Overcoming concrete construction obstacles with induction hardened piping
High rise projects progress more successfully when contractors utilize abrasion-resistant pipe delivery systems
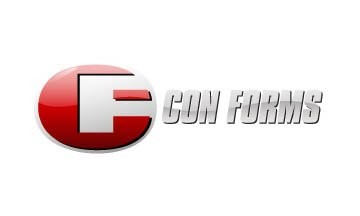
The old axiom about how a chain is only as strong as its weakest link is particularly appropriate when constructing skyscrapers, which require pumping hundreds of tons of concrete through a pipeline system that begins at the hopper of a concrete pump located at grade level and reaching up to the highest floors.
These pipeline systems must therefore be designed to withstand months, even years, of abuse resulting from the extremely abrasive nature of the concrete mix, pumped at pressures of 2,000-3,000 psi at high speed. Any disruption due to a failure in the piping system can be costly – literally halting construction – because concrete will harden quickly and once it does, the piping must be replaced before pouring can resume.
As a result, many concrete pumping contractors are specifying a unique type of induction hardened pipe designed to stand up to abrasion. This pipe is engineered using a proprietary chemistry and an induction hardening process to deliver a gradient wall thickness that begins with an inner wall hardness profile of up to 57HRc on the Rockwell Scale (600 BHN) and slowly tapers to a more ductile outer wall.
By being extremely hard on the inside, the pipe resists even severe abrasion, but the softer outer wall still provides the required toughness to contain the high-pressure and mechanical loading that the pipeline will encounter.
The Shangri-La Project
Designed by Vancouver based architect James Cheng, and under construction by Westbank Projects Corp., the Shangri-La Hotel and condominium tower will rise to 70 stories above the Toronto, Canada, skyline when finished later this year.
The construction management company for the project is 180 University Management Inc. and the site superintendent is James Taylor. The forming contractor is Hardwall Construction Company Limited.
Handling the all-important task of pumping concrete throughout the building is the Amherst Group – Toronto-based experts in the operation of concrete pumps, placing booms, cranes, heavy lift planning and special rigging. The company, founded by Roy Welstead, is currently celebrating its 50th year of operating a fleet of mobile and stationary hydraulic cranes and concrete pumps, placing booms, and deck placers for major construction projects.
Now managed by Welstead’s sons, David, Terry and John and daughter Valerie, Amherst has been credited with successfully completing major projects dating as far back as the Pickering and Darlington nuclear power plants on Lake Ontario, the Montreal Olympic site, the Niagara Tunnel, and hundreds of condominium projects. But as its tallest structure to date, the Shangri La tower posed a particular challenge.
“When you install a concrete pipeline you have to factor in that the higher up you go, the more pressure is created and the greater the wear,” says Paul Turney, Amherst’s concrete pumping manager. “It’s very labour intensive to replace broken pipes, not to mention the delay in construction, so you have to counteract all that by making sure the wall material can stand up when pushing concrete 700 feet vertically.”
“Over the years, I’ve come across dual and triple wall pipes, some European-manufactured pipes, and even encountered some inferior pipe put on a pumping truck by someone trying to save money – but it was all substandard,” continues Turney, who has 25 years of experience in the industry.
According to Turney, he discovered a unique induction hardened pipe from Construction Forms and has specified it ever since.
Based in Port Washington WI, Construction Forms, Inc. (aka ConForms) is a provider of abrasion resistant piping systems. Over the years, they have developed, produced and marketed induction hardened piping products and components for concrete pumping, mining, pulp and paper, power generation and wastewater treatment.
The company’s line of concrete-specific products is anchored by its pipe systems, from 2 inches to 6 inches I.D, which are made abrasion-resistant via a unique induction hardening process. It begins with a steel pipe manufactured to a proprietary chemistry, followed by induction heating, and finally water quenching of the inner surface to create a single wall pipe that can last up to 3-5 times longer than mild steel.
Other piping system elements include boom and lay-down systems, elbows and bends, reducers, back-end kits, ends, adapters, couplings and gaskets. The company’s 5-inch and 6-inch two-bolt high pressure coupling, for example, has been tested to handle 15,000 psi static loading without any sign of failure.
“The induction hardened piping is cost effective because it extends the pipe’s life immensely, as opposed to just soft pipe,” says Turney. “So we specify ConForms for our entire placing systems including our mobile boom-pumps.”
To supply 70-stories worth of concrete for the project, a Putzmeister BSA14000 electric pump will eventually push 35,000 cubic metres of 85mpa-strength concrete through a system of lay-down and vertical pipes of 5-inch diameter and 0.25 to 0.5-inch wall thickness with induction hardened heavy duty ends.
“The Shangri La project is all full-speed pumping all the time, and that wears pipe out even quicker,” Turney says.
Beginning in August 2010, truck-mounted boom pumps supplied concrete from the foundation up to the fifth floor. At that point, Amherst’s crew installed the stationary pump and ConForms pipeline.
“I met with the site superintendent, and he had some concern with the horizontal pipe running into the building using a concrete thrust block to anchor it, so we overcame this issue by burying the pipeline in the lane-way,” explains Turney. “About 150 feet of pipeline was actually encased in the concrete floor slab. When we are finished with the project, we will just fill it up and leave it. But in order to do this we have to trust the integrity of the pipe to last the life of the project.”
Once that problem was overcome, work on the high-rise proceeded quickly.
“We went from the fifth floor and rocketed up to the sixty-eighth floor in just 14 months,” recounts Turney. “We never once pumped on a weekend, and there were only a few pours in the evening because of weather delays or required adjustments to the reinforcing steel.”
Other Amherst projects beside the Shangri La have benefited from induction hardened piping systems. For a recent project for Telus, Canada's third-largest telecommunications company, two separate thirty-story communications towers were to be built within the cramped confines of downtown Toronto next to a busy highway.
“When they excavated the hole we only had ten feet between it and road, with no access on the other two sides. Yet we needed to pour 55,000 metres of concrete,” recalls Turney. “I noticed an empty lot across the highway and suggested that we dedicate that space for ready mix trucks and the stationary pump, and then bury the ConForms pipeline under the road. That way we didn’t have to deal with closing the road every time the trucks needed to unload concrete.”
Amherst installed three piping lines under the highway, the longest one extending 800 feet horizontally before heading up 30 stories to a 110-foot-radius placing boom.
“When pipes are underground for a long distance you’re taking a chance because if a problem crops up, you can’t access it,” notes Turney. “If the system fails, whatever concrete is in the pipe is going to harden by the time you get to it. So we relied on the induction hardened pipe we’ve had success with in the past.”
Amherst was awarded a construction industry Innovation Award on that project in recognition of time and cost savings.
“It’s an example of how the concrete pumping industry has become more sophisticated and technically savvy over the years, says Valerie Brennan, Amherst’s Vice-President and daughter of founder Roy Welstead. “With the help of ConForm’s induction hardened pipe, whatever concrete placement challenges are thrown at us, we will find a way to overcome them.”