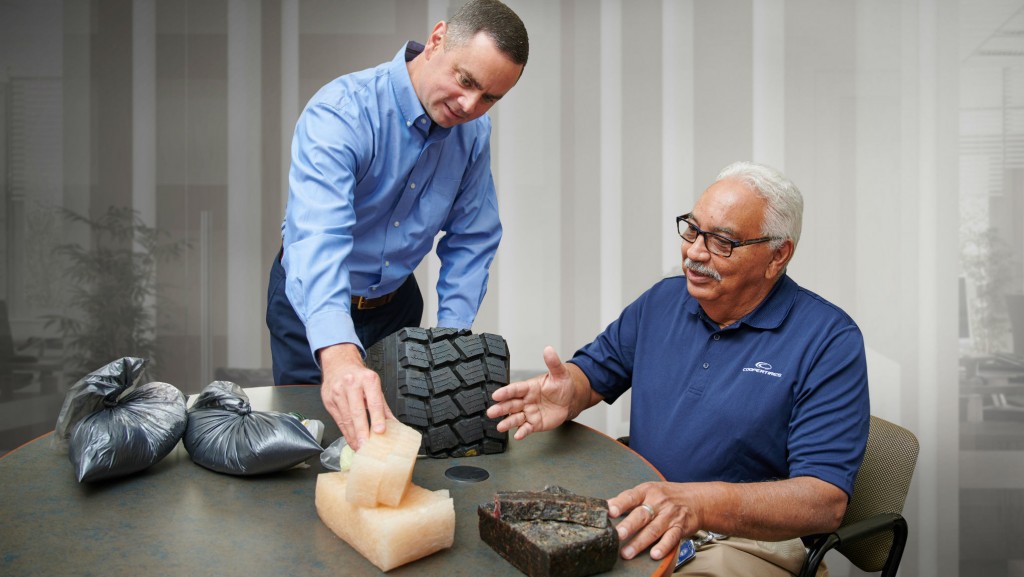
Today's commercial truck tires are rolling pieces of sophistication. They are the vessels that carry the payload on dump trucks, mixers and tractor-trailers, so the importance of their construction and foundation (the casing) can't be understated.
"Other than tires for the aerospace industry, commercial truck tires have arguably the toughest job in the tire business," said Phil Mosier, Cooper Tire's manager of commercial tire development. "It's why we dedicate so much engineering time to ensure our tires perform safely and productively. From a productivity standpoint, since tires are such a high operating cost, miles to removal and durability – balanced by a competitive price – is what can keep help construction fleets keep costs down. Providing our customers with a low cost of ownership is what Cooper is all about."
What makes tires so high-tech?
On the surface they're black and round and look pretty much the same. "Commercial truck tire manufacturers all primarily use natural rubber for heat resistance and durability," said Mosier. "As a comparison, the automotive tires you drive on generally consist of more synthetic rubber than natural rubber. And, truck tires all use carbon black to some degree as a primary ingredient in the chemistry of the tire. But, that's where the similarities end."
According to Mosier, some commercial tire brands are well known and have been around for generations, proving their performance on North American roads. Others are less known with limited distribution. "And, like with any product, you have varying degrees of quality and expectations – in the tire world you have up to four tiers of quality and pricing," he said. "And for the most part, you get what you pay for."
A tier 4 tire might show up sporadically in the U.S. market for example, then disappear. And, there are a lot of players. "The buyers of these tires are looking for rubber to put on the road - not high mileage, retreadability or other metrics," explained Mosier. "They're low-priced tires with casings that typically don't hold up to multiple retreads. When you move up to tier 2 and tier 1 tires, you find a huge quality improvement, and casings with a four-belt package. These tires give you better overall performance, and are engineered for multiple retreads. One way to sum up the quality variant is to look at the tire manufacturer's warranty. The better it is, the higher the quality. A tire manufacturer knows better than anyone else how its tires will perform. At Cooper, for example, we track performance data – it's why we're able to offer an industry-leading warranty program."
According to Mosier, tires for construction applications each pose different challenges and that's why wear (miles to removal) can vary greatly. Dump trucks, for example, have to contend with driving off-road – on gravel and rock, for example, so the tread and tire casing must be tougher to resist damage from rocks. Some fleets operating dump trucks, with diligent tire maintenance practices, get more than 80,000 miles on drive tires.
"Those running tractors with lowboys have a whole other set of tire needs," Mosier continued. "The trick – or the art in what we do – is in balancing the performance attributes of the tire," he said. "For a tractor hauling a lowboy trailer with heavy construction equipment, the first five miles and the last five miles of a trip wear out a tire faster than the 100 miles in-between. Stopping, starting and scrubbing tires are what wear away the tread and it can impact uniform wear. So, as a tire designer, we have to figure out a way to resist those forces in order to make a better tire. Anyone can build a tire to go straight for 500 miles... and have good wear. But to get top performance you have to offset the forces that eat up a tire. That's the challenge."
Also challenging tire designers are the different wheel positions. With drive tires you need a combination of deep tread depth matched with traction.
"Since tread wear is faster, we need to go with deeper tread depth – the Cooper Severe Series MSD for example has 32/32nds of tread – and sturdy lug shapes to enhance traction," said Mosier. "And the traction design elements need to carry all the way through to the bottom of the tread, so you don't have to pull the tires prematurely due to lack of grip on the road. In the past, the typical width of a drive tire was 8-1/2 inches – now it's more than 9 inches. What this has done has given a bigger footprint to spread weight, and that helps improve tire longevity."
According to Mosier, commercial tires are evolving at a rapid pace. "Compounds continue to change and the mixes keep improving," he said. "The use of new raw materials and formulations allow us as tire designers to expand performance so that improvements can be made in durability – chunk and tread tear resistance – plus in treadwear and traction."
Another component in continued tire quality improvement is in the manufacturing process. To be considered a top tire manufacturer, tires coming off the line need to be uniform.
"And that means the specs and tolerances are very tight," Mosier said. "For top tire brands, if the tires don't meet spec, they're rejected. And top brands, like Cooper, use x-ray and uniformity machines to inspect every tire coming off the line. Manufacturing commercial tires has come a long way. These improvements mean tires from the leading brands have better uniformity, which translates to longer, more even wear."
All told, Mosier said it's an exciting time to be a tire designer. "We have so much technology and research at our fingertips," he said. "We have chemists with PhDs who uncover new ways to perfect compounding, and we have new ways to design and test our tires to ensure top performance. There is so much opportunity in the commercial tire space – it's exhilarating to come to work every day to see what we can accomplish."