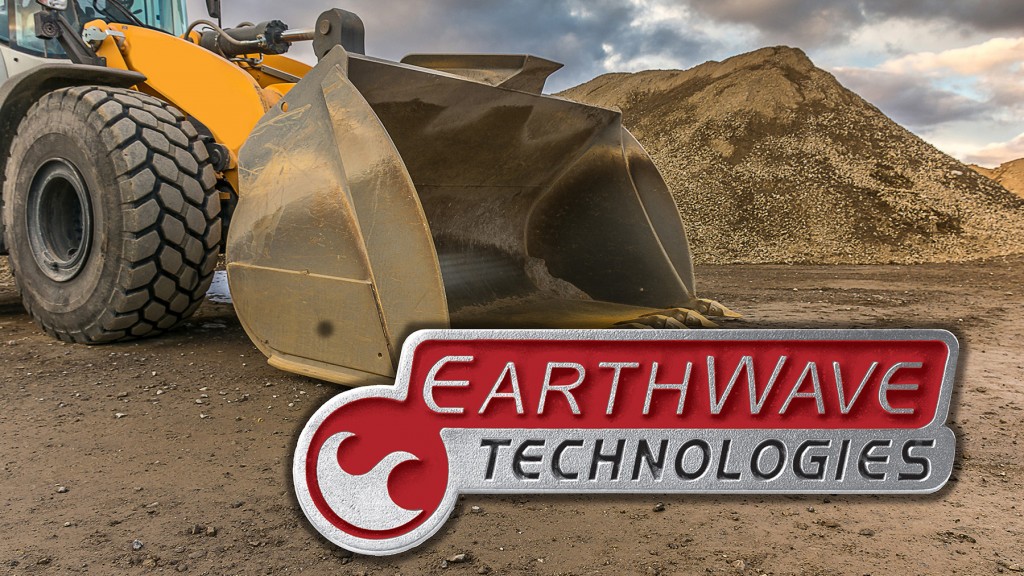
Earthwave introduces their new Construction Management Solution (CMS), a wireless telematics system developed specifically for "yellow iron" construction projects. The new GS-364 hardware platform connects directly to the computer/bus of off-road equipment, delivering real-time data from pavers, excavators, loaders, dozers, and virtually any other construction tool. Actionable data, including hour-meter readings, RPMs (is machine idle or working), fuel usage, temperatures, asset auto-assignment to job and more, is delivered from the jobsite to a phone, tablet or laptop. This allows users to monitor, manage, and optimize equipment, personnel and workflows, streamlining projects and enhancing profitability. Earthwave's Construction Management Solution was developed specifically for the heavy construction industry and is ideal for off-road construction projects of all sizes and types.
A full complement of reports allows users to instantly see what is happening in the field and take corrective action as needed. A Current Fleet Status Report replaces the magnetic boards/grease boards which can quickly become outdated. Real-time tracking shows what equipment is at each job, and its status (running, shut-off, in transit, etc.). A current status by equipment type shows where all equipment of a certain type is (dozers for example).
A Breadcrumb Trail shows the detailed location information for the machine for the day selected. Each time the unit updates (variable from 1 to 5 minute intervals), the packet shows the location of the machine and the reason for the packet (Engine On, Engine Running, Engine Off, etc.). A Geozone is provided to automatically track the machines activity within that Geozone, and when it arrives and leaves the Geozone.
A Maintenance Due Report shows the number of run-time hours before maintenance is due for all equipment. Areas shaded in red indicate that service is past-due, while areas shaded in yellow indicate that equipment is within 36 hours of its next PM. Services can be tracked by hours and/or miles.
Weekly reports are also automatically generated to provide up-to-date information on projects. A Weekly Productivity by Project report provides a detailed, side-by-side comparison for all equipment on a selected project for the week. This is especially useful in determining how well a project is performing, and if any equipment can be better utilized elsewhere.
A Summary Productivity Report by Project provides a summary of all equipment on any/every project for a selected period of time. The date range can be modified to provide weekly, monthly, YTD, project-to-date or any other date range desired. A pie chart reflecting the percentages and totals of idle and productive (time equipment is running and not idling) time on all equipment on that project is automatically generated when the report is run. A bar chart can be generated to show the percentages of a piece by piece basis.
Armed with this accurate and timely information, users can make better decisions to impact the productivity and profitability of their construction projects.