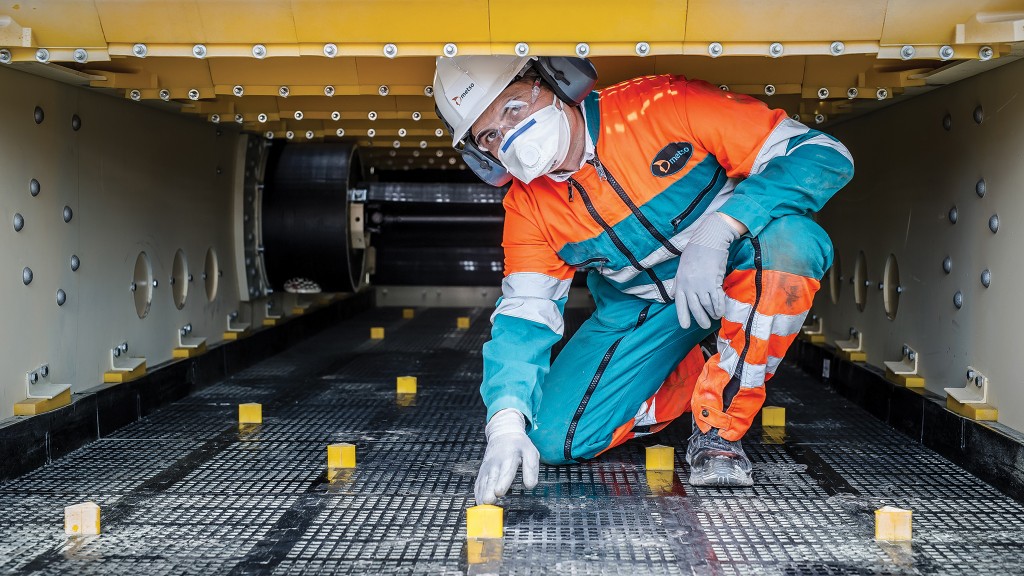
To maximize profit, aggregates producers need to ensure that the product they offer fits the needs of their customers, down to the size of the material they sell. Using the right equipment throughout the crushing and screening process is key to that goal.
One area that might not be as obvious to meeting that goal is the screening media that is used to sort those various end products. The fact is, though, that without that properly sized screen installed correctly and maintained well the final product may not pass inspection for the customer. Choosing the right screening media is essential for any crushing and screening operation.
Every aggregates producer has a different need when it comes to their screening needs, and the range of products to fit those needs is broad. It's important to understand the type of material that will pass over a screen to decide the best selection, according to experts from Metso Outotec.
Today's screen media comes in several variations, from the popular wire mesh through engineered solutions like rubber and polyurethane, explained Product Manager Claes Larsson.
"The more traditional type of screen media is the woven wire mesh, which is used throughout really any industry from aggregates to portable equipment, and then you also have something that is growing in the industry today, more flexible wires which are crimped in zig-zag to form openings, and bonded with polyurethane strips to keep them together," Larsson said.
Metso's Trellex PCL screen media, for example, uses treated and coated wire bonded to polyurethane strips to increase wear life and help reduce plugging issues that can increase maintenance needs. It, and similar wire cloth screens, is installed using tension hooks that connect the material to the sidewalls of the machine. A screening deck may use several different sizes of media to help in efficient material movement.
Molded polyurethane and rubber products are a step up from wire cloth, and useful for reducing some potential issues such as blinding, or clogging up of fine openings.
"If you have large rocks or bigger sizes, rubber mats could be preferred; if you're wet screening, the lifetime of wire mesh is kind of short, so that is where polyurethane can come in as well," Larsson said. "Rubber and polyurethane products come in different shapes, and as well there's a growing segment in the market for modular media where the material comes in a standardized size."
Injection molding of polyurethane and rubber modules has provided the ability to make much broader types and sizes of media for installation in a range of screens, and provides the ability to work with different OEM installation methods and maintenance needs.
Size of operation, type of material and other factors often influence the type of media that an aggregates business will select, noted Metso Engineering Manager Travis Schoultz.
"Some smaller suppliers need to be more money conscious, and the less expensive way to go is the woven wire type method, while larger operations might opt for the rubber or polyurethane solutions that are typically a little more expensive," Schoultz said. "The application itself can determine what media is best for the environment or use – sometimes you're looking for more open area and that may lead you to a wire woven solution. . . that helps the media stay clean. If the application is wet or sticky it may push them in that direction."
Wire and rubber are good in wet or sticky applications as the material moves energetically with the screen, allowing it to dislodge material that might begin to plug openings while allowing the desired product to fall through. Higher throughput operations might find polyurethane a better choice, while screening of abrasive materials can best be done with rubber media. Knowing what the best choice is can often come down to expertise.
"It's a good idea to get expert advice when you're selecting your media, as you go through a particular site or project – it's helpful to talk to someone with plenty of knowledge," Schoultz said.
Skilled plant operators will have their own knowledge of how different products function, but there are often times when the conditions may change and something different is needed; consulting with a dealer or other expert is always a good step, Larsson said.
Maintenance is another area in which the choice of media can make a difference; changing wire media can be a big challenge compared to polyurethane or rubber.
"If you have a screen with a wire cloth, that's typically four feet long and six to eight feet wide - that can be a heavy piece of equipment that you might need a crane to lift out," Larsson said. "If it's a modular system, each module might weigh less than 10 pounds so one person can lift it."
Modular rubber and polyurethane systems can be changed out in small segments where necessary, and products in the Metso line can be snapped in or out with ease – or take advantage of a new hammerless attachment system that uses special pins installed with a cordless drill for quick and easy changes. It's much easier to change media in multi-deck screens when using modular systems as well.
Cutting maintenance costs and needs down can also be done using new technologies that have come to the market in recent years. Metso's Screen Planner, for example, is an online tool that allows users to build and configure their screens, then track wear as inspections are completed. Electronic monitoring can also help with optimizing the performance of a screen and the media installed in it.
"What's come into play more is optimization of the screen speed and stroke," Schoultz said. "That's done through electronic devices attached to the screen while it's running; they can tell you the speed of the stroke or the range of motion of the screen, and allow you to optimize the machine based on the opening and other factors to get the best efficiency out of your media."
All in all, there are many different factors that go into the right choice of media for any screening operation. Every one is different, and taking advantage of expert knowledge is always a good approach to finding the right solution.
"Different OEMs have different approaches, different lengths, different insight between the walls of the screen, and those are all things that we need to keep track of," Larsson said. "It's a complex world."