How a construction equipment rebuild extends the life of your most valuable asset
Today’s expanded rebuild options drive down total cost of ownership and help companies get the most from their equipment
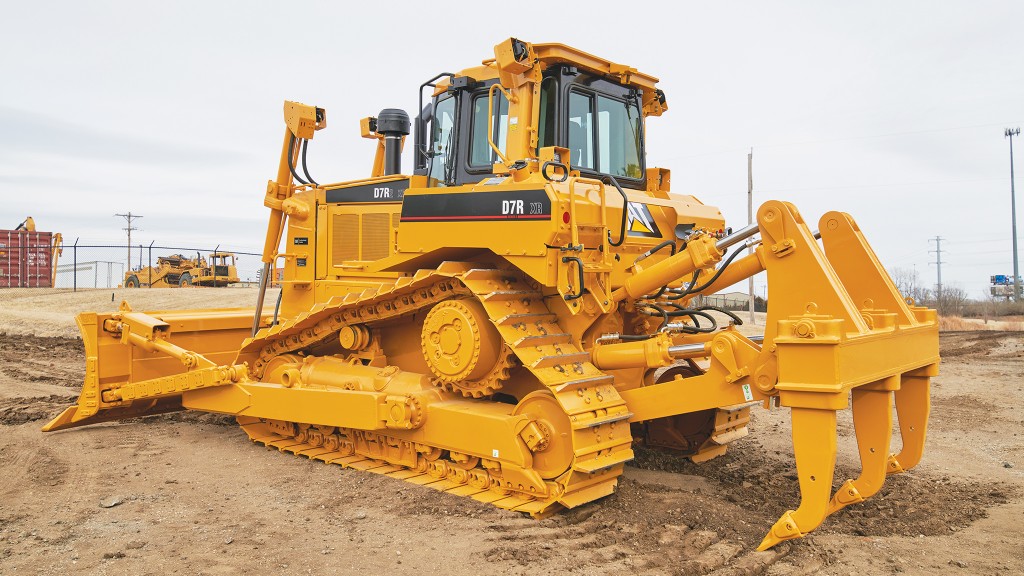
Machine and component rebuilds for heavy construction equipment are part of many contractors' fleet management plans. Today, contractors target tens-of-thousands of operating hours, multiple service lives and low total cost of ownership (TCO) from their most valuable assets by implementing a regimented maintenance plan and multiple machine rebuild strategies.
"Service departments consistently following the machine's suggested maintenance schedule, oil sampling guidelines and monitoring telematics data will typically realize the lowest total ownership costs," comments Dave Matranga, a Caterpillar market professional for engines and Cat Certified Rebuilds (CCR). "Include a rebuild strategy into the mix, and companies can drive down TCO even further."
Expanded rebuild options weren't always the industry standard. As recently as the early 1980s, equipment manufacturers didn't offer certified machine rebuilds. If a contractor wanted a "like-new" piece of equipment, well, buying new was the only option.
In response to challenging economic conditions and voice-of-customer requests, Caterpillar was among the first heavy equipment manufacturers to introduce its CCR program in 1984, which gave contractors a "like-new" machine at a lower cost alternative to buying new. The machine was rebuilt from the frame-up - axles to cab - with the goal of getting more than a just few thousand extra hours out of the machine.
"The ‘like-new' product offered a second life for the machine," comments John Baptiste, project engineer - Caterpillar Certified Rebuild Products. Matranga adds, "The first units rebuilt through our CCR program were Cat D8K dozers. These dozers offered comparable performance and appearance to their brand-new counterparts with similar extended protection plans and financing rates and options, so they were, indeed, ‘like-new'."
The typical CCR machine rebuild included approximately 7,000 part numbers either replaced or refurbished. Over time, trends showed better maintained and operated equipment resulted in more reusable parts, lowering machine rebuild cost. "A well-trained operator goes a long way in maximizing machine life," comments Eric Mathewson, senior parts specialist for Caterpillar Undercarriage and Ground Engaging Tools (GET). "Working a side-slope in one direction too long or improper use of the bucket were instances that led to uneven wear and a shorter life for wear items and machine components."
Rebuild programs like CCR were well received by contractors and participation rates remained relatively consistent over the years. However, the extensive program left out companies that wanted targeted system or component rebuilds, so manufacturers responded with options to meet those customers' needs.
"In 2001, we introduced our Certified Power Train rebuild program that upgrades only the systems that move the machine, and participation in our rebuild program tripled," offers Matranga. "Caterpillar then expanded the program to include Certified Engine Rebuilds, Certified Hydraulic Rebuilds and Certified Machine Component rebuilds over the following years, and program participation rose significantly. Companies realized that reusing components, versus scrapping or landfilling, lowered TCO plus improved sustainability."
What's the standard?
Baptiste recommends working with the dealer even before machine purchase to review applications, how long it is anticipated to remain in the fleet and the company's expectation for uptime availability. This allows the dealer to run a life cycle analysis and have targeted maintenance and rebuild solutions planned.
"We have some customers who run their operations 24-7 and demand machine uptime availability in excess of 90 percent," says Baptiste. "The dealer preschedules downtime for maintenance and rebuilds at prescribed intervals, so the equipment is better able to meet this uptime expectation," he says.
While some may assume that all rebuilds are equal, this is not the case. When it comes to rebuilds, selecting a provider just on initial price-point can sacrifice post-rebuild machine life and productivity.
Over the years, manufacturers have developed rebuild standards. Caterpillar, offering more than 35 years of experience with its CCR program, provides its dealers with detailed reuse and salvage guidelines specific to machines like dozers, excavators, trucks and loaders. These documents guide dealers through properly inspecting components for reuse or salvage, based on extensive rebuild history and conservative criteria. This is designed to provide more consistent rebuild results, regardless of where it is performed.
Baptiste mentions friction disc replacement and Thermal Spray as examples of where the reuse and salvage guidelines help to lower rebuild costs. "Other companies may overlook the reusability of friction discs or plates and buy new. Caterpillar has an 18-page document with pictures to help our dealers identify which items can be reused or reconditioned," he says. "We also offer Thermal Spray guidelines for components like hydraulic cylinder rods, so they can be salvaged for another life."
Matranga adds that Caterpillar guidelines require all switches, harnesses and sensors be replaced during a rebuild. "The highest equipment downtime drivers are miscellaneous items like sensors and switches, so our guidelines require these be replaced whereas other providers do not," he says.
Changing machine designs
Like rebuild programs, not all machine designs are created equal. Contractors must investigate if a machine is built with components designed for a second or third life.
With certified rebuild offerings becoming the norm, equipment designs have evolved over the years with a vision of extending machine service life. "We test our frames using the most severe applications the machine will face in the field to extend the welds, especially the hidden ones, well beyond the first or second machine life," offers Mike Chica, medium wheel loader large structure engineer for Caterpillar.
The New Product Introduction (NPI) program at Caterpillar starts with a very prescriptive process, from concept to production, detailing machine and customer requirements. One component of the program requires the NPI team to complete a repair process engineering template, which serves as a check of repairability of various machine systems, correlating to machine rebuildability. "NPI is about meeting the brand promise and trying to extend the life of machine subsystems," mentions Patrick Hill, life cycle manager for Caterpillar medium wheel loaders. "The group is passionate about meeting customer life cycle needs."
Vic Simkus, medium wheel loader engineer for Caterpillar, is adamant that the quest for component longevity must also include the manufacturer's suppliers of purchased finished components. "The manufacturer cannot abdicate quality to the component supplier," he says. "At Caterpillar, we focus on reliability metrics to increase machine longevity and work with the supplier to put our intellectual stamp on it."
Advanced monitoring
Monitoring machine performance plays a critical role in helping to extend a machine's service life and rebuild intervals. This begins with the basics of following the prescribed maintenance intervals and having a well-trained operator communicate any issues with the shop.
"Our goal is to have companies catch issues at the Level 1 parts stage, which are parts designed to wear, are not rebuildable and protect the more expensive machine components that can be rebuilt," says Mathewson. "Catching issues early increases uptime availability and drives down the TCO," he adds.
Routine fluid sampling through programs like Cat S∙O∙S Services provide insight to internal component wear and potential failure. This data analysis allows contractors to plan for any necessary component repair or rebuild. "Trends like increased metal fragments in the oil give an owner the necessary data to make proactive service decisions," says Matranga.
A machine's duty cycle in the field, rather than machine hours, offers a better indicator of service life and rebuild interval frequency. Advanced monitoring of field fleet equipment through telematics provides insight as to how a machine is used in the field. "We track fuel burn, which is a key indicator of the machine's workload," says Matranga. "The higher the fuel burn, the higher the workload and the shorter the time period is between rebuilds."
Matranga also points to recent developments in remote services as the next evolutionary step in digital machine monitoring to catch field issues early, extending time between rebuilds and lowering TCO. "Our dealers can now run diagnostics remotely through Cat Remote Troubleshoot and analyze real-time data to help reduce equipment downtime," he explains. "It's also possible to upgrade a machine's latest software remotely through Remote Flash."
Consider upgrades
The term "like-new" means just that to many manufacturers, as they push the boundaries of rebuilds beyond refurbishing or replacing the machine's core components. Cat dealers offer customers the latest technology, wear parts and service updates available for a machine. This way, the rebuilt machine is expected to perform like a new piece of equipment coming off the assembly line.
Several updates are automatically included during a rebuild performed by the dealer. "CCR rebuilds automatically receive appropriate updates that involve machine safety and critical performance upgrades," mentions Baptiste. "For less critical engineering upgrades, customers can add those as options at the time of rebuild."
Mathewson advises companies not to ignore the working end of the equipment. Wear strips and work tools that protect the more expensive components are continually upgraded by manufacturers. "Our new hammerless GETs fill the bucket more efficiently and usually require about half the time to change, so upgrading work tools to get more from a machine is a worthwhile discussion to have with the dealer during a rebuild," he says.
The evolution of emissions standards has resulted in significant efficiencies in engine design, allowing them to last longer and, in some cases, save a considerable amount of fuel. "One customer upgraded from a Tier 2 to Tier 3 engine, and the fuel savings alone led to a return on investment, in this case, of about 1.5 years," says Baptiste.
A rebuild is also the right time to approach the dealer about available technology upgrades to optimize machine efficiency. Manufacturers continually upgrade production-enhancing solutions like semi- and fully autonomous machine operation, grade, slope, and payload technologies. "Our technology is backward compatible within a model series, so an earlier model receiving a certified rebuild can be equipped with the latest technology," mentions Matranga.
Whether it's to extend a machine's service life, lower TCO or enhance production efficiency, certified rebuilds offer contractors another avenue for getting a "like new" machine at about half the cost of purchasing a new machine. "Certified rebuilds should be considered as a part of a company's fleet management strategy," offers Mathewson. "Equipment dealers will be able to walk customers through the rebuild process and help them get the most from the rebuild."
Rick Zettler is a technical writer who covers the construction equipment industry.