Oil cleanliness: the key to hydraulic system reliability
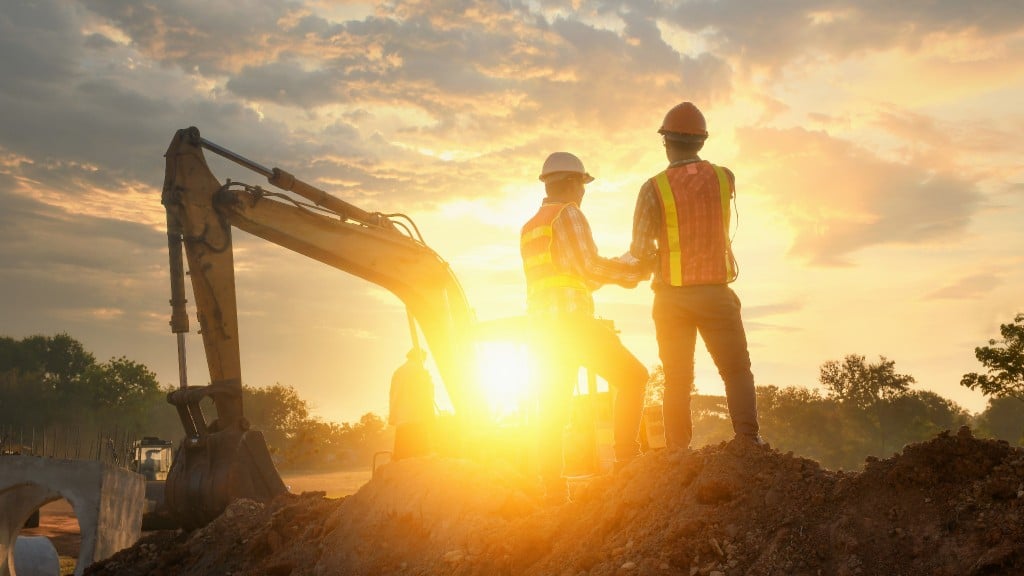
Maintaining an appropriate level of oil cleanliness is critical to the success of the hydraulic systems in any heavy equipment operation. In fact, the presence of contamination in hydraulic fluid is the single most important factor influencing the reliability of the system - between 50 and 70% of all hydraulic system failures can be linked to contamination.
Taking proactive and predictive steps to ensuring oil cleanliness can go a long way to mitigating this risk. By implementing processes to ensure fluid and system cleanliness, maintenance professionals can increase the life of system components, reduce unplanned downtime and maintenance costs.
To put it simply - the cleaner the oil, the longer equipment will operate reliably. This is why operators that keep their oil clean are at an immediate advantage to those that don't. Ensuring proper oil cleanliness enables you to realize the full lifecycle of the oil, which means you get the best value out of your investment.
What is oil cleanliness?
The measure of oil cleanliness refers to the level of particle contaminates present in the oil, including both insoluble and hard particles, which are often not visible to the naked eye. The presence of these contaminant particles can interfere with the hydraulic fluids' ability to lubricate parts with tight clearance, causing increased wear to system components. This is key in hydraulic systems, where tight clearances and harsh operating conditions cause a greater sensitivity to particle damage.
This form of contamination can occur from two sources, internal and external. External contamination commonly refers to foreign particles such as dust, dirt and other matter that can make its way into the system. Whereby, internal contamination occurs as a result of mechanical wear inside the equipment or oil degradation, causing particles to disperse within the system. While mechanical wear can easily lead to internal contamination, it is more likely for contamination to be introduced to a previously acceptable system via hydraulics seals, inadequate air breathers, or during sampling, filter changes, storage, handling and dispensing.
However, it's important to note that oil contamination cannot be entirely eradicated, only controlled. Acceptable levels of contamination will always be present and will vary depending on the type of system, often determined by Original Equipment Manufacturers (OEMs).
How to ensure oil cleanliness?
Oil cleanliness can often go unnoticed or set aside as ‘out of sight, out of mind'. But with equipment reliability and performance largely linked to the financial bottom line, the benefits of oil cleanliness cannot be overlooked.
There are three additional simple maintenance principles that can ensure hydraulic systems are protected against contamination and an acceptable level of oil cleanliness is upheld:
- Filtration - During the lifecycle of a lubricant it will become exposed to internal and external contaminants and using filters of the correct micron rating and beta ratio (filter efficiency) will allow contaminants to be removed faster than they are generated. An effective filtration system will work to ensure that the filtered oil remains free of impurities, therefore safeguarding the performance and reliability of the hydraulic system.
- Storage, handling and dispensing - Lubricants become susceptible to contamination during storage, and especially when stored for long periods of time, handled or moved. Lubricants can also be exposed to contaminants during any transfer process - whether it be pumping from bulk dispensing or singular drums - open nozzles and drum bungs can leave any oil susceptible to contamination. When dispensing from bulk or drums, desiccant type air breathers or at least sintered bronze bung filters, should be ideally used.
- Used oil analysis (UOA) - With today's hydraulic systems being smaller and more powerful than ever, the demands of system cleanliness are increasingly critical. As potentially hazardous particles can be invisible to the human eye, cleanliness monitoring through a used oil analysis program is vital in detecting contamination. Monitoring the levels of key properties within the hydraulic oil provides owners and operators with the ability to predict issues and schedule maintenance before problems become too expensive or serious to repair. Effectively helping reduce the risk of unplanned downtime and sudden failures, used oil analysis and data interpretation can reveal the level of contamination present, help identify its cause and provide another effective method for reducing maintenance costs and downtime.
For best practice, it is recommended to filter all oil storage into a facility by using kidney loop filtration on all bulk storage tanks, as well as establishing proactive and reactive filtering measures. In order to avoid the costly process of frequent lubricant changes due to contamination and the downtime associated with the process, the use of filtration devices is recommended to remove unwanted particles, which will extend the working life of the oil and components in your system. Filtration devices, such as portable filter cart or stationary filtration installations should be used on a proactive basis to remove particles and a reactive basis when oil sampling indicates that ISO particle counts have risen above target levels.
It is also important to use the correct size and media of filter based on its absolute micron rating and beta ratio (efficiency) at a given particle size, to achieve your desired cleanliness target level. Depending on whether the lubricant will be passed through a filter once or several times will also determine what filter efficiency will be needed. It is recommended to always work with the oil manufacturer to ensure you are using the appropriate filter size for the lubricant.
It is also common for lubricants to become contaminated via dispensing equipment that has not been properly flushed, cleaned or is unsuitable for the use. To avoid contamination during these processes, oil should be filtered as it is transferred into sealed, air-tight containers. Dedicated transfer pumps and/or filtration equipment should be also be used for each product type, ideally ISO graded to support the correct contamination level.
The current particle counting method for coding the level of contamination by particles is known as the ISO Cleanliness Code, which works to determine the number and size of the particles in the oil sample being tested. Acceptable levels of oil cleanliness are often determined by the system builder or hydraulic pump OEM, providing the assurance that any fluid used is maintaining a satisfactory level according its accepted contamination level. According to this standard, a code number is assigned then to the particle count with values derived at three different particle sizes: greater than 4 microns, greater than 6 microns and greater than 14 microns. For example, 19/17/13 could be the target cleanliness code that a supplier wants a fluid to meet. If your result is 18/17/13, you can be assured that your oil cleanliness meets the requirements. If your result is 20/17/13, it means that the fluid contains an excessive amount of particles greater than 4 microns, therefore additional or finer filtration is required.
Having this used oil analysis data is extremely useful, but the next step is to be able to manage and interpret it quickly and effectively. Forward-thinking reliability and maintenance teams are now taking advantage of digital diagnostic tools, like Petro-Canada Lubricants' LUBE 360 Oil Diagnostics, to support equipment and maintenance managers to do this. These digital tools can allow samples and data results to be accessed from tablets and mobile devices, allowing immediate access to the latest insight, 24/7. For asset managers, the easy-to-use dashboard graphs can help to prioritize critical results and detect abnormalities within the results, meaning contamination is recognized earlier and steps like filtration can be taken to ensure oil cleanliness is maintained. Utilizing oil diagnostics keeps an operation one step ahead by using the latest technology to proactively track where maintenance is needed and predict where it will be needed in the future.
Maintaining acceptable oil cleanliness is about more than just using the correct lubricant, it is also implementing an approach to ensure a clean environment that reduces the risk of contamination, so that the components life is extended. Operators should implement a proactive and predictive approach to oil cleanliness built around filtration, adequate storage, handling and dispending and a used oil analysis program. A proactive plan to tackle the risk of contamination should be front and centre of all lubrication and maintenance programs - this will help ensure the longevity, reliability and operational productivity of any hydraulic system.
Neil Buchanan is the Senior Technical Advisor at Petro-Canada Lubricants.
Company info
2310 Lakeshore Road West
Mississauga, ON
CA, L5J 1K2
Website:
www.lubricants.petro-canada.ca