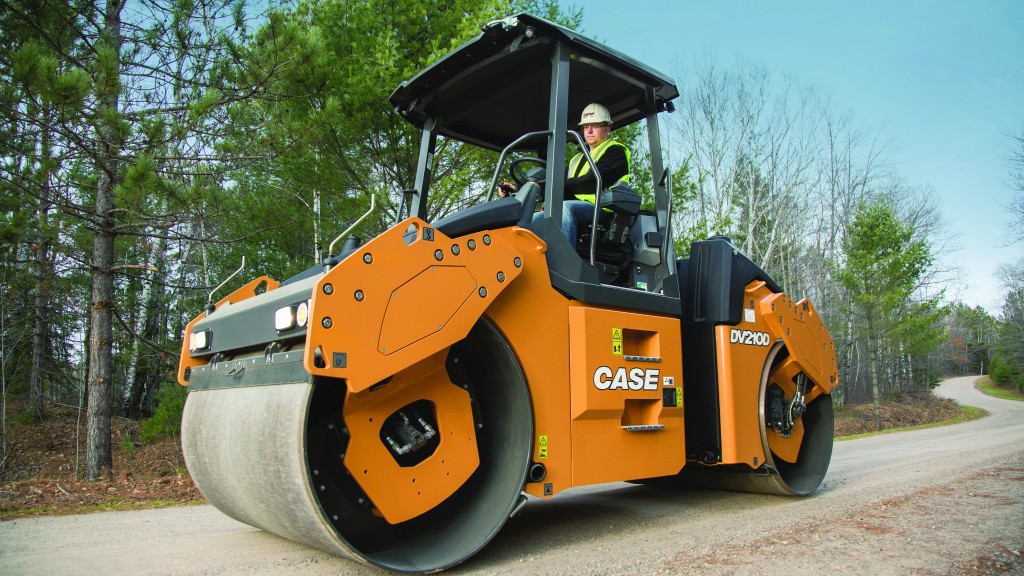
The needs of roadbuilders vary from region to region. Evolving highway specifications, project owner demands, maneuverability and ease of operation are just a few things that contractors must factor in when choosing a tandem vibratory roller.
Roadbuilders' needs driving direction of tandem rollers
According to Tim Kowalski, Hamm applications support manager, Wirtgen America Inc., roadbuilders need to be able to compact quickly and choose their roller based on the type of mix used.
"Depending on the mix type we can match the roller to the mix to give the customers an advantage when it comes to compaction. We are also constantly training customers on proper rolling techniques to help them get the most out of the rollers in the fewest number of passes."
"We have double-drum standard vibratory machines at 3,000 vpm, high-frequency double-drum vibe machines at 4,020 vpm. We have oscillation rollers with the front drum in standard vibe at 3,000 vpm, and the rear drum using oscillation at a frequency of 2,200 vpm. We also have rollers with a standard vibe drum in front with rubber tires in the rear," said Kowalski.
Nathaniel Waldschmidt, product marketing manager, compaction, for Case Construction Equipment said to look for a roller with crab-offset-capable drums. "The ability to offset drums is important for a couple of reasons. When compacting asphalt on a roadway or another large-scale project, it's important to bind each pass together. By having a compaction machine that allows you to have the rollers either in-line or offset, you're able to have an overlap of up to six inches to bind the two passes together."
Another benefit of offset drum capability is that the machine has a tighter turning radius for added maneuverability in confined areas.
Simple operation is vital for today's roadbuilders, according to Bryan Downing, global sales support consultant for paving products at Caterpillar. "Caterpillar is continually making product improvements to deliver higher productivity for operators. Recent machine updates have included refinements in machine setup ensuring the best success of operators. Caterpillar continues to focus on making machines and operators more productive with less setup and with automation of features."
Downing also said that the company has been focused on offering smarter compaction energies, operation simplicity, lower fuel consumption and modular technology additions. An available option on Caterpillar tandem vibratory rollers is an Automatic Adjustable Compaction (AAC) vibratory system. With AAC, the operator selects the vibratory frequency needed for the target paving speed, presses the Automatic button and drives a consistent rolling pattern.
Waldschmidt from Case also noted the importance of ease of use and operator comfort. "All construction equipment is becoming more operator- and user-friendly in terms of comfort, which is obviously important when sitting all day on a machine."
A few things to look for in the cab are: visibility to the drums, seat maneuverability for both forward and backward operation, and intuitive controls that enable the operator to easily adjust amplitude and/or frequencies on the fly.
Waldschmidt also said that compactors should have easily accessible maintenance and service points. If a machine goes down on a paving job, it is vital that it can be serviced quickly as asphalt must be compacted at a certain temperature. If there is a delay in service, the job deadline may be at risk.
New features boost productivity in achieving ideal compaction and density
Small mistakes can have an enormous impact on mat quality. Volvo has developed new features to assist operators and help automate compactor functions. "Speed limiters, auto vibration, automatic water spray and impact spacing meters are perfect examples of technologies that help automate tasks that could cause mat quality problems and really help to make compactor functions easier for the operator," said Mark Eckert, compaction product manager for Volvo Construction Equipment. "Our advanced drum vibration system diminishes start-up power consumption for optimum performance."
Bert Erdmann, product manager for compaction at Bomag Americas, said that contractors are opting for machines with intelligent compaction (IC) features to ensure meeting specific densities and smoothness specifications on interstate, highway and roadway projects.
Bomag offers a range of features to help contractors meet specifications. Economizer determines material stiffness and where the roller is in the compaction process. Lights illuminate on the Economizer gauge to let the operator know when optimum compaction is achieved. Erdmann said that these readings can be correlated to nuclear gauge density testing.
Bomag's Asphalt Manager offers self-adjusting drum vibration amplitudes that automatically react to material stiffness. "On a fresh mat, vibration amplitude will be high, but it will gradually change from a true vertical to horizontal amplitude as material stiffness increases, virtually eliminating the possibility of over-compacting," Erdmann said. "You can combine Asphalt Manager with a mapping system to provide documentation of the project."
Erdmann added that proper impact spacing is critical for achieving mat smoothness. "Bomag heavy tandem rollers have a screen that displays impact spacing based off roller speed and selected vibration frequency. This allows the operator to adjust rolling speed to find the sweet spot on spacing that will give the smoothness and productivity desired."
Contractors want 10 to 14 impacts per foot. Smaller diameter drums require more impacts per foot (12 to 14) to achieve desired smoothness and larger diameter drums do not require as many impacts (10 to 12) to achieve smoothness, Erdmann noted.
Downing from Caterpillar said that "intelligent compaction usage and implementation has been growing in recent years. Use of IC methods, compaction meter value (CMV), machine pass count and temperature mapping provide process control measures for the compaction train. These process control measures have greatly improved compaction consistency and uniformity. IC machines can be further enhanced with connectivity options that allow for mapping data to be sent to the cloud and into offices. . . so that near-real-time evaluation can be reviewed. Connectivity also allows two IC machines to share mapping data, which is very important for the echelon rolling patterns that often occur in the initial compaction phase."
"HCQ (Hamm Compaction Quality) is Hamm's intelligent compaction system that maps out rollers' passes by colour and mat temperature for each pass, as well as recording stiffness of the compaction effort on the front drum," said Kowalski.
He added that more and more jurisdictions are requiring this technology to document the consistency of rolling patterns, ensuring proper coverage and compaction. "This results in better compaction effort overall, and the consistency of coverage of the mat for better results. Our exclusive Easy Drive operating system can control our set speed and impact spacing, so each pass is compacted with the same effort."
Eckert said that Volvo's highway-class DD110C, DD120C and DD140C double-drum compactors feature several intelligent features that increase productivity and improve fuel efficiency for a boost in performance on large-scale projects. "These compactors bring together high centrifugal force, heavy static weight and variable amplitude for high-quality compaction."
It is now very common to see compaction meters offered by compaction OEMs, according to Waldschmidt. "These meters measure the amount of rebound at each drum as they go over an area. If the machine passes over an area and does not register any rebound during soil compaction, for instance, that lets the operator know they've hit a bad area that requires attention.
"If the meter is registering full rebound, the operator will know to avoid over-compaction of that area. The compaction meter helps identify areas that will require added attention prior to testing."
Another tool that's gaining popularity is automatic vibration on/off as rolling speed slows. According to Erdmann, "This prevents the potential of divots developing in the mat at the beginning and end of the rolling pattern. For example, as the roller slows upon approaching the paver, the vibrators kick off and automatically start up again after the change of direction and ramping up to rolling speed."
Skilled operator shortage leads to simplified control systems
OEMs have been taking note of the skilled operator shortage that has been a trend across the industry for some time.
"The shortage of skilled operators has led manufacturers to work toward simplifying controls and processes across all equipment lines," said Waldschmidt. One example is automation technology that will adjust the vibration of the drums automatically as it goes along. The operator just has to steer and manage speed at which the machine is travelling.
Hamm's Easy Drive system ensures the consistency of controls across most of the company's rollers to ensure that an operator will remain familiar with the controllers when switching machines. Kowalski also said that Easy Drive reduces the time needed to train operators.
Caterpillar has also focused on updating models for operating simplicity, operator productivity and comfort. Downing said that the AAC system will help operators, whether skilled or newer, be their best.
"At Volvo, we're constantly evaluating machine features that help contractors counter the skilled labour shortage by allowing operators to work more productively, efficiently and accurately," said Eckert. "In terms of control systems, several of our tandem rollers include the optional Volvo Intelligent Compaction system, Compact Assist with Density Direct. Density Direct allows customers to see real-time estimated density values across 100 percent of the mat. Compact Assist also features pass mapping and temperature mapping functionality, as well as data collection capabilities for integration with Veta data management and analysis software."
Jobsite connectivity elevates roller performance
The future of documentation and intelligent compaction lies in the hands of mapping technologies, according to Waldschmidt. Documentation is currently a standard function on many IC systems, displaying the details of every pass for the contractor to demonstrate that the job was performed to spec. With mapping technologies, the contractor can plug in coordinates that match up with the IC documentation and show where passes were, how many were made, compaction levels, parameters and more.
"With the intricate detail of the mapping systems, if there's an area on the jobsite that's not reaching compaction levels, contractors will be able to pinpoint exactly where it is. This is crucial because there could be bad base materials underneath or some other obstruction that's impeding the ability to achieve proper compaction.
"Without the mapping technologies, the operator simply knows that there is a bad patch somewhere on the lift. They may be able to make an educated guess as to where it is, but they won't be able to pinpoint it. With the mapping technology, they can make targeted adjustments or repairs," explained Waldschmidt.
Downing noted that connectivity of IC rollers has greatly improved rolling patterns. "This improvement has happened mostly due to Global Navigational Satellite Systems (GNSS) mapping data being shared to construction back offices for analysis and, more importantly, shared between rollers for near real-time pass count uniformity."
Hamm's WITOS HCQ is a cloud-based system that transfers the data from its IC system to the office. Parameters include pass, temperature and stiffness data. All of this can be viewed in real time from the jobsite or the contractor's office. Kowalski noted that "this is a great tool for quality control personnel with which to monitor roller activity when they are not on the jobsite."
With the WITOS Paving module, the paver communicates with the roller and vice versa. "This is in conjunction with mat temperature monitoring behind the screed with our Vögele RoadScan system and the temperature recording on the roller in its first pass," Kowalski said.
"These help us in controlling the compaction based on temperature differences we see as we roll."
Erdmann said that, at present, the effect of jobsite connectivity on roller performance and design is minimal. "Bomag does offer this type of connectivity through third-party vendors, such as Topcon and Trimble, where rollers communicate with each other to know what areas have already been compacted, avoiding overlapping and over compaction."
In the future Bomag intends to use the cloud to offer roller connectivity through its Bomap app. This recently introduced app uses the GPS on an operator's mobile device to track pass counts, regardless of the brand of roller. This app can be configured to work with and document readings from temperature gauges as well as Economizer and Asphalt Manager compaction values. This also allows the contractor to go back and correlate density and smoothness readings to the values captured by Bomap.
Volvo's compactors are supported by the company's ActiveCare Direct telematics system. ActiveCare Direct does not overwhelm the fleet manager with fault codes. Instead, it analyzes data and sends case alerts in near real time providing probable cause, recommended solution and consequences of inaction. ActiveCare Direct also provides monthly fleet reports.
The evolution of tandem rollers
Exciting new advances in construction equipment as a whole are coming to tandem rollers as well, such as hybrid technology and autonomy.
Bomag introduced its hybrid technology for tandem rollers at Bauma. Bomag hybrid rollers reduce fuel consumption, lower costs and decrease emissions, according to Erdmann. This is particularly beneficial on urban jobsites. Bomag hybrid tandem rollers are currently in production.
Hamm has also introduced tandem rollers with a hybrid powertrain.
Bomag also introduced a fully autonomous roller at Bauma 2019. This concept machine is not yet commercially available. The roller has no operator station, which Erdmann said can be of benefit on hazardous jobsites.
Kowalski from Hamm commented that autonomous rollers are coming, but it will be some time before they are commercially available. "There are a lot of safety features that have to be monitored. A lot of testing is going to be needed before we see them in the field."