Technology keeps workers safe, equipment running and projects on schedule in remote locations
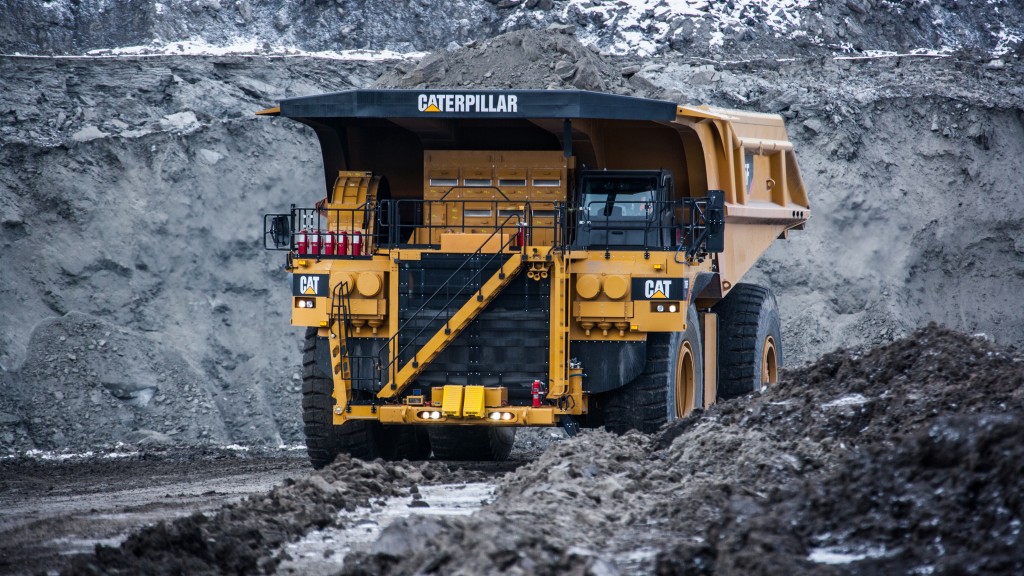
High demands, tough terrains, challenging weather conditions. Operators work across a vast array of conditions, so not only do they need to know how to use a variety of equipment but they also need the skills to operate that equipment in various environments, temperatures and conditions.
Construction outside of city centres has been on the rise in recent years due to the resource boom and an increased demand for new infrastructure. These remote locations have their own set of unique challenges. Accessing the right equipment at the right time can have a considerable effect on productivity, maintenance costs and optimization and can be very demanding on equipment and operators.
But technology is helping to keep workers safe, equipment running and projects on schedule under these challenging conditions.
Planning jobsites and maintaining equipment
Infrastructure work, fixing or maintaining roads, sewer and water – all common construction jobs in any location. Add in -40 degree C temperatures, remote northern locations only accessible by road at certain times of the year, frozen ground and at times very little daylight, and you get a whole new set of circumstances and challenges, making diligent planning and precise logistics essential.
Keeping equipment and operators productive and on track in extreme conditions can be a tough job. Equipment needs to be properly prepped and maintained while on site. Repairing a machine after failure can be costly, particularly in remote locations where fuel, parts and engineers are not easily accessed.
Equipment is especially prone to breakdowns in severe cold where metal becomes brittle. Excavation and earthmoving of frozen ground can take longer and it is extremely hard on both the machine and attachments. Downtime needs to be managed to perfection – the longer a machine is out of use or idle, the greater the impact on the project from a timing and cost perspective.
This is where equipment telematics can help, ensuring machines are running efficiently and providing real-time intel from fleet hours and location, equipment availability, idle time and fuel consumption to scheduled maintenance. Once analyzed the data can alert equipment managers of fault codes and many other aspects of operation including idling hours, start and stop times, fluid analysis, and equipment inspection information.
Giving owners and operators a full picture of how machines are performing, identifying problems and errors before they become costly, leading to improved performance and reduced maintenance.
Remote fleet monitoring and the right equipment partner can help maximize the life and value of equipment and keep maintenance on schedule. Remote monitoring connects all the machines in the fleet via telematics and provides recommendations on maintenance or other issues that need to be addressed. Equipment technicians monitor the machine 24/7 and distribute parts prior to service checks to ensure they arrive in time for scheduled maintenance.
Keeping equipment productive with the right technology
It's not just the machine and the operator that benefits from technology. Increased accuracy and greater efficiency is gained by the use of technology throughout the entire job. All projects start with surveying – gathering data and inputting information into software programs, to design and build the project.
Drones can be used to fly the site to capture images that are tied to ground control points and GPS coordinates, which are then stitched together in software to create 3D images of the site used to analyze progress and material usage.
The vision of the project starts here – designs are created digitally in software before a machine ever enters the site. Software programs are used to schedule various stages of the projects, monitor progress and timelines which can be reported back to clients.
Machine control remains one of the most common technologies being used on construction sites today whether it's installed at the factory or aftermarket. Satellite data can pinpoint locations and cut grade at the blade, providing efficient measurements, greater safety and an almost immediate ROI. New developments in the past few decades offer a huge benefit to earthmoving applications in some of the most remote and challenging terrain – 3D technology gives a detailed and accurate view of terrain for operators and on-board connectivity increases communication between the operator and site manager and keeps them appraised of the work, any issues and progress.
Safety benefits
Technology is not only transforming the way construction companies are able to execute projects, but it also has a real impact on safety on site. Investment in safety related technologies is ensuring workers stay alert and focused while operating a machine and site managers are aware of how to mitigate any potential hazards. In-cab technologies can monitor eye movement and head pose in real-time, wearable smart-bands help operators and site managers understand the connection between operator fatigue and accident risk on and off the job by converting information into data and analyzing patterns.
Next generation machines come equipped with backup and side cameras straight from the factory for increased safety. Another common feature is seatbelt indicators, used to alert operators to buckle up to keep them secure.
With technological advancements in surveying, like drones and GPS rovers, the number of survey people on the ground on a jobsite has been drastically reduced. A task that traditionally took two or three people can now be done with one.
Technological advancements lead to better operation
Technology is ensuring operators can do their job better, safer and faster. And it's even more important for construction companies operating in Canada's harshest conditions and most remote locations.
Reliability and durability is taken very seriously when designing a machine. The best equipment is rigorously tested to operate just as well in the hot Californian desert as the sub-arctic temps of northern Canada.
By combining the right equipment partner with site logistics, maintenance programs and equipment monitoring support - even the most challenging projects can stay on time and on-budget.
Nathan Duncan is Regional Technology Manager at Finning Canada.
Company info
16901 - 109 Avenue
Edmonton, AB
CA, T5P 4P6
Website:
finning.com
Phone number:
888-346-6464