A North American first in highway reconstruction
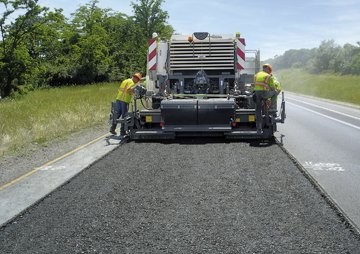
Continuously increasing traffic volumes and the loads imposed by heavy-vehicle traffic had left the pavement surface of Virginia’s very busy I-81 covered with alligator cracks, wheel ruts and patches where minor repairs had been carried out. In previous years, traffic was kept running on this divided four-lane highway by carrying out extensive repair operations.
In the spring of 2011, however, a 6-km-long stretch on the right-hand truck lane required complete rehabilitation due to structural damage and an inadequate load-bearing capacity. The left-hand passenger car lane, which was subject to lower loads, was to be rehabilitated by cold recycling to a depth of 12 cm.
This highly challenging construction project involved the use of as many as three different recycling methods – making this a unique rehabilitation project.
During the rehabilitation of the truck lane, the compact dimensions of the Wirtgen Group machines minimized the disruptions to traffic: vehicles were guided past the job site on the adjacent, left-hand lane, thus maintaining a continuous flow of traffic.
W 210 and W 2100 large milling machines removed the entire asphalt material down to a depth of 25 cm in a single pass. The LEVEL PRO levelling system specifically designed by Wirtgen for use in cold milling machines made light work of this difficult task, precisely maintaining the selected milling depths.
Trucks seamlessly transported the reclaimed granulated material to the KMA 220 mobile mixing plant for recycling.
A Wirtgen WR 2400 cold recycler with a working width of 2.40 m was at the ready for the soil stabilizing operation to be carried out next, which would restore the subgrade to the required bearing capacity.
At the same time, the cold recycling mixing plant was busy recycling the reclaimed asphalt material in an “in-plant” process for full reuse. Its mobile mixing design enabled the mixing plant to be set up in the immediate vicinity of the construction site, which not only reduced the distance to be covered by the transport trucks, fuel consumption rates and CO2 emissions, but also resulted in a significant reduction of the overall construction costs.
Asphalt pavers placed the material on the stabilized subgrade as a 20-cm-thick layer that was then effectively compacted by tandem rollers from Hamm. Finally, a 5-cm-thick asphalt layer was placed on top.
The rehabilitation of the left-hand lane was then begun without delay. As it had mostly been used by passenger cars in the past, it required less extensive rehabilitation methods. In a first step, the W 2100 milled off the 5-cm-thick surface course at a gradient of 2 percent.
After pre-spreading 1 percent pure cement, the Wirtgen 3800 CR cold recycler – equipped with a 3.8-m-wide, integrated paving screed – gained centre stage for the “in-situ” processing of the traffic lane.
It is a major advantage of this process that neither the source material nor the recycled construction material mix require any transport effort. The cold recycler milled off and granulated the damaged asphalt layer down to a depth of 12 cm in a single pass – while the milling and mixing rotor mixed in foamed bitumen, cement and water at the same time.
The 3800 CR then paved and pre-compacted the recycled mix by means of the integrated Vögele paving screed. Final compaction was carried out by tandem and rubber-wheeled rollers from Hamm. The rehabilitation work was completed by paving an asphalt course on top of the recycled base.
Ground-breaking, cold recycling technologies from Wirtgen were the key to success in this showcase project. Traffic on the I-81 flowed smoothly again after a short construction period. On the two roadways, optimal structural integrity for excellent durability was accomplished in an economical, resource-efficient and environmentally-friendly manner.
As VDOT Commissioner Greg Whirley emphasized: “Savings on the I-81 in-place pavement recycling project go beyond time, money and materials. The reduced transports for old and new material saved fuel. Safety for drivers and road workers on the project was also increased because work-zone congestion was reduced. This section of rebuilt pavement also will be stronger from bottom to top, extending its service life and reducing the need for such complex maintenance for many years.”