetooth to a display on the back of the truck, as well as the GPS tracking system, where operators can review the condition. With the data being collected, batch plant operators can be more precise about the mix prior to it leaving the plant, reducing the time and effort needed at the jobsite, and other variables such as drum rpm, temperatures and more are tracked more efficiently.
Shaving time off curing processes saves money
With these kinds of approaches to managing concrete before delivery, contractors can be assured that they are getting the right concrete mix at the right time. From there, though, the question has always been: is it strong enough, and when is it ready to continue building?
Testing processes have frequently used cylinders of concrete poured from the batch and taken to a lab, where samples of cured concrete are crushed to determine the strength of the final product. Only once they have achieved the proper strength can construction continue.
"Strength needs to be validated in concrete somehow . . . people, as they pour concrete, cast field-cured cylinders - they take samples and put them in a cooler. That way there's a relationship to the concrete that's been placed versus the samples that are on the project," explained Kris Till, technical sales manager with Kryton. "From there, they send off the sample, the sample gets crushed, and that indicates the strength. They wait for the samples to come back with the achieved targets, and that gives them the thumbs-up to move forward."
The issue with that system is that the cylinders don't necessarily cure at the same rate as concrete poured in larger volumes, Till noted. Large concrete pours have a heat profile that affects curing and strength, a condition that isn't necessarily replicated in the smaller samples.
"They're very small samples . . . therefore they usually always lag behind the concrete. So, right there, that's a huge disconnect because you can wait for a field-cured cylinder to validate your concrete for days after the concrete is at strength," he said. "That's where the biggest productivity gains come from - knowing exactly when your concrete has actually achieved its strength development."
A technology popularized in Europe has begun to make its way into the North American market, using sensors embedded into the concrete itself to track the maturity of the material more closely and allow for faster results. Kryton's version, Maturix, allows for real-time monitoring of the concrete curing process.
"This non-destructive testing method has been around since the 1950s, but it requires very complicated calculations. As technology has evolved, now these platforms and sensors are able to do these calculations using live data," Till said.
The Kryton approach uses a thermocouple embedded into the concrete that is attached to a reusable sensor, which can transmit real-time data into the cloud.
"We take a very economical piece of equipment, a thermocouple of wire, and fix it to the reinforcing steel, then run it outside and plug it into the transmitting sensor - only the thermocouple is consumed in the concrete," Till explained. "Everything we do is through a wireless network - we're communicating this temperature in real time to a cloud-based platform. It does this fairly complicated calculation to convert it to maturity, and from maturity you can understand strength development of the concrete."
Consumable sensors connect wirelessly
A similar approach has been taken by another recent entry to the concrete technology sector. Hilti, already known for its many concrete tools, introduced its own sensor system in mid-2020 after acquiring Concrete Sensors earlier in the year.
A fully wireless system, the Hilti solution uses consumable sensors that pair with mobile devices through an app and provide quick snapshots of concrete conditions. Brendan Dowdall, concrete sensors director, explained that there are a number of aspects to the solution.
"There's hardware - the sensor - and then there's software, an app that connects to the sensor and the way in which you gain more value from the solution," he explained. "There's a service - we have a concrete lab where we test actual concrete mix designs for temperature sensitivity and how it will perform in the field. We know concrete cures faster when it's warm and slower when it's cold, but how much faster or slower is what we get from the lab? We get a rich data source that gets fed back into the app, along with the data from the sensor that will tell you the real-time strength of the concrete."
Installing the Hilti sensors is simple; each one has a QR code that can be read by the app using a mobile device, and once it's registered the palm-sized sensor is attached to rebar or another anchor where it will be buried within the concrete. The app allows for naming of sensors and identification of precise locations, and once it's in place the sensor begins to send data in, which is then processed and made available to users.
"It's going to tell them the current strength of the concrete, current temperature, temperature over time and the relative humidity in your concrete," said Scott Rutledge, Hilti business unit manager, anchors. "If you're measuring the difference between interior and exterior temperature on a large mass concrete pour, it will give you that temperature differential as well. We wanted to make it super simple for the customer, so realistically within a day of when they've poured the concrete they'll have their first readings and it will tell them exactly what the condition of their concrete is."
The end goal of collecting real-time data on concrete maturity is time savings - the sooner that a pour reaches maturity, the faster the job can carry on.
"Understanding strength in real time is a missing piece of the construction puzzle - we're allowing contractors to strip forms and load concrete and do things a lot more efficiently, saving significant time," Till described. "They can save up to 20 percent on time, easily, on a project."
Reducing the time spent on the curing phase of a particular project adds up quickly, Rutledge noted.
"It doesn't sound like a big deal, but you're going to get the information to make a decision four or eight hours sooner than you were before. You wouldn't think, on a two-year project, that makes a huge difference, but it really does. They say ‘if I can make that decision four days faster . . . maybe I can do four-day pour schedules instead of five-day pour schedules, and that allows me on a 27-story building to get done 27 days sooner,'" Rutledge said. "They can save hundreds of thousands of dollars by having that jobsite finished a month earlier."
Company info
1800 International Park Drive Suite 400
Birmingham, AL
US, 35243
Website:
commandalkon.com