Rotochopper launches 1,000 horsepower B-66E electric horizontal grinder
New dual-motor drive option designed to reduce operating and maintenance costs compared to single-motor drive
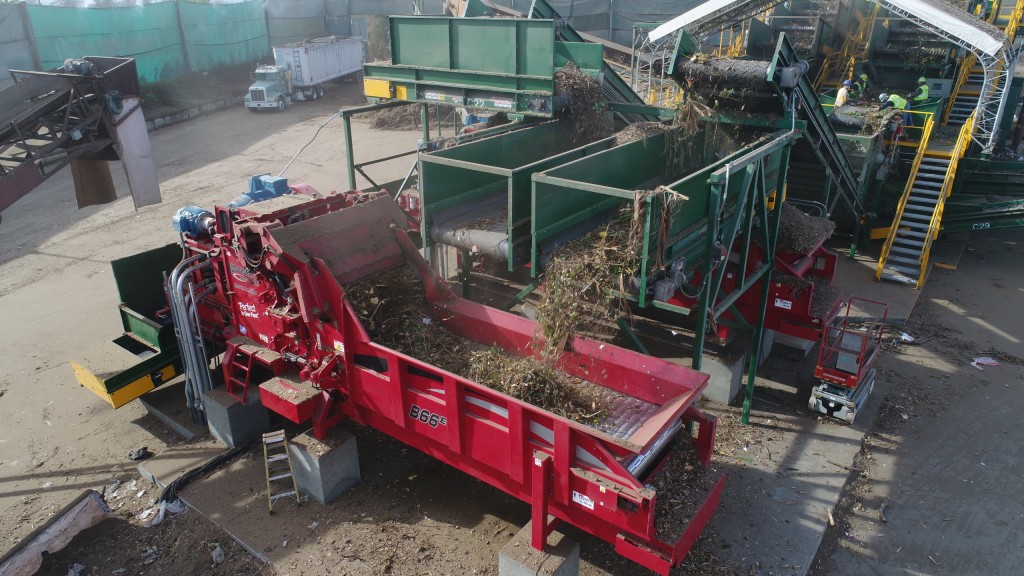
To help customers process increased volumes of waste materials, Rotochopperhas introduced a new 1,000 horsepower dual-motor drive option for the B-66 E electric-powered horizontal grinder. The dual-motor drive is designed to reduce operating and maintenance costs compared to a single-motor drive, as well as minimize amperage surges at start-up.
Due to the sourcing challenges of bigger electric motors, grinder owners have often opted for lower horsepower. "The dual motor drive brings the best of both worlds," said de St. Aubin. "The convenience of smaller motors along with the production capacity of higher horsepower."
Two dual drive 1,000 horsepower B-66E electric horizontal grinders were successfully installed at a waste processing facility in California the end of last year to process sorted green waste. They needed greater production capacity than our current configuration could provide and chose the dual drive motor over a single motor based on the recommendation of the Rotochopper engineering team. The dual-drive motor increases efficiency and reduces maintenance costs.
Benefits of a dual motor drive over a single motor drive include lower start-up amperage surges and lower repair costs in the event of downtime. Major downtime is rare with industrial electric motors. Yet should a breakdown occur, the dual motor drive decreases the lead time and cost of replacement parts compared to a single larger motor.
"The 600 to 700 horsepower range has been a great fit for customers from a broad range of industries," said Rotochopper CEO Art de St. Aubin. "But the growth in yard waste composting, municipal waste, and other high-volume markets is driving increased demand for bigger electric grinders with higher horsepower."