Aggregate producer's Trimble Loadrite scales are consistent and accurate in tough conditions
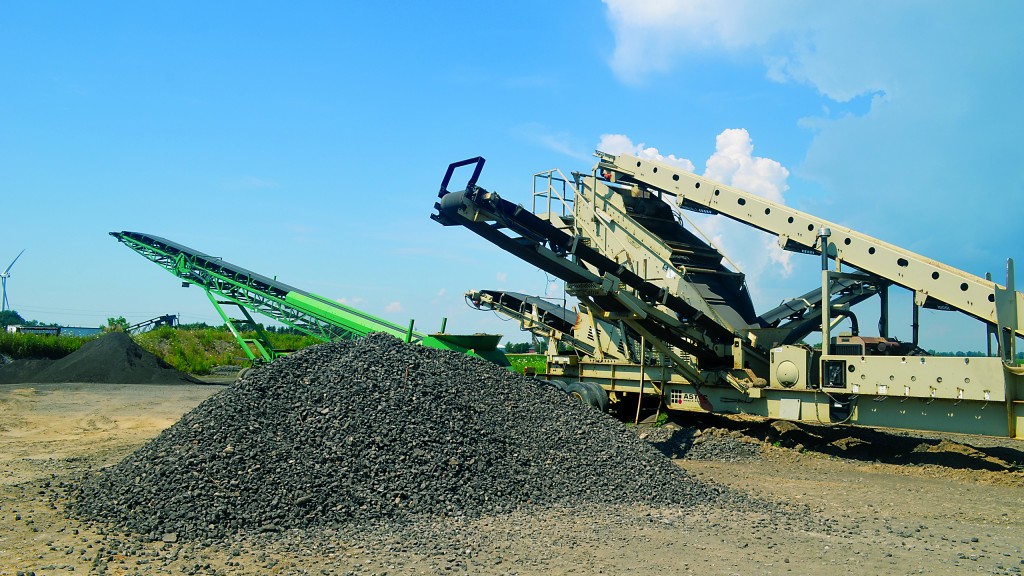
Located in the town of Merlin, in southwestern Ontario, Sykes Trucking & Aggregates Ltd was founded in the 1970s by entrepreneur Ed Sykes and is now owned and operated by his son, Don Sykes. About 10 years ago, the company purchased Orford Sand & Gravel Limited, located in the neighboring town of Muirkirk. Today, the aggregate production company produces sand and gravel and has a screening plant to develop its own custom sand mix and asphalt sand, which meets Ontario Provincial Standards for asphalt.
Sykes Trucking & Aggregates is a loyal and longtime user of Trimble Loadrite scales. Ed purchased the company's first Loadrite onboard loader scale in the 1980s, and since then the company has added two Loadrite X2350 excavator scales and five Loadrite L2180 wheel loader scales. Sykes Trucking has relied on its local equipment dealer, Silver Top Supply, to install and calibrate the scales. Don has the company's platform scale certified once a year and takes pride in the fact that his team still uses the original loader scale his father purchased in the 1980s.
"I am impressed with how well these scales hold up even in rough weather and a tough environment," said Don. "They are extremely consistent and just downright accurate. The only time we have Silver Top out here is when we hit a branch or something with our bucket and one of our sensors goes out. They are great about coming out to help us in those cases, but other than that Loadrite scales just work."
Operators use the Loadrite L2180 onboard scales on loaders across the aggregate operation, moving material from the sand pits to the screener for processing. Don explained that the L2180 scales are essential for his business because they deliver accurate and consistent payload measurement for every single load of material moved. The onboard scale works by using a rotary position sensor to continuously monitor the boom position over the entire lift. This allows the system to take multiple measurement points, and in doing so improves accuracy because variations in weights are calculated, averaged out or even discarded if they are outside tolerance levels. This brings the overall accuracy of the Loadrite scales to within +/-1 percent or better.
Don likes that the onboard scales allow for consistent loading from machine operators, regardless of experience. It also helps avoid overloading trucks and possible fines by ensuring trucks are loaded to the correct value. He explains that his operators like that weights can be calculated and printed directly from the loader, which eliminates the need to log weights manually.
"Our Loadrite scales save a lot of time because operators lift each load, weigh it, and can instantly record and print accurate weights," said Don. "That saves time getting out of the loader and onto the platform scale. And, if a customer wants a specific amount of stone, we can show them right there in black and white they're getting exactly that. That gives a lot of confidence and credibility to your business."
Looking to expand his aggregate operation, the company purchased a 225-acre parcel of decommissioned railroad lines outside West Lorne, Ontario. Officially known as CN Mile marker 118-138, this section of double-track railroad was formerly part of the Canadian National Railway and dates back to the early 1900s. The bed of the track and rail is comprised of railway ballast and other crushed stone material. This material was selected as the track bed because of its ability to provide drainage and support significant loads carried by railcars. Railway ballast is generally produced from granite, trap rock, quartzite and limestone.
Don explained that he purchased the land and railroad line from the local municipality, with plans to dig it up and reclaim and recycle the old railway track and materials. He believes using recycled materials in this way is particularly important in this region of Ontario because there is a shortage of aggregate base material in the area due to increased demand and growth in the area.
Because of erosion and the compaction of material, the excavator operator must first dig down approximately 3.5 feet to the track bed to excavate the material. He then uses the X2350 excavator scale to precisely weigh each load of rock, which is then loaded on a truck and taken to the Sykes plant for processing. The Loadrite excavator scale delivers bucket-by-bucket optimization of the load-out process, making sure each truck is loaded to its full capacity and weight is recorded accurately every time.
When working at full capacity, Don estimates that the crew excavates and moves approximately 2,200 tons of material per day. After nearly seven years of excavating the railroad track intermittently − generally working during periods of reasonable weather and when business is slower − he estimates his crew has recycled about 80 percent of the existing track and has about two more years worth of track left. Don appreciates that the X2350 excavator scale allows his operators to track material movement in real time and to optimize loadout operations, even in a remote area, for every bucket and every truck load.
"Along the rail line, there are grain elevators and scales that we could have used to weigh our rail material, but that overtime would make the project cost prohibitive," Don said. "They charge $7 to $10 per weigh, so that would add up really quick to hundreds of dollars per day. Over weeks and years of doing that, it just wouldn't work. For the stone recycling work we're doing here, you couldn't ask for anything better than the Loadrite scale."
Once material is excavated, weighed and loaded into the trucks, the railroad track material is then run through the crusher, processed and turned into 2/3-inch and 3/4-inch crushed clear stone. Sykes then sells the clear custom stone for use in landscape and other applications.
"With accurate, mobile weighing from Loadrite, we're able to cost-effectively offer this unique, reused and recycled stone that's serving another purpose," Don said. "That's big in this area where this kind of material is limited. We're also cleaning up the area and reusing a part of our Ontario history, which is pretty cool."
Company info
935 Stewart Drive
Sunnyvale, CA
US, 94085
Website:
heavyindustry.trimble.com/en/loadrite-payload-management