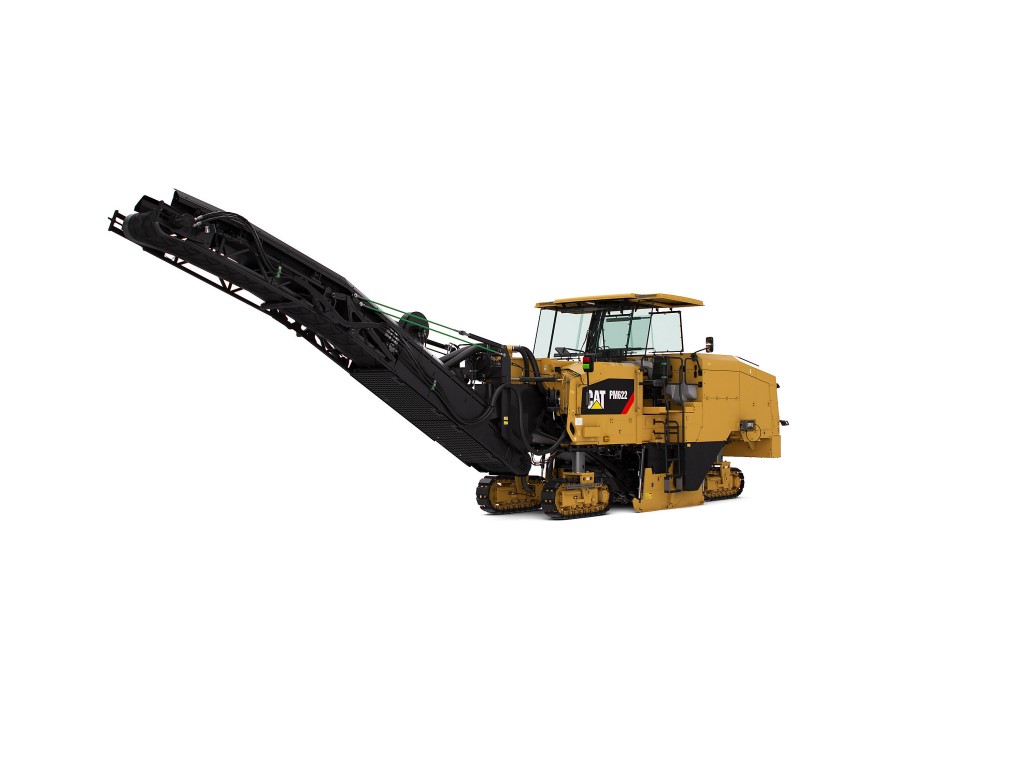
Caterpillar Inc. has announced the availability of the PM620 and PM622 Cold Planers. The machines are high-production, highly maneuverable half-lane milling machine that perform controlled full-depth removal of asphalt and concrete pavements in a single pass. Operating weight for the PM620 is approximately 33 330 kg (73,260 lb) and the PM622 is approximately 33 900 kg (74,580 lbs). Transport weight for the PM620 is approximately 29 400 kg (64,680 lb), and the PM620 is approximately 30 000 kg (66,140 lb).
The PM620 and PM622 are powered by a Cat® C18 ACERT™ engine, a turbocharged, 6-cylinder diesel engine that provides 470 kW (630 hp) of gross power. The C18 engine meets U.S. EPA Tier 4 Final and EU Stage IV emission standards. The engine is iso-mounted to reduce vibration and increase operator comfort.
The Automatic Engine Speed Control feature allows the engine to optimize output to match the load, reducing excessive fuel consumption and wear on the engine.
The turbocharged air-to-air aftercooling system provides high horsepower with increased response-time while keeping exhaust temperatures low, which generates significant improvements in airflow. This increases efficiency and reduces emissions.
The cooling system provides cool intake air in order to maximize fuel efficiency and minimize emissions. An on-demand variable speed fan draws ambient air from the top of the engine hood and through the cooling package, keeping the engine compartment cool. Heated air exits from the rear of the machine, directed away from the operator’s station for greater operator comfort.
Undercarriage and Drive System
The PM620 and PM622 utilize a four-post design. The leg posts feature an auto-leveling function that provides smooth height adjustment without stepping.
The machines are fully hydrostatically driven by two variable displacement propel pumps supplying oil to variable displacement motors on each track. Drive motors are piston-type and automatically control displacement to provide maximum torque for work or greater speed for moving around the job site. A propel lever/steering joystick provides infinite control of the travel speed within the range.
The machines have a robust propel system with a diagonal cross flow design that provides exceptional traction. The pumps drive opposing track motors, front to back and side to side, to ensure the machine has power across the center of gravity of the machine. In extreme conditions, automatic traction control minimizes slippage by providing more power to tracks that grip.
There are several automated functions to simplify operation. The operator’s platform has a ‘hold’ button to stop the machine and pause various functions while making truck interchanges or job stops. It returns to previous working speed and functions when deactivated. There is a speed limit to allow the operating speed to set to ensure consistent operations. The machines are equipped with position sensing cylinders in the posts and hydraulic systems, providing basic machine function improvements such as service height indications and rear leg auto-stop. It also enables the optional Cat Grade Control system to include additional capabilities.
The drive tracks are based on durable, proven Caterpillar designs and components. Track tension automatically adjusts to ensure optimum operation. Track assemblies are 1788 mm (70.4") long, 305 mm (12") wide and feature replaceable, bolt on polyurethane track pads for long service life.
Four-mode steering is standard. An electronic control module processes inputs from the sensors on the front and rear tracks along with input from the steering selector controls. It provides precise simultaneous track movement in the cab and coordinated steering modes and automatically realigns the rear tracks to center when the front-tracks-only steering mode is selected. In the coordinated mode, the inside turning radius is a tight 2.00 m (6' 5") providing exceptional maneuverability in confined spaces.
A true-tracking alignment function provides greater steering precision, smoother cornering and reduced track wear. This function makes small adjustments to the alignment of individual tracks to ensure that the tracks are travelling in the optimal direction to make the desired maneuver without dragging a track or shorting a radius. This extends track pad and undercarriage component life.
The operator’s station features dual operating controls, including joystick steering/propel lever, upper conveyor controls and rear track steering controls. Ergonomic instrumentation layout has been designed for comfort and ease of use. A touchscreen display is visible in day or night conditions, and keypads are backlit for comfortable low light operation. Keypad controls are positioned within easy reach for the operator. A large storage locker is standard. Options that add comfort for the operator include suspension seats and a hydraulically operated canopy. The canopy can deploy and retract to a storage position without disrupting operation. The canopy can be equipped with optional front and rear windscreens that protect the entire width of the operator station.
The touchscreen display provides easy-to-read gauges, function indicators and warning indicators to keep the operator informed of machine operation and vital systems. It also displays video from the optional remote cameras if equipped. An optional second display can provide an additional monitor for machine functions.
The computerized monitoring system includes several electronic control modules (ECMs) that constantly monitor system pressures and engine conditions with multiple modes of operation. The system can provide self-diagnostics and fault codes to the touchscreen display.
The machines are equipped with excellent perimeter lighting for enhanced low light operation. The halogen lights are positioned around the machine to provide light to work areas. An upgrade to LED lights is available. The operator’s platform has floor lighting that activates upon button press from any control station to provide visibility when accessing the machine in low light conditions.
An optional remote camera system is available. The cameras are positioned to provide the operator with views to the front and/or rear of the machine. Video is displayed on the primary touchscreen. Up to two optional magnetic mounting cameras are available.
Cutting System
The cutting chamber features a design that streamlines material flow, reduces wear on the chamber, and has enhanced flush cutting capability. Side plates move via independent hydraulic cylinders that are equipped with position sensors. This ensures that the side plates float at the proper level, and eliminates binding. It also eliminates the need for a wire (yo-yo) sensor by enabling the entire length of the side plate to function as an averaging ski for grade matching. A hydraulically operated anti-slab device prevents slabbing of the road surface. It also protects the collecting conveyor and ensures an optimum discharge opening to the rotor chamber. The chamber also features a right side hinged door to provide service access to the rotor. The moldboard, side plates and anti-slab device all feature raise, lower, float and hold functions.
The rotor drive system features a dry clutch driving a planetary gear reducer, an efficient and reliable system of applying rotor power to the pavement. The clutch is coupled to the engine and is hydraulically actuated by the keypad controls on the operator’s console. Three cutting speeds are available to match the best rotor RPM and torque with the job site conditions, and are controlled electronically from the keypad on the operator’s control console.
Automatic Load Control is a standard feature to enhance machine productivity while milling. An ECM continually evaluates engine rpm and controls propel speed as required to maintain peak performance for maximum output.
Two five-rib, high-tensile-strength belts drive the rotor through a drum drive gear reducer. The hydraulically powered automatic drive belt tensioner prevents slipping and reduces maintenance.
The PM620 is equipped with a 2010 mm (79") wide high production rotor and the PM622 is equipped with a 2235 mm (88") wide high production rotor. The maximum cutting depth is 330 mm (13"). The rotor is equipped with durable three-piece, quick release tool holders and carbide-tipped cutting bits arranged in a chevron pattern for maximum breakout force. Optional Cat Diamond Bits are available for greater cutting performance during certain applications.
The quick release conical tool holders feature a tapered fit, maintaining tightness in the holder base. The mandrel features large, replaceable, carbide-faced loading paddles to effectively move milled material onto the collecting conveyor, resulting in higher production and less wear on the inside of the rotor chamber and cutting tools. Triple-tree cutting bit placements on rotor end cutters provides optimum bit spacing to clean up loose material and reduces wear on drum when maneuvering in the cut.
Optional Cat Diamond Bits offer the ultimate in cutting performance. The bits last up to 80 times longer than conventional carbide bits, extending periods between stops for bit maintenance. This increases production and reduces operating costs by facilitating more uptime and reducing the need to purchase and store pallets of carbide bits. Cat Diamond Bits are sharper than conventional carbide bits, reducing drag on the cutting system and allowing the machine to cut at faster speeds, increasing production. Reduced drag also decreases fuel consumption, vibration to the operator and machine wear, which lowers operating and maintenance costs.
Cat Grade Control Option
The PM620 and PM622 can be equipped with integrated Cat Grade Control. The 2D-capable/3D-ready grade and slope system automatically controls rotor depth and cross slope to a preset cutting depth, and can be enhanced for full 3D control with the addition of optional equipment. The base system is fully integrated with the machine, providing easier, more precise operation and better system protection. The system can be configured with contacting or non-contacting grade sensors including Cat sonic sensors and mounting hardware, the side plate position or optional inboard ski. The machine can be set up to control grade on both sides using any combination of sensors. Or, the machine can be set up to control grade on one side of the machine and slope on the other. The system allows you to change the sensor arrangement during operation with simple commands, as work site application requires.
The position sensing technology coupled with the Cat Grade Control system provides the machine with functions such as an automatic plunge cut feature that eases the rotor into the start of the cut. The machines also have a ramp-in, ramp-out capability to provide a gradual, sloped entry or exit from the cut. An auto-jump feature allows the machine to exit a cut, clear an obstacle such as a manhole cover or grate, and re-enter the cut at the previously set depth with use of a single button.
A cross communication function allows the operator to view and change settings of control boxes located on the opposite side of the machine. This provides the operators with a means to control both sides of a job from a single location. The system also provides a cross-coupling function that when an adjustment is made to the grade or slope of one side of the machine, the opposite side will automatically adjust based on the command parameters. Continual read-out for rotor depth and cross-slope is displayed on each control box and is visible in light or dark conditions.
Sonic grade control sensors can be easily positioned on each side and provide a consistent accuracy to ± 3 mm (1/8").
Conveyor System
The collecting conveyor is driven by a high-torque hydraulic motor to ensure maximum efficiency. A large chamber discharge opening clears out the cutter box quickly to maintain high production. The seamless collector belt features 32 mm (1.25") high cleats and is 850 mm (33.5") wide to clear out the cutter box effectively and control fine particles. An optional grease tensioning system uses a grease cylinder to adjust tension and tracking on the belt rather than an adjustable screw. The cylinder makes the adjustment easier and reduces crew exposure to the spinning belt. A traditional screw adjustment design is also available.
A standard water spray system lubricates the conveyor belt and helps control dust. A centrifugal pump supplies water to spray nozzles in the cutting chamber. The nozzles focus water spray in a flat fan pattern to the rotor for better cooling of cutting bits. Nozzles are easily removed for inspection and replacement without tools. The system features an automatic function that operates only when the rotor is engaged and machine is moving forward, which conserves water. The system is triple filtered, and includes a gauge to monitor water pressure, a low water level indicator and water control valves to conserve water usage. An onboard winterization system is also included, providing a simple method to purge waterlines with pressurized air.
The 3400 L (898 gal) water tank can be filled from standard wide fill openings on the top of the machine or the standard ground level port at the rear of the machine. There is also an optional side fill port. This enables adding water while the machine is operating. An optional water transfer pump is available to facilitate additional filling options.
An additional water spray system can be fitted as an option for greater lubrication, cooling and dust reduction during heavy-duty applications. This system includes an additional water pump, a second spray bar located in the rotor chamber housing, and extra spray nozzles on the collecting conveyor.
The hydraulically controlled front loading conveyor features height adjustment for raise and lower and two cylinders for a 60 degree swing to the left and right of center that can be controlled from the operator’s station or at two ground level control stations. It is equipped with upper aluminum covers for added protection against material spills and blowing of fine materials. The loading conveyor can also be hydraulically folded downwards, reducing machine dimensions during transportation.
The seamless loading conveyor belt features 32 mm (1.25") high cleats and is 850 mm (33.5") wide. It offers long service life and excellent control of fine particles. Variable belt speed provides adjustable control of the loading conveyor to ensure proper discharge.
An optional dust abatement system is available. The system utilizes a vacuum that pulls dust from the collecting conveyor and the transitional zone between the collecting and loading conveyors. The dust is ejected through the loading conveyor along with the discharge material.
Optional Equipment
Options include a diamond bit cutting drum and bits, a self-powered canopy, canopy windscreens, additional touchscreen displays, Cat Grade Control, inboard averaging ski with position sensing cylinder, suspension seats, remote cameras, additional water spray system, dust abatement vacuum system, a rotor turning attachment, a high-pressure wash down system, bucket trays for cutter bit bucket storage, a high capacity water tank refilling pump and an electric refueling pump.
Serviceability
Large doors open wide to provide excellent access to the engine, emissions package, air filter, hydraulic components and daily service points.
The computerized monitoring system includes Electronic Control Modules (ECMs) that continually monitor system pressures and engine conditions with multiple modes of operation. The system can provide self-diagnostics and provide fault code to the touchscreen display.
The machines feature long service intervals to reduce owning and operating costs. Engine oil service is every 500 hours, and hydraulic oil service is every 3,000 hours if oil sampling is not conducted, up to 6,000 hours if scheduled oil sampling occurs.
An auxiliary electric pump drive provides an emergency hydraulic flow that allows a disabled machine to manage some machine functions and be towed away from the work area to ensure that the disabled machine will not disrupt the continuation of work.
The hydraulic rotor service door opens wide for convenient access to rotor for inspection and tool maintenance. The engine-mounted air compressor and cutting bit removal tools make changing cutting tools quick and easy. An optional rotor-turning attachment is available to turn the rotor during cutter bit replacement.
Hydraulic hoses are held neatly in place with polyurethane routing blocks. The blocks separate hoses helping ensure that they do not rub on one another to provide long life and high reliability.
Wiring for the electrical system is protected by nylon-braided wrap. All-weather connectors ensure electrical system integrity. Electrical wiring is color-coded, numbered and labeled with component identifiers to simplify troubleshooting.
Product Link™ provides accurate, timely and useful information about the location, utilization and condition of your equipment. The system streamlines diagnostic efforts, maintenance scheduling, and costs by providing communication flow of vital machine data and location information between the dealer and customer. Optional configurations are available.
Two maintenance-free Cat batteries that are specifically designed for maximum cranking power and protection against vibration provide the 24-volt electrical system. The batteries are located at the rear of the machine and are easily accessible at ground level.
Other features that simplify service include leak-resistant O-ring face seal hydraulic fittings, grouped quick-connect hydraulic test ports, scheduled oil sampling ports, visual sight gauges and remote grease points.