Electrification is the future of fleets: Cummins
New study calls for collaboration and continued investment towards electric power
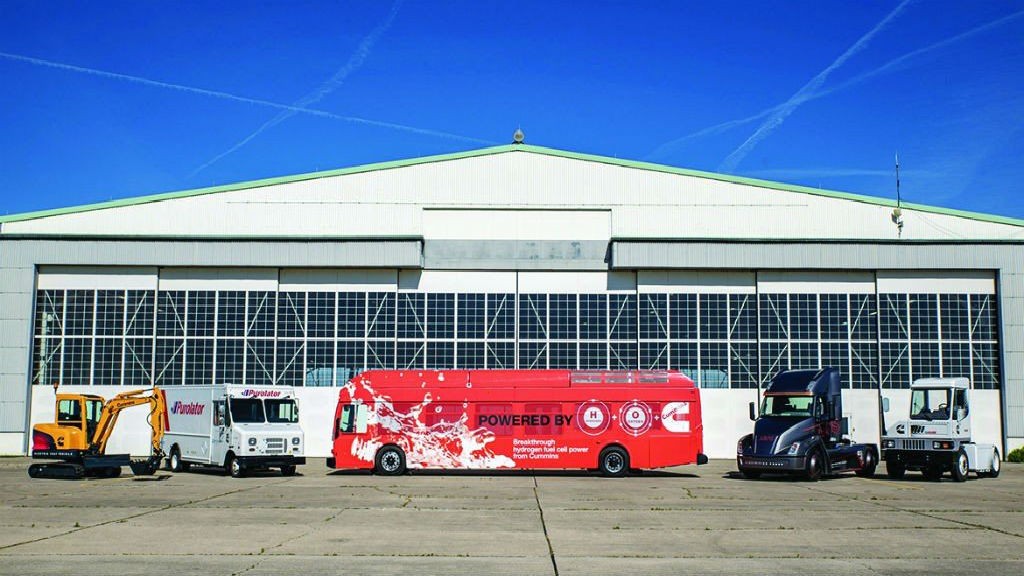
With a growing need to reduce the world's need for fossil fuels that will only grow in the coming decades, now is the time for manufacturers to consider how best to power their fleets moving forward, according to a new white paper produced by Cummins. In the paper, the engine manufacturer is calling for expanded collaboration to move electrification of vehicles ahead, as well as identifying the need for policy changes to assist the move away from carbon-based fuel sources.
Cummins has identified four areas in which electrification must continue to mature for it to succeed, which are similar to those that drove the development of the internal combustion engine: technological maturity, infrastructure capacity, economic reality and regulatory buy-in. In the introduction to the white paper, Julie Furber, vice president of Cummins Electrified Power, said that collaboration across the industry and with policy makers can drive emissions reduction.
"Cummins has worked on the means to manufacture diesel engines with the lowest possible particulate matter and nitrogen oxide emissions, minimizing the impact its engines have on the planet," Furber stated. "However, we know by the end of the 21st century we will need to be less reliant on fossil fuels, and now is the time to diversify how we power mobility and heavy industry."
Battery development moving forward
Growth in technology as it applies to battery development is one key step forward, according to the paper. Lithium-ion batteries, a central need for advancing electric vehicle use, have become a more mature technology recently. With concerns surrounding EVs centering on their ability to take and hold a charge, efficient powerful batteries are a must.
Development of lighter-weight Li-ion battery cells is important to providing greater range for electric vehicles. According to the Cummins white paper, older batteries using a lead-acid technology require more weight and size to hold useful energy levels. A lead-acid battery weighing one kilogram can generally supply one Watt of power for 35 to 40 hours (35-40 Wh/kg), while one taking up one litre of volume can do the same for 80 to 90 hours (80-90 Wh/L). In comparison, today's Li-ion batteries have far greater energy density; they can have 250-300 Wh/kg and 500-650 Wh/L – giving them the ability to store enough energy to let vehicles travel longer distances before recharging.
Since Li-ion technology has become commercially viable, the energy density per kilogram has more than doubled, and per-litre density tripled, Cummins notes. The goal is to keep this development moving forward, so that batteries can power trucks and other vehicles further while reducing the space and weight required for battery cells.
"We're working on optimizing our battery design. Innovative materials for anode and cathode manufacturing can affect not just the battery's capacity, but also its cost per kilowatt-hour, maximizing battery life, optimizing charge rates, managing the range of temperatures it can endure without damage, and above all else, ensuring its safety," Andrew Penca, Executive Director, Electrified Power for Cummins stated in the paper.
A second area that must be tackled for effective electrification is the infrastructure to charge those more efficient batteries. Many countries are making efforts to add charging stations, especially in urban areas, but availability and speed of charge must be addressed.
While commercial vehicles may have long stretches of downtime that could be used for charging, the space needed must be considered in infrastructure design, and to maximize the use of vehicles, chargers and space charging speed must be increased. Fast chargers are improving steadily, but more must be done to meet trucking needs. In addition, the added draw of power from the electric grid needs to be considered - additional lines may be required for charging sites, for example.
Economic questions remain
One commonly known aspect of electric vehicles is that there is a price to pay for reducing emissions – EVs come at a premium compared to their fossil-fuel brethren. That comes back to the owner over time thanks to fuel savings, but there are other costs that need to be addressed as well.
While manufacturing costs for batteries are expected to drop, the need to replace those batteries down the road when their ability to hold a charge lessens. In the white paper, Cummins suggests that leasing may be an option for battery replacement, and allow those degraded batteries to be used for other energy storage uses later on. There are other costs such as maintenance and installation of charging points, but those can be mitigated or reduced using technology such as advanced telematics, Cummins advises.
Return on investment is a key selling point, and as technology advances, EVs are beginning to move towards parity with diesel vehicles overall.
Finally, public bodies must move forward with electric-friendly policies and infrastructure planning to help encourage the development of EVs. Incentives to drive more electrification will help make the move away from fossil fuels much easier.
This article originally appeared in the February 2020 issue of Heavy Equipment Guide. Check out the digital edition here.