Selecting the right truck engine for the job
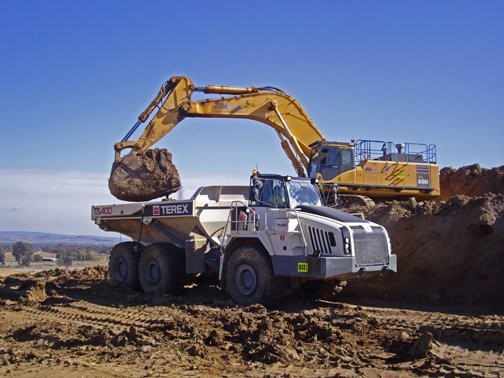
You have a number of considerations when purchasing articulated haul trucks for your operation. Truck capacity, loading capabilities, hauling distance, road conditions and dump cycle times are just a few elements that are traditionally analyzed to determine the correct number and size of trucks to increase productivity and efficiency, and reduce operating costs.
With the recent change to ultra-low sulphur diesel (ULSD) fuel and the reduction of nitrogen oxide (NOx) emissions to meet Tier 4i/Stage III B standards, selecting the right engine technology for the application must also figure into the equation.
There are two very different approaches to meet Tier 4i/Stage IIIB emission standards. Exhaust gas recirculation (EGR) recirculates a measured amount of exhaust gas with incoming air to reduce NOx levels and requires a diesel particulate filter (DPF) to reduce particulate matter. The second alternative, selective catalytic reduction (SCR) uses diesel exhaust fluid (DEF; or also known as AdBlue) to convert NOx into a harmless mixture of nitrogen vapour and water.
“At Scania, we have experience with both SCR and EGR technologies used in on-road trucks,” says Peter Sundell, project manager, application engineering for Scania CV AB, manufacturers of the Tier 4i/Stage IIIB engines powering Terex articulated dump trucks. Ken Emmett, truck product manager for Terex Construction Americas adds, “As far as application rules of thumb go, SCR technology will provide a better solution for engines above 325 hp (242 kW) and operated at a low duty cycle (below 50%). EGR technology is better suited for lower horsepower engines operating in high duty applications.”
EGR analyzed
Since EGR pumps oxygen-depleted exhaust back into the engine to reduce NOx emissions, the engine works a little harder. “To get the same power out of the engine, its size is also increased,” says Emmett. Additional engine components increase the system’s complexity and require more space under the hood.
The engine requires larger cooling systems and a turbocharger specifically configured for the EGR solution to make up for the lack of oxygen in the exhaust. Up to 30% of oxygen-depleted exhaust is recirculated, which then must be cooled in order for emissions to be removed. The EGR engine often requires a diesel oxidation catalyst (DOC), which interacts with diesel fuel to oxidize pollutants before they exit the system.
These lower combustion temperatures reduce NOx but result in an increase in particulate matter. This matter is trapped in the DPF and, by regeneration, is oxidized into nitrogen gas and carbon dioxide and expelled through the exhaust pipe. The regeneration process increases the heat in the exhaust system to burn off the particulate matter.
There are two methods of regeneration in today’s engines: passive and active. The primary, passive regeneration occurs during normal engine operating conditions, depending on the duty cycle, and is the most fuel-efficient method for cleaning the DPF. This process does not impact machine operation and does not require operator involvement.
If the truck’s duty cycle is not high enough, then active regeneration serves as a backup system. “This only occurs when passive regeneration is not possible, based on temperature, load and speed,” says Emmett. Active regeneration requires injecting fuel into the exhaust system, increasing fuel consumption and elevating exhaust temperatures up to 1,300 degrees F (704 degrees C) to clean the filter. This is often done without impacting truck performance, but, in extreme cases, it could require the truck to be parked while the filter is regenerated, lowering production potential.
It is this critical balance between machine load and the particulate filter regeneration that is at issue. Articulated dump trucks operate in a low engine demand duty cycle. “The normal duty cycle of a truck is 30 to 40%, which makes it difficult for the engine to clear the DPF through passive regeneration,” mentions Emmett.
Terex has extensively studied the relationship between duty cycle of its machines and the best Tier 4i/Stage IIIB solution. “Since Terex does not manufacture engines,” explains Emmett, “we are able to work with leading engine manufacturers to choose the most efficient technology to match the application. We offer EGR technology for our material handlers, which have a high duty cycle of up to 70%.” For articulated trucks, however, Terex and Scania see SCR as the more efficient approach for customers.
SCR – the preferred option
The primary emission-reducing ingredient of an SCR engine is DEF, a safe, stable and non-toxic liquid. The straightforward SCR system is composed of a DEF injector, supply module and storage tank. A chemical reaction takes place inside the SCR chamber to convert NOx into a harmless mixture of nitrogen vapour and water.
When compared to EGR, SCR is a much simpler technology that enables the manufacturer to fine tune the engine for performance without sacrifices. “With the SCR system,” says Sundell, “emissions are ‘taken care of’ in the after treatment system, which allows us to adjust the engine for lower fuel consumption and better responsiveness.” Scott Pollock, global product manager for Terex articulated trucks, continues, “Even when the cost of DEF is taken into account, the combined diesel and DEF cost for the new Terex TA300 is 7% lower than the cost of fuel in the previous Tier 3/Stage IIIA engine.”
Production of Terex articulated trucks with the Scania SCR engines began in June 2011. Scania engines are also equipped in various equipment lines within the multiple Terex business segments. “We have hundreds of SCR technology engines operating in North America,” says Sundell. “One of our early SCR prototype engines was installed in a piece of Terex port equipment and now has more than 9,000 operating hours on it. We also have a Tier 4i engine in a wheel loader with more than 11,000 operating hours.”
Terex Construction offers Scania SCR engines for its TA250, TA300 and TA400 articulated trucks, designed for the construction and aggregate markets. The 9 and 13 litre engines offer from 311 hp (232 kW) to 444 hp (331 kW) gross power and are fine-tuned for efficient operation, based on application demand.
Demystifying DEF
While SCR may be a preferred technology for Terex off-road trucks, DEF is a relatively new additive within the off-highway machine industry, which can lead to some concern. “Customers often ask me questions about DEF, based on what they have heard and on some misconceptions in the marketplace,” says Emmett.
The DEF used in SCR systems is a carefully blended aqueous solution consisting of 32.5% high purity urea and 67.5% deionized water. A compound of nitrogen, urea turns into ammonia when heated and has been used in a variety of industries, including agriculture.
The 32.5% urea concentration gives DEF its lowest freezing point of 12 degrees F (-11 degrees C). Both the deionized water and urea freeze at the same rate, so as it thaws the solution does not become diluted or over concentrated.
During vehicle operation, SCR systems are designed to heat the DEF tank and supply lines. “The engine cooling circuit is connected to the DEF tank, and the hoses are electrically heated to keep DEF a liquid,” says Sundell.
Should the solution freeze when the vehicle is shut down, the system is designed to withstand the expansion and quickly return DEF to its liquid form, so vehicle operation will not be impacted. “We have trucks dependably operating in -40 degrees F (-40 degrees C) temperatures in Moscow,” says Emmett. Sundell adds, “I have not heard of any cases where DEF freezing has caused problems with Scania engines.”
While the on-road use of SCR technology has led to a growing infrastructure of easily obtained DEF, the off-road infrastructure is still evolving. The fluid can be obtained from a number of locations throughout North America, and there are a variety of storage options available for off-road use.
Canisters in sizes up to 4.8 gal (18 l) can be obtained for emergency use, but Emmett recommends buying and storing DEF in bulk for off-road fleets. “Fifty-five gal (210 l) barrels are available for small fleets of up to five machines,” says Emmett. “Intermediate operators can get 265 gal (1,000 l) containers for fleets from 5 to 15 machines, while larger fleets will realize the most benefit from high-capacity bulk containers from 400 to 1,320 gal (1,500 to 5,000 l).”
DEF storage life is temperature dependent. According to ISO Specification 22241-3, storage temperatures of less than 50 degrees F (10 degrees C) give DEF a minimum 36-month shelf life, while storing in temperatures between 87 degrees to 95 degrees F (30 degrees to 35 degrees C) drops the shelf life to a minimum of six months.
Pricing for DEF, as with other items, depends on the quantities in which it is purchased. It can cost more than diesel fuel when purchasing it in 1 gal (3.8 l) containers. When purchased in bulk, DEF can be as low as 60% of the cost of diesel fuel.
SCR engines use DEF very efficiently, so the costs are reasonable. “DEF consumption has shown to be less than 10% of fuel consumption,” adds Emmett. “Tests have shown the Tier 4i (Stage IIIB) engines now powering Terex trucks are more fuel efficient than the previous Tier 3 (Stage IIIA) engines, which more than offsets the cost of DEF.” The 13.7 gal (52 l) DEF tank on a Terex articulated truck requires filling every other fuel tank fill-up.
SCR or EGR, the choice is yours. However, those closest to the emissions control technology that is here to stay see the best use of the technology being application dependent. “There are advantages and disadvantages with both technologies, but for dump truck applications, SCR is the preferred technology,” concludes Sundell.