CEMCO celebrates 50 years of growth and success
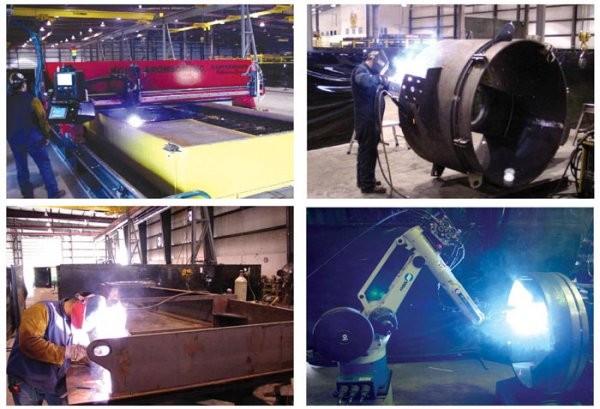
When Mason Hise purchased a fledgling repair company in 1962, one could not imagine that it would grow into a worldwide leader in vertical shaft impact crushing technology.
“There was never a conscious decision to become an equipment manufacturer,” Neil Hise, Mason’s son and now President of CEMCO said. “We were just working hard and trying to solve problems. We didn’t let anyone tell us there was something we couldn’t do.”
That work ethic and ingenuity transformed CEMCO from what started as a service and repair business into a global manufacturing company that now occupies a 144,000-square-foot manufacturing facility that solves crushing challenges in 27 countries across the globe. The company is now on its third generation and continues to focus on solving the unique challenges of the mining and aggregate industries while leveraging its experience to reshape the recycling and cement industries as well.
In 1962, Mason Hise learned that a company by the name of Crusher Service Company had been listed for sale. Filled with the entrepreneurial spirit and motivated by a desire to provide a more stable life for his family, he decided to purchase the company. Equipped with rugged machines, an ever-increasing demand for repair services, and an even greater amount of sweat and determination, Mason and his son Neil provided crusher repair services to customers in a 400 mile radius around Albuquerque. Using trucks and portable, manual-welding rigs, the Hise family found the hours long and the work plentiful. Rose served as the accountant and office manager, handling all the details necessary to support the growth of this fledgling business.
It was demanding work using unsophisticated equipment, and requiring the men to travel endless miles on dirt roads to service the aggregate industry day and night. Equipped with only hand tools and welding rod, they disassembled, welded, straightened and reassembled crushers countless times.
Facing the abrasive hard rock common to the Southwest, roll crushers were in constant need of repair and those repairs often lasted only a week before additional service was required. Mason and Neil believed there had to be a better way to crush rock into chips and sand. In May of 1965, they had just wrapped up an 18-hour shift of welding hard face repair to a roll crusher that was providing material for the Heron Dam project near Chama, N.M. The roll crushers were in need of continuous repair, sparking through the night while they attempted to crush the hard New Mexico granite. As the pair laid in their sleeping bags staring at the starry night, they agreed there just had to be a better way.
In their quest for a solution, Neil and Mason discovered existing vertical shaft impact crushers, but quickly realized their design failed to offer a practical solution. The castings simply weren’t sound enough to handle that hardness of material. The two options available, the Tornado and Simplicity D’cintegrator, consumed a significant amount of parts and eventually self-destructed.
“There are few things harder than New Mexico granite,” Neil said. “It’s why our repairs would only last a week. We knew we would need to find the right design and material to create an alternative option.”
Mason and Neil asked Les Edminister, owner of West Coast Alloys, if he could construct a new style of crusher wear parts from the same alloy as the hard-face welding rod he provided for the Hise’s repair shop. Les didn’t hesitate at all, and quickly brought in other management at the foundry to tackle the challenge. Meanwhile, Neil took pencil to paper and, using his education and experience, began drawing bearing cartridges, shafts and crushers in an effort to change the design concept that existed to a more practical solution.
In 1966, Neil sketched a shaft design and took it to a local machine shop. He asked the crew to build three shafts: one for the concept, one back-up in case the original broke and a third to be used in a second crusher if there ever was ever going to be another. Two weeks later, he returned to measure the results; all three were different sizes.
Realizing that success required consistency and accuracy, Neil and his team purchased a used lathe and began making the parts themselves. That’s how CEMCO began its transition into manufacturing.
“Looking back, I have to laugh,” Neil said. “That lathe we bought was likely a century old, but it took all the money we had. In the end, it got the job done.”
Before long, the team was building keyways and constructing bearing housings. In 1986, when CEMCO exhibited at its first industry tradeshow, realization struck. CEMCO was no longer a service and repair company. It had evolved into a small, yet full-fledged manufacturing company and would one day be a global solution provider.
While it’s truthful to say CEMCO’s production doubled within a year of making its first crusher with West Coast Alloys, selling a single machine one year and two the next doesn’t make a company a world-known manufacturer. It provided a good start for future success, though.
That first crusher still operates today in northern New Mexico, crushing perlite which is used for ceiling tiles, brake pads and many other items. Today, it’s joined by several additional CEMCO crushers – a true testament to the company’s belief in the product and its reliability.
Within a couple of years of designing that first crusher, CEMCO introduced the Turbo 54, its first mass-produced model. The small machine handled 80 to 100 tons per hour and sold to diverse customers from Alaska to Mexico solely by word-of-mouth advertising.
In 1970, CEMCO produced its first semi-portable crushers. By the 1990s, the introduction of variable frequency drives made manufacturing portable machines easier and more effective.
As the years passed, CEMCO diligently searched for ways to continue to improve on Neil’s first pencil-sketch concept. The units were adapted so it became easier to get inside to change out parts. They ensured some mechanical parts could be purchased at local stores for customer convenience. They paid attention to the small things that proved to make a big difference. Recognizing the huge radial load and big thrust load cast upon the bearings, CEMCO developed a bearing system that would last longer under those strenuous conditions.
Through three generations of love, sweat and toil, the family has developed a design and product that has stood the test of time and clearly emerged as the leader. Today, CEMCO manufactures eight sizes of crushers and understands the science of crushing in order to customize the machine to each customer’s specific needs. A limestone crusher in Ohio, for example, won’t function as well in Virginia because the limestone differs significantly in chemical composition and hardness. CEMCO understands the differences and reconfigures the internal mechanisms on each unit to best accomplish the job for a particular customer.
“We may not have a degree in chemistry or physics hanging on our walls,” Neil said. “But every day our salespeople are chemists, physicists and engineers – understanding the unique aspects of our customer’s application and designing the ideal components to tackle that challenge. That’s what sets us apart.”
The experience of understanding elements and physics properties, led CEMCO to another venture. How could they leverage their crushing science to positively impact other industries?
As the company grew, so did its pool of experts in mining, engineering, fabricating, machining, aggregate production, power and energy production, agriculture, and contract manufacturing. The extended CEMCO expertise enables the company to meet challenges head-on with the same ingenuity and sweat equity on which the company was founded. The desire to solve problems and find a better way of doing things lives on.
“There is something I learned early on,” Neil said. “One person can’t grow a company. One family can’t grow a company. Employees are the most valuable asset we have and many of our employees have worked with us for years, from generation to generation. It’s their expertise and dedication that allows us to grow the company.”
In the mining industry, CEMCO crushers now take on steel slags, gold and copper. Each customer’s specific refining process for product gradation is met with the exactness that comes from a custom manufacturer. The third largest gold mine in the world in Muruntau, Uzbekistan knows what that means. For more than 17 years, CEMCO crushers have been at work 24/7 at the mine processing 1.3 million tons per month. It’s a vastly different world than when Mason began working in gold mines as a teenager, but his vision helped shape the industry of today.
While mining may have been a natural transition for the company, some new markets have ventured significantly from tradition. About 20 years ago, CEMCO delved into recycling, offering the innovative solutions for crushing cement, glass, ceramic tile, drywall, brick, roofing tiles, copper slag and steel slag. All the while, CEMCO’s focus remained the same: keeping operating costs minimal with low-maintenance, low-energy options. Today, that experience extends directly to small machines tailored to restaurants and bars.
CEMCO’s list of experience and market solutions extend to agriculture and transforming unusable coal and uranium into usable resources as well. Their accomplishments also include innovative custom manufacturing for the oil and gas industries. Overall, CEMCO remains a leader in the aggregate industry, which it has served with dedication for most of its 50 years.
In 1980, Neil took over as President of CEMCO but Mason remained very active in the business until his passing in 1993. Today, Neil continues to serve as the company’s president. It continues to be a family business with his wife Ty Juana and daughter Jennifer both owners in the company. Ty, joined the business fulltime in 1986 as the CFO and served as CEO for the past five years. Jennifer, who first visited the shop as a baby, now serves as vice president. Through high school, she ran forklifts and helped on sales trips – completely involved with the family business. In college, she earned a degree as a mining engineer and, at age 25, became the first female plant manager of a sand and gravel dredging operation for TXI Red River. A decade ago, she brought her knowledge and experience back to the business her grandfather founded. Neil’s other daughter, Aneile, holds an equally important role.
“She is raising the fourth generation of the Hise family,” Neil said. “Hopefully one day they too will join CEMCO.”
The business that Mason started 50 years ago now includes much more than his son, daughter-in-law and granddaughter. The CEMCO team has grown to include others who are as much family as those who descended from Mason. A quarter of all CEMCO employees have been on the staff for more than a decade. The teamwork and dedication shows in the quality of work.
Through it all, Mason’s advice keeps the company on track and devoted to the work ethic he established 50 years ago as he roamed the Southwest doing repairs. “The most important thing is remembering that you’re only as good as your word,” he would say. If somebody made a promise to a customer, they had better keep it. “Tell them the truth and do what you say,” he reminded his family. That message continues to be lived now by the extended CEMCO family as it works to address new problems with the same well-thought and planned solutions that developed a generation ago under the stars.