HCSS Safety software takes the paperwork out of safety planning
Breaking through the paper jam that can cut down on safety plan buy-in is becoming easier
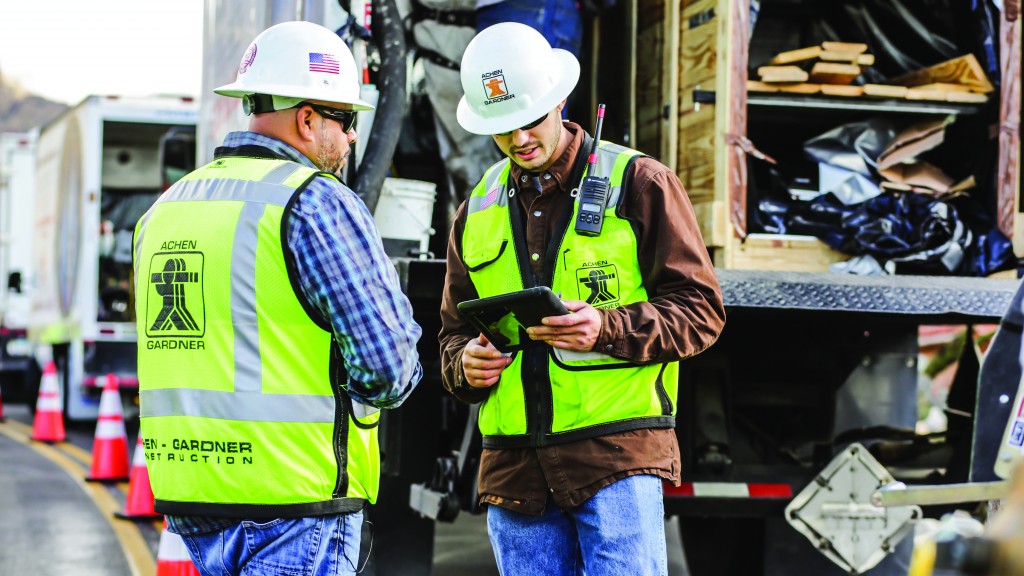
On today's construction jobsites, the way in which contractors and their employees approach safety has changed dramatically. Where safety was often an afterthought in the past, today there is a strong focus on making it a part of workplace culture – an overlying piece of every day's work that ensures everyone goes home safely at the end of every shift.
The challenge with establishing and expanding a safety culture on heavy equipment jobs has rarely been a lack of interest, but a lack of time to deal with the inevitable byproduct of a well-designed safety plan: the documentation. With more and more construction software companies bringing solutions for safety onto the market, though, the opportunities for growth in safety planning are expanding.
One problem with the traditional safety plan developed by many organizations is that it's done at a high level by a safety director, and then is implemented from that high level. Stacey McCroskey, product manager for HCSS Safety, said that meant that there was less buy-in with workers on the ground.
"The safety is always high when the safety director is on a construction site, and then that tends to diminish when they have moved on to the next site," she related.
Those plans are often well rooted in the office, which comes - especially in construction companies, which are often still catching up with their peers when it comes to technology - with a lot of paper. When an organization has been using paper documentation as its basis for years, it's hard to encourage a move towards less cumbersome and more functional approaches, McCroskey said.
"Paper's still the primary competitor in the industry because companies are still saying ‘We've been doing this for four generations, I don't know why you're trying to make us change now,'" she said. "The primary weakness of paper is that when you get a pile of paper in front of you, how do you know which piece is going to tell you where the potential next problem is?"
When it comes time to seek out records of specific activities taken under the company's safety plan, paper becomes even more of a problem, simply through its volume.
"If an incident happens or they need to pull paperwork for some sort of litigation, you've got boxes and boxes of banker boxes in a warehouse somewhere that you need to search to find the one piece of paper to show you did hold a safety meeting on a particular topic," McCroskey said. "The amount of paperwork just gets crazy... you've got these mountains of paperwork that they're trying to maintain."
Depending on the company, there are any number of activities that need a paper trail, from toolbox safety talks to pre-work site inspections or equipment inspections.
"It can get quite complicated. Your subcontractor may be working multiple different jobs for multiple general contractors that each have their own set of forms," McCroskey said.
It's the constant need to stop and fill out paperwork that helps sell electronic systems and software solutions to reluctant construction industry members, she said.
"It eventually saves you time – you won't need to fill out two pages of paper to do an inspection, and instead you're just clicking on buttons. It frees up your safety person, who doesn't need to chase around paperwork – because a lot of time the paper gets stuck in a foreman's pickup, gets stuff spilled on it, or gets crumpled up," she noted. "I can't say that all of them are excited about moving to technology and off paper. Once they start using it, they find they love it because it does save them time."
Solutions like HCSS Safety take the paperwork out of the equation and offer the entire company flexibility and mobility, from the work site to the office. In addition, they offer users an easier way to conduct the safety activities that are part of the daily routine and greater opportunity for head office to analyze the efforts over time.
On the jobsite, crew members are able to access HCSS Safety through an iPad, with a variety of functions, McCroskey said.
"We have a library of prepared safety presentations or toolbox talks, so the foreman pulls up the talk and it has their talking points ready for them. They can take a picture of the crew or have them sign off with their finger on a signature pad... that is in a manager's system back at the home office within five seconds," she said.
Having a portable interface makes the toughest part of implementing a safety program – the confirmation that it's been delivered – easier. It also helps with transition for staff who may not be comfortable with technology.
"A lot of times when we go out and do field training with the foremen, a lot of them have never held an iPad or had smartphones," McCroskey said. "We try to keep things simple on the field app, but the great thing is that once you do get the field involved, you raise the level of awareness and now they're paying attention to safety, even if it's just in the back of their minds."
Once meetings and inspections begin using the mobile interface, head office gets another benefit: more data, and more analytics that can help with monitoring effectiveness of the current safety structure in the company.
"You can look at leading indicators to try to predict where there might be problems, or where you need additional training," McCroskey described. "Your personnel at the home office who see the data coming in know who's doing what and what's going on in the field – they have a real-time pull of data from the field, which is important. If they run the analytics, they can catch problems before they become a major incident. Over time, that helps them lower their insurance premiums."
Adapting a company to use the new solutions is generally fairly easy, especially when everyone buys in to the lighter paperwork load. Generally, companies will send teams to HCSS, for example, and spend a week being trained on the new system, how the software operates and how to manage the data, among other things, so that they can return and train others. HCSS will also send trainers to work with foremen and others on the jobsite.
Both large and small construction companies are taking up software solutions for their safety plans now, McCroskey reported. While the big players have always had safety programs in place, the smaller operations have sometimes lagged behind.
"I think with smaller companies part of it may be the introduction of millennials into the workforce – they expect a bit of technology," she said. "We're definitely seeing smaller companies start to develop safety programs, even if they're just really small – at least it's something."