Bomag's 600-hp-class cold planers boast reengineered milling chamber for increased performance
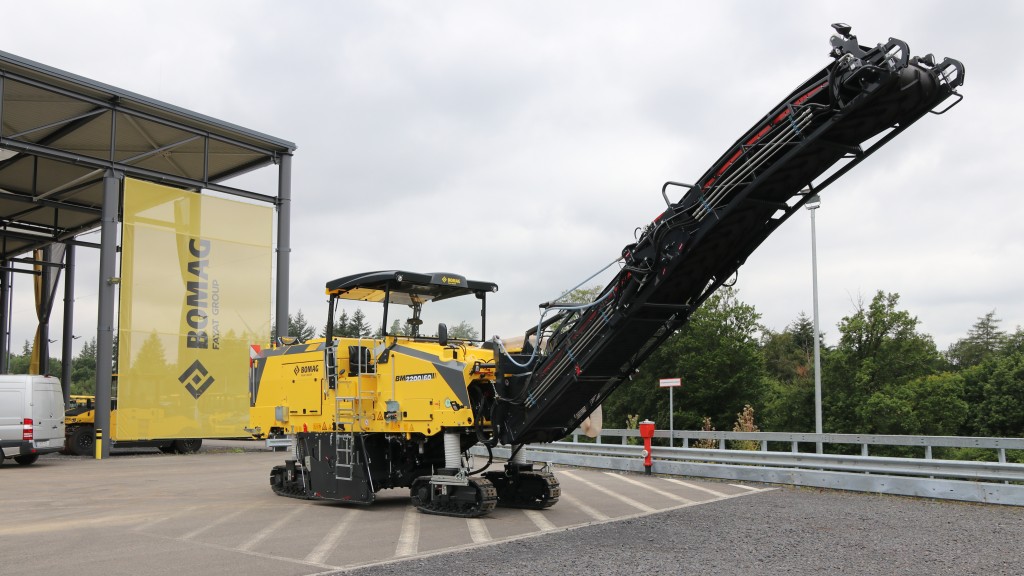
Bomag has reintroduced its 600-hp-class (440-kW) Bomag 2200/60 cold planer with a Tier 4 Final (Stage V) engine and multiple productivity enhancing design advancements. The reengineered milling chamber improves the robustness and design of the front material depressor, resulting in increased performance, lower wear and longer component life. A new inner scraper design and improved compartment seal help to prevent material loss.
The BM 2200/60 offers an 86.3-inch (2,200-mm) cutting width and features Bomag's exclusive BMS 15 milling tooth holder system for superior milling productivity and extended service life by up to 30 percent over other cutting systems. The tapered tooth retainer claw boasts a low-resistance profile that delivers more cutting power with less wear. A quick-change cutting tool design reduces the time required to change a full set of teeth by up to 75 percent over conventional systems.
Optimized conveyor roller placement improves material flow on the new BM 2200/60 for more efficient removal of millings from the cutting chamber. Improvements to the 31.5-inch (800-mm) gathering and loading belts help to increase service life. The system's new integrated dust extraction system helps to improve the working environment for the operators.
New replaceable track pads help to reduce service time and increase milling time in the field. Robust track rollers help to increase drive system durability. An 11.8-inch (300-mm) track width and 67-inch (1,700-mm) track length provide excellent traction when milling at depths reaching 12.6 inches (320 mm).
New hydraulic hose placement and routing improve service life, reduce thermal aging and increase machine uptime. Integration of smart cylinders that provide internal measurements remove external sensors and the inherent risk of damage. An integrated service platform simplifies and significantly reduces the time for daily maintenance procedures, further improving machine uptime.
Contractors can also choose the 600-hp (440-kW) class Bomag BM 2000/60 model with a 78.7-inch (2,000-mm) milling width and all the same series design improvements.