Five ways to stay ahead of your HDD rig maintenance
Save time and money with daily inspections and other preventive maintenance
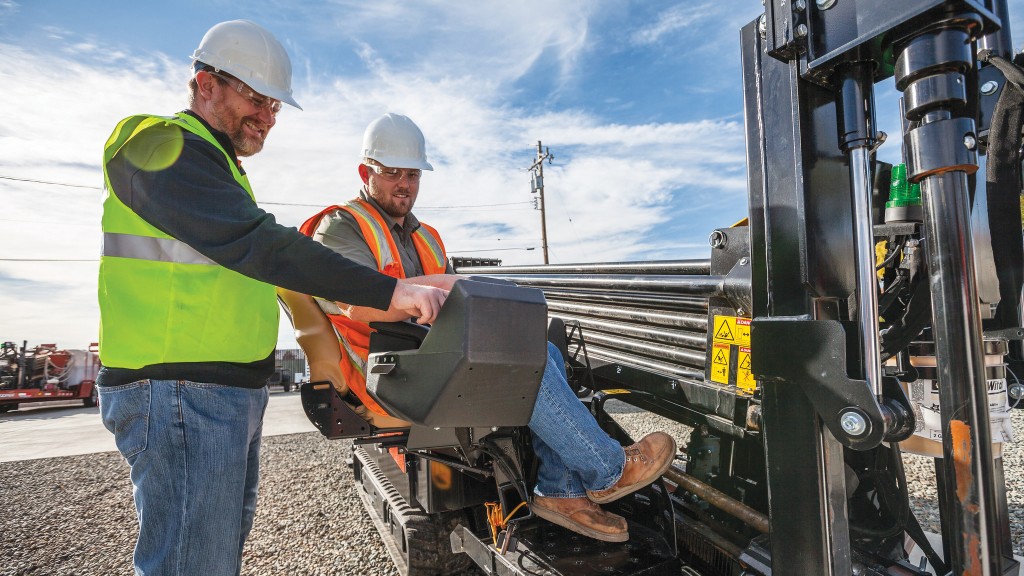
You know that getting the job done quickly and efficiently is the name of the game for your HDD crews. So when time is of the essence, conducting daily preventive equipment inspections may seem like downtime. But industry veterans know that basic care and maintenance routines are instrumental in preventing actual, costly downtime.
Preventive care and maintenance are what keep machines functioning at a high level and are the best ways to keep an operation efficient. It's also easier than you may think. Companies like Ditch Witch design machines with operator simplicity in mind. Machines are prepackaged with easy-to-understand manuals, intuitively located service points and proper equipment guidelines, positioning contractors for success.
Here are five preventive maintenance best practices that will keep your machines running smoothly for the long haul.
1. Utilize your daily checklist
The most important step in preventive maintenance is also the easiest – follow the user manual. This document provides the necessary information to keep your equipment safe, productive and efficient. Within the manual, you can find recommended service intervals, one of which walks operators through daily maintenance routines like checking coolant, oils, mud pump, drilling fluid and Y-strainers. Taking the time to check these components will reveal any issues left over from the previous bore that might keep a machine from running properly. For example, drilling fluids and Y-strainers protect your machine's high-pressure mud circuit. If they are not inspected daily, sand, debris and other obstructions could cause the machine to break down and be out of commission for that day.
2. Stay ahead of the saver sub
As the equipment responsible for driving pipe downhole, the saver sub is one of the most essential pieces of a rotary system. One of the biggest maintenance fears with a saver sub is if the thread profile becomes damaged inside, this not only leaves the saver sub broken, but also wrecks the entire rack of pipe. A damaged saver sub can cause the entire drill to be inoperable until a replacement part is available.
Your crews should make sure to inspect their saver sub every day. And wise fleet managers will make sure that they're fully stocked with correct parts so that maintenance, when required, won't lead to long stretches of downtime.
3. Streamline maintenance with telematics
Modern telematics and centrally located site gauges can help you and your teams streamline the preventive maintenance process even more. For example, Ditch Witch's Orange Intel Fleet Management System is designed to alert contractors about any upcoming service intervals that are tied to the machine's user manual.
Telematics flag when machine components need to be inspected or serviced, whether it's at 10 hours or 2,000 hours. Spending five to 10 minutes a day conducting service checks will not only help you save time, money and costly damages from any overlooked maintenance problems, but also keep machines operating at their peak level on the jobsite.
4. Maintain your drill pipe
It's easy to view the cost of the rig as the overall cost of the unit, but the truth is that by the time a drill goes through its full life cycle, you've probably spent more money on replacing pipe. That is why maintaining proper lubrication and rotation of your drill pipe will not only help lengthen the life of your equipment but lead to its overall success.
Every manufacturer has their own standard of proper lubrication, which is designed to optimize thread compression and tolerance. Maintaining your automated greaser machines with the correct lubrication compound helps contractors achieve proper torque, reducing the chances of the pipe unthreading and breaking downhole.
5. Proper end-of-day care
At the end of every job, you should take time to clean each machine to eliminate any blocked jets or pumps, which can hinder the performance success of your drill. We know that time is money and time spent servicing your equipment is valuable. To streamline the cleaning process, manufacturers often design their machines with a high-pressure pump that gets plugged into the circuit system within the machine, allowing for an efficient way to wash down the machine. During the wash down, watch for any connections and hydraulics that might be leaking or flag a broken line. These could lead to costly contamination issues on your next jobsite and keep you down on the job if not identified ahead of time.
It can be hard to set aside time for what may seem to be tedious maintenance tasks, but just a few minutes each day can truly help overall operations at your jobsites. Through these daily checks, aftercare routines and keeping up with proper equipment standards, you can keep your machines in their best operating shape, saving time and money, and combatting downtime.
Cory Maker is HDD product manager at Ditch Witch.