Slag recycler uses dust suppression cannon to meet air quality regulations
Industrial atomized mist technology employed to contain fugitive dust emissions and control runoff
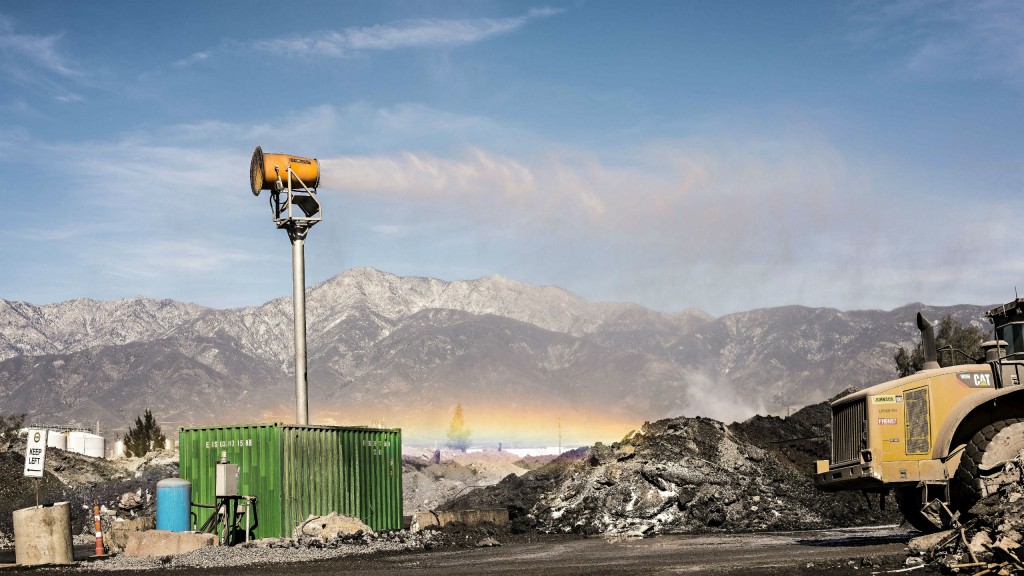
Tervita, the Calgary-based environmental solutions firm, is operating a slag recycling plant in California using industrial atomized mist technology to contain fugitive dust emissions and control runoff to satisfy strict state air quality regulations. Tervita was tasked with controlling dust while conserving water in an area known for high winds, Rancho Cucamonga, CA. The firm accomplished that goal by integrating a tower mounted DustBoss DB-60 with a modified shipping container in an innovative design that stabilizes the unit and protects electronics. The result is a drastic reduction in fugitive dust emissions, improved regulatory compliance and better community relations.
In 2012, the Gerdau Corporation chose Tervita to take over operations of the slag processing plant, servicing the company’s long steel mill located approximately 0.25 miles (0.4 k) away. Facing a transition that required updated equipment in a strict regulatory environment, Tervita managers worked closely with the South Coast Air Quality Management District (SCAQMD) and local leaders to create an air quality management plan that made the operation compliant and more efficient.
Tervita receives approximately 300 tons (272 mt) of material a day in 10 to 14 “heats” (dump truck loads), which are offloaded into a 200-foot-deep by 100-foot-wide (61 meters x 30.5 meters) storage area separated into two sections. Nearly a third of the temperature of the surface of the sun, newly delivered slag -- approximately 2500º to 3000ºF (1,370º to 1,650º C) -- is wetted, cooled, mixed and cured by a combination of water, front loader and time.
“When we installed the new state-of-the-art crusher, we streamlined the recycling process into a faster operation that is dust-free because of the bag house filtration system,” said Carson Swartz, Operations Supervisor for Tervita. “But the storage and cooling area was a big issue. Whether offloading, churning or moving the slag to the crusher, it’s constantly being disrupted, causing a lot of dust.”
Prior to installing the DB-60, the company tried using the moveable sprinkler irrigation system left in place by the previous operators. Tervita found that the sprinkler system only saturated the surface material, which caused large amounts of runoff and did not properly address the fugitive dust.
Managers at Tervita heard from colleagues in the steel industry about the use of atomized mist technology at another slag recycling operation. The company strategically placed a 20-foot-long by 8-foot-wide by 8.5-foot-tall (6 m x 2.4 m x 2.5 m) shipping container in the storage and cooling area. Working with DCT technicians, the container was reinforced with a heavy-duty steel frame and modified to mount a 12-foot (3.65 meters) tall steel tower topped by the DB-60 equipped with a 359º oscillation system, making the total height from the ground approximately 28 feet (8.5 meters). Inside the container, a touch screen panel is mounted on the wall that allows operators to control the elevation, oscillation arc, booster pump pressure, fan output and water volume. Many of these functions can also be modified outside the container by remote control.
Since the water used by Tervita for dust suppression is non-potable, it is first sent through an in-line 30 mesh, 595-micron filter before being delivered to the booster pump, where the water pressure is raised from 10 PSI (0.68 BAR) up to 160 PSI (11.03 BAR), with a potential maximum of 250 PSI (17.23 BAR). Pumped through a 1.5-inch (38.10 mm) hose to a circular brass manifold, the water is forced through 30 atomizing spray nozzles, which fractures it into millions of tiny droplets. The mist is then propelled by a powerful 25 HP electric fan that produces 30,000 CFM (849.50 CMM) of airflow through a specialized cylindrical barrel design. Atomized droplets are launched in a 200-foot-long (60 meter) cone at an adjustable 0 to 50° angle, covering a total area of 125,000 square feet (11,613 square meters) when using the full 359º oscillation.
Atomization introduces more droplets into the air than hoses or sprinklers, using a fraction of the water volume. Because the mist is propelled by a fan rather than water pressure, the DB-60 uses only about 25 GPM (94.5 lpm) to cover the area, as opposed to an industrial irrigation sprinkler system that can require up to 500 GPM (1,893 lpm) to adequately service the same area.Not only do the atomized droplets capture airborne particles, once they land they also quench the storage piles, offering surface suppression with far less runoff and product loss.
Due to the use of atomized mist, the facility has dramatically reduced the volume of water needed for dust management, making more water available for other parts of production in the plant, thus promoting sustainable overall usage for the entire facility. With fugitive dust levels compliant to SCAQMD regulations, Tervita achieved the goals set for the project and successfully applied a new technology that could be used in other locations and applications.
“As much as we run the machine, we’ve been impressed by how well it’s held up,” Swartz added. “Since the installation, the couple of times we’ve called DCT, they were very responsive and even came out to visit just to see the setup. Their service matches the quality of the equipment.”