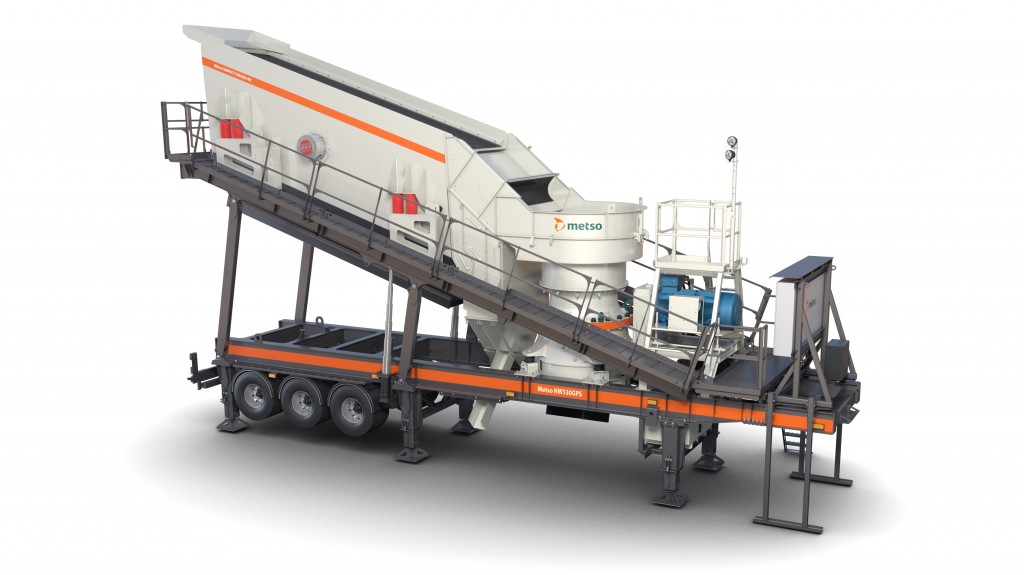
Metso is introducing new higher capacity models to its popular wheel-mounted Metso NW Rapid series. In addition to a bigger jaw crusher model, the NW Rapid units are now also available with a variety of robust cone crushers, including the first model with the MX crusher. Easily transportable using standard prime movers, over a thousand NW Rapid models have already been sold into aggregates and C&D recycling applications.
According to Metso, planning a crushing and screening process can typically take months. Additionally, it's often difficult for aggregates producers and recyclers to move their largest equipment from site to site. NW Rapid is the market's first wheel-mounted crushing unit that can be delivered in standard containers from the factory as well as easily moved from one site to another using standard prime movers. The flexibility of the concept allows producers to profitably offer their customers contracts of various sizes.
Besides portability, other advantages of the NW Rapid models include quick set-up and best-in-class production capacity. NW Rapid has been designed so that it can be set-up and dismantled in 24 hours. The 11 predesigned layouts make planning the crushing process significantly faster. The solution consists of modules that can be used to create a variety of combinations as needed.
"A large share of our customers supply aggregates for public infrastructure projects that can last from a few months to a couple of years. Depending on the project phase, our customers must have the ability to offer also very high capacity. The new NW Rapid models enable production capacity to temporarily be increased up to 500 tons per hour, which is equal to the capacity of a fixed plant. Because of the flexibility, customers can better respond to short-notice orders and can accept contracts that couldn't be carried out with the traditional fixed solutions," said Julius Mäkelä, Metso's Director of Portable and Modular Solutions.
The NW Rapid series models are electric-driven and they have Metso's IC Series crushing automation as a standard feature. Additionally, the NW Rapid units can be connected to the Metso Metrics remote monitoring service, which allows central monitoring of the entire crushing fleet's production and energy consumption.
New Rapid models spark interest around the world
The NW Rapid series is ideal for producing high-quality end products with multistage crushing and screening units. Now, the NW120 Rapid jaw model will be joined by the screen-equipped NW330GPS and NW300HPS cone crushers. The NW4MXS is the latest introduction to the series and brings the MX4 Multi-Action cone crusher, launched in 2017, to the integrated crushing solution for the first time. Serial production of the NW4MXS will start in the second half of 2019. For other models, factories are already working to bring new machines to customers globally.
According to Metso, the NW Rapid series has sparked great interest, and more than one thousand units have been sold since 2015.
"The demand for Metso's crushing and screening plants has been growing in recent years, and, in fact, NW Rapid has quickly become one of our most popular solutions especially in fast-growing markets like India, where urbanization and huge public infrastructure projects have accelerated growth of the aggregates sector. Because of the flexibility and cost-efficiency, NW Rapid is of interest also in several other markets: the equipment has already been sold to more than 20 countries," says Renaud Lapointe, Senior Vice President, Business and Product Management for Aggregates Equipment at Metso.