Texas-based sand and gravel company relocates its CDE wet processing plant to new site to optimize return on investment
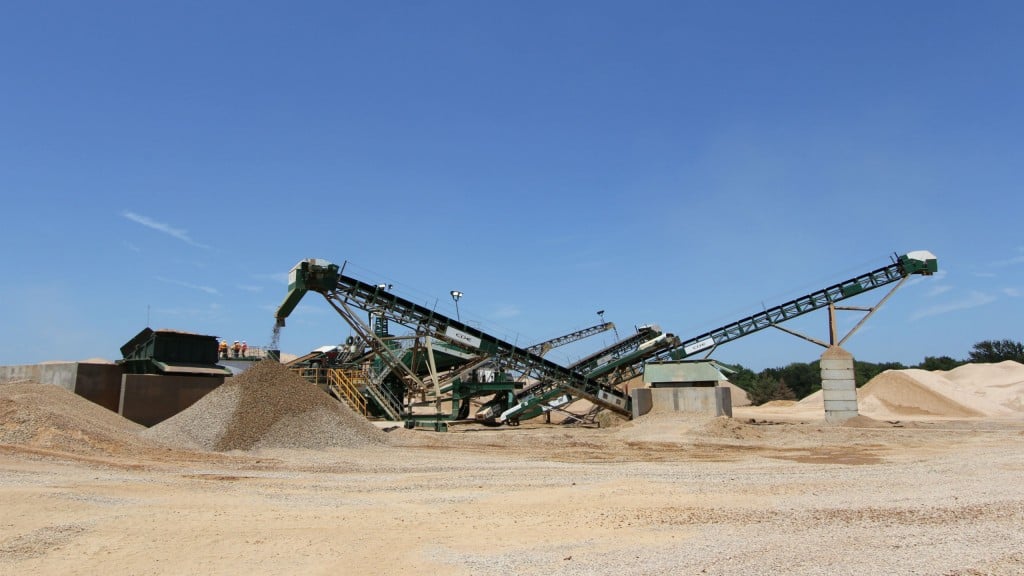
Texas-based Metroplex Sand & Gravel company has been enjoying the benefits of the CDE modular approach to wet processing equipment. The company has recently exercised the option to move its sand washing plant to a new site at Resolve Aggregates in Ravenna, Texas, once its production objectives were attained at its initial Fort Worth site after 16 months.
The full CDE Fort Worth installation was disassembled, containerized, relocated and installed by Metroplex employees in just 11 working days, to then be re-commissioned by CDE at the newly acquired sand deposit in Ravenna, Texas, near the Red River.
The background
Keith Newell, President of Metroplex Sand & Gravel, said: "We discovered th e CDE technology at ConExpo 2014 in Las Vegas. The company was launching its new M4500 wash plant, designed to meet the needs of the North American market with a capacity of 450 tons per hour."
The CDE team explained how combining feeding, screening, sand washing and stockpiling on a compact chassis allowed for the fast deployment of the M4500, which would allow us to set very competitive production schedules.
Newell adds: "Shortly thereafter, a member of the CDE team visited the GS Materials Plant in North Carolina, which featured a CDE 300 tph turnkey wet processing solution. We were immediately impressed by the plant's ability to manage gradation and silt cuts, with the option to produce golf course spec sand in a single pass. With conventional classifying equipment and sand screws, this is difficult to say the least!"
Metroplex also had the opportunity to discuss and witness the effectiveness of the modular model and recognized the potential of this approach for the company. Owning various sites, the ability to move a plant to a different location when relevant was considered an asset in terms of return on investment.
A more detailed consultation with CDE provided efficient solutions to answer the client's primary requirement to produce in-spec finished products in a single pass, with a reduction in both the environmental and the plant footprint, with a focus on decreasing the height of the installation.
In 2015, following a process of co-creation with Metroplex to further meet its production requirements, CDE designed, manufactured and delivered a complete five-machine wet processing solution comprising the M4500 modular wash plant, the AggMax portable logwasher, the Counter Flow Classification Unit (CFCU), an EvoWash fines recovery unit and an AquaCycle thickener.
The process
The +3-inch material is delivered to an oversize stockpile from the top deck of the rinsing screen on the M4500 with the material between ¼ inch and 3 inches transferred to the AggMax. Once the gravel has been scrubbed to remove clays, it is being stockpiled into 3 product grades: 3/8 inch minus, 3/8 inch to 1 inch and 1 inch to 2 1/2 inches. The 1 inch to 2 1/2 inches is conveyed from the screen to a Cemco Model 80 vertical impact crusher where it is crushed to sand and smaller gravel particle sizes. The AggMax also includes a dewatering screen at the rear which accepts the lightweight organics floated off from the gravel fraction and dewater these before stockpiling in a product bay underneath the machine.
The minus ¼-inch material is then sent to the sand washing element of the M4500 which is configured with a dual pass cyclone arrangement. The sand material is first delivered to two 25-inch cyclones where the first separation occurs. The material is then discharged from the cyclones to one side of an A-Series VibroSync split dewatering screen before the coarse sand is stockpiled via a radial stockpile conveyor.
A selected proportion of the material passes through the dewatering screen to the fine sand sump and is then sent to the Counter Flow Classification Unit (CFCU), which further facilitates density separation by using an upward flow of water to carry lighter particles up while allowing the heavier particles to fall to the bottom of the CFCU tank. The material from the bottom of the tank is then delivered to the second side of the split A-series VibroSync dewatering screen and a 100 mesh to 18 mesh fine sand product is stockpiled via the integrated M4500 stockpile conveyor. Meanwhile the lightweight material from the CFCU is delivered to an additional EvoWash 71 sand washing plant where a 200 mesh to 100 mesh cushion sand product is stockpiled.
The plant also includes an AquaCycle A600 thickener which accepts all the waste water and minus 200 mesh fines which are dosed with flocculants on entry to the tank. This facilitates the settlement of the fine particles to the bottom of the thickener tank while the clean water overflows the peripheral weir and is recycled to the wash plant. The AquaCycle recycles up to 90 percent of the process water, which is ready for immediate re-use by the system. Water recycling presents substantial benefits when environmental considerations come into play, but also as the need for settling ponds, and therefore the time spent on their maintenance, is significantly reduced.
Keith Newell adds: "The modularity and compact foot print of the M4500 is an obvious plus and the time it has all taken to come together has been shorter than we would have thought possible.
"The quality of the equipment design and the strength of its manufacturing are truly remarkable as well, as is the precision with which the plant fits together. Perhaps most importantly, the AquaCycle thickener greatly diminishes our fresh water requirements. Our current plant requires 6,000 GPM; the M4500 – although it uses approximately 2,600 GPM – requires only 300 GPM of new water."
The relocation
The CDE methodology is based on a tailor-made service to clients, who are invited to collaborate in the development of their installation. This means that each wet processing solution is created with the client's requirements at its core. In the case of Metroplex, a modular approach was required to ensure that the high efficiency, built-to-last installation would be used throughout its lifetime by relocating it from one site to another, therefore optimizing the company's return on investment.
In 2017, at the end of the economic life of the Fort Worth quarry, Metroplex decided to replicate the successful production model at its newly acquired quarry in Ravenna, 100 miles from Fort Worth. At the new site, operating as Resolve Aggregates, the plant is currently producing in excess of 100,000 tons-per-month of C33 concrete sand, #8 pea gravel, #57 gravel, C144 masonry sand and asphalt sand. When required, the plant also accepts crushed material directly to the feed boot from a transfer conveyor.
The present and the future
Kevin Kelly, President for North America, CDE said: "The CDE equipment range has been developed to meet the growing production needs of today's materials production industry. It introduces cost savings without compromising on quality and capacity.
"Each installation is designed to individual requirements, built and tested in our assembly facilities, to then be containerized for fast delivery and quick setup on a minimal footprint.
"The M4500 wet processing plant, as well as its bigger sister the M5500 were specifically engineered with the North American market in mind, to provide solutions that pack a strong production punch whilst reconciling environmental requirements and the demand for powerful, reliable and high-tonnage equipment.
"Watch for the arrival on the North American market of the new CDE Combo XL, the latest addition to our Combo range that incorporates feeding, washing, grading, water recycling and stockpiling in one machine.
"Launched at Agg1 in Houston earlier this year, the Combo XL is designed for the production of manufactured sands and is set to revolutionize the North American market. With a capacity of up to 250 tons per hour and up to 90 percent of process water recycled and immediately ready for re-use, the Combo XL ticks all the right boxes for operators looking for high volumes of quality materials that are ready for market in record times.
"With the option to produce up to three materials of even consistency and in spec every time, the new CDE Combo solution presents significant added benefits compared to existing systems. We foresee the marriage of a high efficiency cyclone-based processing plant and an unrivalled water management system to be extremely successful in the region."